Shape memory intrinsic type self-repairing material as well as preparation method and application thereof
A self-healing material and intrinsic type technology, applied in the field of intelligent polymer materials, can solve problems such as the depletion of repairing agent, and achieve the effect of high repair rate, simple repair process, and high repair efficiency
- Summary
- Abstract
- Description
- Claims
- Application Information
AI Technical Summary
Problems solved by technology
Method used
Image
Examples
Embodiment 1
[0037] Add 15 parts of polyε-caprolactone diol monomer with a number average molecular weight of 1500 and 3.5 parts of hexamethylene diisocyanate into a 250ml three-necked flask with mechanical stirring, and react at 65°C with tetrahydrofuran as a solvent 1h, add 4.3 parts of styrene-butadiene-styrene block copolymer and 1 part of multi-walled carbon nanotubes with a diameter of 10-20nm, stir at 65°C for 1h, then add 3 parts of 2-(4-hydroxy -2,2,6,6-Tetramethylpiperidine-1-oxy)-N-(2-hydroxyethyl)-2-methylpropionamide, 0.1 part of 2-methyl-1-(4-methyl Thiophenyl)-2-morpholinyl-1-propanone and 0.7 parts of trimethylolpropane tris(3-mercaptopropionate) were reacted at 65°C for 0.5h, and the resulting mixed solution was ultrasonicated for 10min and then poured into a rectangle Molds were stripped of THF at 60°C to form approximately 1 mm thick sheets. Heat the obtained rectangular sheet to 60°C and apply stress to make the longitudinal strain of the rectangular sheet reach 500%, ...
Embodiment 2
[0039] Add 20 parts of polyε-caprolactone diol monomer with a number average molecular weight of 2000 and 3.5 parts of hexamethylene diisocyanate into a 250ml three-necked flask with mechanical stirring, and react at 65°C with tetrahydrofuran as a solvent 1h, add 5.3 parts of styrene-butadiene-styrene block copolymer and 1.2 parts of multi-walled carbon nanotubes with a diameter of 10-20nm, stir at 65°C for 1h, then add 3 parts of 2-(4-hydroxy -2,2,6,6-Tetramethylpiperidine-1-oxy)-N-(2-hydroxyethyl)-2-methylpropionamide, 0.1 part of 2-methyl-1-(4-methyl Thiophenyl)-2-morpholinyl-1-propanone and 0.7 parts of trimethylolpropane tris(3-mercaptopropionate) were reacted at 65°C for 0.5h, and the resulting mixed solution was ultrasonicated for 10min and then poured into a rectangle Molds were stripped of THF at 60°C to form approximately 1 mm thick sheets. Heat the obtained rectangular sheet to 60°C and apply stress to make the longitudinal strain of the rectangular sheet reach 500...
Embodiment 3
[0041] Add 30 parts of polyε-caprolactone diol monomer with a number average molecular weight of 3000 and 3.5 parts of hexamethylene diisocyanate into a 250ml three-necked flask with mechanical stirring, and react at 65°C with tetrahydrofuran as a solvent 1h, add 7.3 parts of styrene-butadiene-styrene block copolymer and 1.7 parts of multi-walled carbon nanotubes with a diameter of 10-20nm, stir at 65°C for 1h, then add 3 parts of 2-(4-hydroxy -2,2,6,6-Tetramethylpiperidine-1-oxy)-N-(2-hydroxyethyl)-2-methylpropionamide, 0.1 part of 2-methyl-1-(4-methyl Thiophenyl)-2-morpholinyl-1-propanone and 0.7 parts of trimethylolpropane tris(3-mercaptopropionate) were reacted at 65°C for 0.5h, and the resulting mixed solution was ultrasonicated for 10min and then poured into a rectangle Molds were stripped of THF at 60°C to form approximately 1 mm thick sheets. Heat the obtained rectangular sheet to 60°C and apply stress to make the longitudinal strain of the rectangular sheet reach 500...
PUM
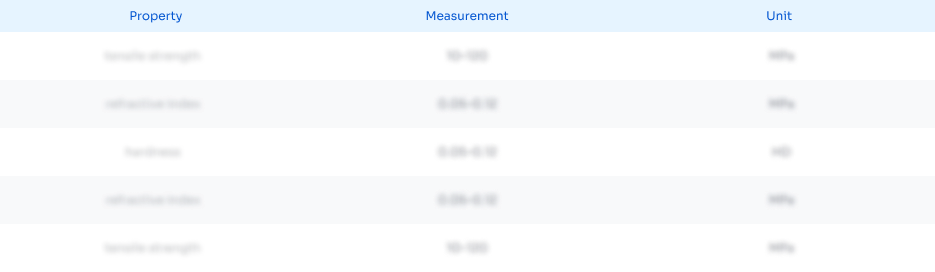
Abstract
Description
Claims
Application Information

- R&D
- Intellectual Property
- Life Sciences
- Materials
- Tech Scout
- Unparalleled Data Quality
- Higher Quality Content
- 60% Fewer Hallucinations
Browse by: Latest US Patents, China's latest patents, Technical Efficacy Thesaurus, Application Domain, Technology Topic, Popular Technical Reports.
© 2025 PatSnap. All rights reserved.Legal|Privacy policy|Modern Slavery Act Transparency Statement|Sitemap|About US| Contact US: help@patsnap.com