Method for separating nickel, copper and iron from electroplating sludge
A technology for electroplating sludge and nickel-copper-iron, which is applied in the direction of improving process efficiency, can solve the problems such as the leaching rate of copper and nickel needs to be improved, and achieves the effect of solving difficult iron removal, good decomposition effect and simple operation.
- Summary
- Abstract
- Description
- Claims
- Application Information
AI Technical Summary
Problems solved by technology
Method used
Examples
Embodiment 1
[0015] Electroplating sludge composition: Ni14.14%, Cu1.0%, Zn9.09%, Co0.24%, Fe5.21%, Mg0.09%, Mn0.03%, Al0.08%, Cd0.07%, S23.86%.
[0016] Add 500g of electroplating sludge and 2500g of sulfuric acid solution with a concentration of 90g / L into the reaction kettle, add 0.6g of lignosulfonate, feed industrial oxygen, keep the oxygen partial pressure in the kettle at 0.7MPa, leaching temperature at 150°C, and control the pH of the leaching solution In 1.5, the leaching time is 3h. After the leaching is over, filter and separate to obtain the leaching solution and leaching residue; the leaching residue is 97.20g after drying. After analysis, the yield of the leaching residue is 19.44%, of which Fe24.99%, Ni0.47% , Cu0.054%, S68.21%, the calculation shows that the leaching rate of nickel and copper is greater than 98%, the leaching rate of iron is 25.94%, and the leaching rate of sulfur is 44.43%. The leaching solution is 4L in total, in which nickel ion concentration is 17.56g / ...
Embodiment 2
[0018] The electroplating sludge composition is the same as in Example 1.
[0019] Add 500g of electroplating sludge and 1250g of sulfuric acid solution with a concentration of 250g / L into the reaction kettle, add 1.5g of lignosulfonate, feed industrial oxygen, keep the oxygen partial pressure in the kettle at 0.3MPa, leaching temperature at 150°C, and control the pH of the leaching solution In 1.4, the leaching time is 1h. After the leaching is over, filter and separate to obtain the leaching solution and leaching residue; the leaching residue is 157.85g after drying. After analysis, the yield of the leaching residue is 31.57%, of which Fe13.52%, Ni0.53% , Cu0.048%, S56.99%, the calculation shows that the leaching rate of nickel and copper is greater than 98%, the leaching rate of iron is 18.08%, and the leaching rate of sulfur is 24.59%. The leaching solution is 3L in total, in which nickel ion concentration is 23.29g / L and copper ion concentration is 1.64g / L.
Embodiment 3
[0021] The electroplating sludge composition is the same as in Example 1.
[0022] Add 500g of electroplating sludge and 1,500g of sulfuric acid solution with a concentration of 220g / L into the reaction kettle, add 1.2g of lignosulfonate, and introduce industrial oxygen to keep the oxygen partial pressure in the kettle at 0.4MPa, the leaching temperature is 110°C, and the pH of the leaching solution is controlled At 1.0, the leaching time was 5 hours. After the leaching was completed, the leachate and leaching residue were obtained by filtration and separation; the leaching residue was 134.40 g after drying. After analysis, the yield of leaching slag is 26.88%, of which Fe17.09%, Ni0.42%, Cu0.044%, S61.03%, the calculation shows that the leaching rate of nickel and copper is 98%, and the leaching rate of iron is 11.83% , The sulfur leaching rate is 31.25%. The leaching solution is 3L in total, with nickel ion concentration of 23.37g / L and copper ion concentration of 1.65g / L. ...
PUM
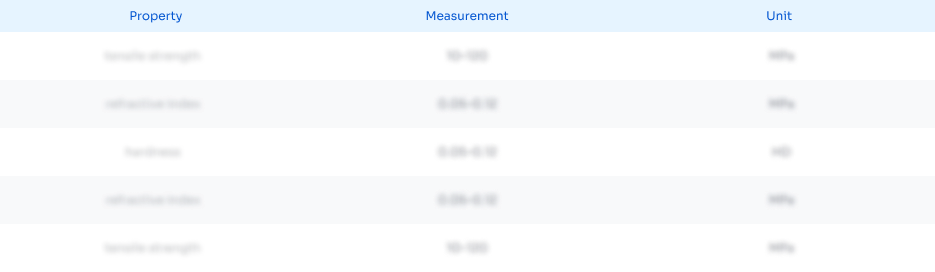
Abstract
Description
Claims
Application Information

- Generate Ideas
- Intellectual Property
- Life Sciences
- Materials
- Tech Scout
- Unparalleled Data Quality
- Higher Quality Content
- 60% Fewer Hallucinations
Browse by: Latest US Patents, China's latest patents, Technical Efficacy Thesaurus, Application Domain, Technology Topic, Popular Technical Reports.
© 2025 PatSnap. All rights reserved.Legal|Privacy policy|Modern Slavery Act Transparency Statement|Sitemap|About US| Contact US: help@patsnap.com