A method for separating zinc and iron in a zinc hydrometallurgy process
A technology of hydrometallurgy and separation method, applied in the field of hydrometallurgy, which can solve the problems of slag environmental pollution, low metal recovery rate, and high iron removal efficiency, and achieve simplified process, high metal recovery rate, and low iron content Effect
- Summary
- Abstract
- Description
- Claims
- Application Information
AI Technical Summary
Problems solved by technology
Method used
Examples
Embodiment 1
[0025] The method for separating zinc and iron in the hydrometallurgy process has the following specific steps:
[0026] (1) Zinc concentrate is roasted at a low temperature of 850~900°C for 5 hours to obtain zinc calcined sand;
[0027] (2) 100kg of zinc calcined sand, liquid after hydro-smelting zinc electrolysis (containing 45g / L zinc, 160g / L sulfuric acid) and the weak acid liquid produced in step (3) (containing 150g / L zinc, 0.8g / L iron L) Perform neutral leaching to produce intermediate leaching solution containing less than 20mg / L of iron (containing 152g / L of zinc, 0.6g / L of copper, and 15mg / L of iron) and intermediate leaching residue (containing 21wt% of zinc, containing Iron 29wt%); the specific process is: the zinc calcine, the liquid after electrolysis of zinc hydrometallurgy and the weak acid liquid produced in step (3) according to the feed ratio of 1:4:2Lkg / L / L, at a temperature of 60°C Neutral leaching for 2 hours under conditions;
[0028] (3) Mix 61kg of m...
Embodiment 2
[0034] The method for separating zinc and iron in the hydrometallurgy process has the following specific steps:
[0035] (1) Zinc concentrate is roasted at a low temperature of 850~900°C for 5 hours to obtain zinc calcine;
[0036] (2) 100kg of zinc calcined sand, liquid after electrolysis of zinc hydrometallurgy (containing 45g / L of zinc, 160g / L of sulfuric acid) and weak acid liquid produced in step (3) (containing 151g / L of zinc, 0.3g / L of iron L) Perform neutral leaching to produce intermediate leaching solution containing less than 20mg / L iron (containing 153g / L zinc, 0.5g / L copper, 8mg / L iron) and intermediate leaching residue (containing 23wt% zinc, containing Iron 27wt%); the specific process is: the zinc calcine, the liquid after electrolysis of zinc hydrometallurgy and the weak acid liquid produced in step (3) according to the feed ratio of 1:3.6:2.5Lkg / L / L, at a temperature of 70 Neutral leaching for 1.5h at ℃;
[0037] (3) Mix 65kg of medium leaching slag obtained ...
Embodiment 3
[0043] The method for separating zinc and iron in the hydrometallurgy process has the following specific steps:
[0044] (1) Zinc concentrate is roasted at a low temperature of 850~900°C for 5 hours to obtain zinc calcined sand;
[0045] (2) Neutral leaching of 100kg of zinc calcined sand, liquid after electrolysis of zinc hydrometallurgy, and weak acid liquid produced in step (3), to produce intermediate leaching liquid and intermediate leaching residue with iron content less than 20mg / L; the specific process is : The zinc calcined sand, the liquid after electrolysis of zinc hydrometallurgy and the weak acid liquid produced in step (3) are neutrally leached for 2.5 hours at a temperature of 65°C according to the feeding ratio of 1:3:3Lkg / L / L;
[0046] (3) Mix the 100kg medium leaching residue obtained in step (2) with the extracted indium and copper solution produced in step (6) for weak acid leaching, and produce a weak acid solution with an iron content of less than 1g / L; t...
PUM
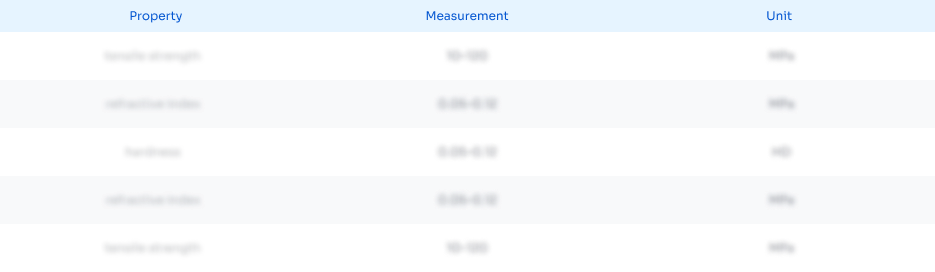
Abstract
Description
Claims
Application Information

- R&D
- Intellectual Property
- Life Sciences
- Materials
- Tech Scout
- Unparalleled Data Quality
- Higher Quality Content
- 60% Fewer Hallucinations
Browse by: Latest US Patents, China's latest patents, Technical Efficacy Thesaurus, Application Domain, Technology Topic, Popular Technical Reports.
© 2025 PatSnap. All rights reserved.Legal|Privacy policy|Modern Slavery Act Transparency Statement|Sitemap|About US| Contact US: help@patsnap.com