Preparation method of high-performance fluoride rubber/silicone rubber cable sheath material
A cable sheath and silicone rubber technology, applied in the direction of insulating cables, rubber insulators, cables, etc., can solve the problem of limited high and low temperature environment tolerance, poor aging resistance, and unsatisfactory high and low temperature resistance of cable sheaths, etc. Problems, achieve excellent heat resistance, overcome low temperature resistance and poor processability, and increase density
- Summary
- Abstract
- Description
- Claims
- Application Information
AI Technical Summary
Problems solved by technology
Method used
Examples
Embodiment 1
[0023] The preparation method of a kind of high-performance fluorine rubber / silicone rubber cable sheath material that the present invention proposes comprises the following steps:
[0024] S1, by weight 100 parts of fluororubber, 50 parts of silicone rubber, 15 parts of epoxy acrylate rubber, 20 parts of hydrogenated nitrile rubber, 2 parts of maleic anhydride grafted polyethylene and 12 parts of silicone rubber grafted methacrylic acid -2,2,2-Trifluoroethyl ester was added to a double-roller mill for mixing, and a mixed rubber was obtained after debinding, wherein the mixing temperature was 35°C and the mixing time was 15 minutes;
[0025] S2. Set the temperature of the kneader to 55°C, add 100 parts of primary rubber by weight, then add 20 parts of carbon nanotubes, 2 parts of stearic acid modified diatomite, 15 parts of calcium silicate, 5 parts 1 part of polyaniline nanofiber, 10 parts of sepiolite fiber and 1 part of calcium hydroxide were mixed for 5 minutes, and then 1...
Embodiment 2
[0028] The preparation method of a kind of high-performance fluorine rubber / silicone rubber cable sheath material that the present invention proposes comprises the following steps:
[0029] S1, by weight, 100 parts of fluororubber, 35 parts of silicone rubber, 30 parts of epoxy acrylate rubber, 10 parts of hydrogenated nitrile rubber, 5 parts of maleic anhydride grafted polyethylene and 3 parts of silicone rubber grafted methacrylic acid -2,2,2-Trifluoroethyl ester was added to a double-roller mill for mixing, and a mixed rubber was obtained after debinding, wherein the mixing temperature was 45°C, and the mixing time was 5 minutes;
[0030] S2. Set the temperature of the kneading machine to 65°C, add 100 parts of primary rubber by weight, and then add 5 parts of carbon nanotubes, 15 parts of stearic acid modified diatomite, 5 parts of calcium silicate, 20 Parts of polyaniline nanofibers, 2 parts of sepiolite fibers and 8 parts of calcium hydroxide were mixed for 1 min, then 5...
Embodiment 3
[0033] The preparation method of a kind of high-performance fluorine rubber / silicone rubber cable sheath material that the present invention proposes comprises the following steps:
[0034] S1, by weight 100 parts of fluororubber, 46 parts of silicone rubber, 21 parts of epoxy acrylate rubber, 18 parts of hydrogenated nitrile rubber, 3 parts of maleic anhydride grafted polyethylene and 11 parts of silicone rubber grafted methacrylic acid -2,2,2-Trifluoroethyl ester is added to the double-roller open mill for mixing, and a mixed rubber is obtained after debinding. The mixing temperature is 33°C, and the mixing time is 13 minutes. The double-roller The roller distance of the mill is 3.5mm;
[0035] S2. Set the temperature of the kneader to 60°C, add 100 parts by weight of the primary mixing rubber parked at room temperature for 24 hours, then add 16 parts of carbon nanotubes, 6 parts of stearic acid modified diatomite, 13 Parts of calcium silicate, 7 parts of polyaniline nanofi...
PUM
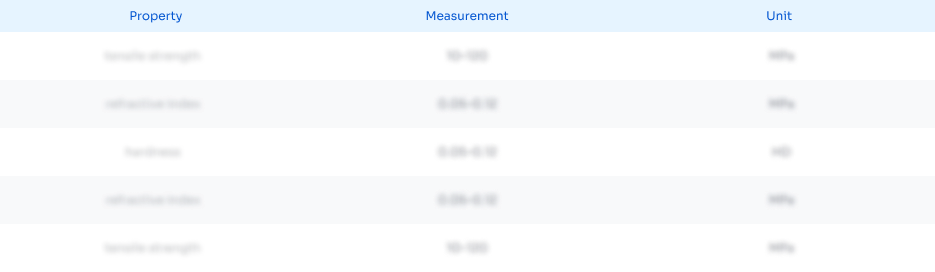
Abstract
Description
Claims
Application Information

- R&D Engineer
- R&D Manager
- IP Professional
- Industry Leading Data Capabilities
- Powerful AI technology
- Patent DNA Extraction
Browse by: Latest US Patents, China's latest patents, Technical Efficacy Thesaurus, Application Domain, Technology Topic, Popular Technical Reports.
© 2024 PatSnap. All rights reserved.Legal|Privacy policy|Modern Slavery Act Transparency Statement|Sitemap|About US| Contact US: help@patsnap.com