Coal burning boiler polymer dry-process denitrifying agent, preparation method thereof and denitrifying process
A coal-fired boiler and denitrification agent technology, which is applied in the field of boiler flue gas denitrification, can solve the problems of limited denitrification efficiency, high investment cost, and low denitrification efficiency, and achieve complete denitrification, high denitrification efficiency, and low ammonia escape rate.
- Summary
- Abstract
- Description
- Claims
- Application Information
AI Technical Summary
Problems solved by technology
Method used
Image
Examples
Embodiment 1
[0026] 1. Denitration agent and its preparation method:
[0027] The polymer dry denitrification agent for coal-fired boilers consists of the following raw materials in parts by weight:
[0028] 30 parts of urea; 20 parts of silica powder; 30 parts of sodium carbonate; 20 parts of bentonite; 10 parts of sodium sulfate; 30 parts of shale powder.
[0029] refer to figure 1 , the preparation method is as follows: Weigh the full amount of raw materials (A, B...F) according to the ratio of raw materials, crush and grind each raw material to 50-60 meshes, and then enter the mixer to fully stir and mix until the materials are uniform , and then to the specified time, and then packaging inventory Serve as the final product.
[0030] In order to improve the uniformity and consistency of the material, the mixed material can go through multiple grinding, mixing and grinding processes.
[0031] 2. Denitrification system and denitrification process
[0032] refer to figure 2 , the de...
Embodiment 2
[0042] The polymer dry denitrification agent for coal-fired boilers consists of the following raw materials in parts by weight:
[0043] 35 parts of urea; 25 parts of silicon dioxide powder; 20 parts of sodium carbonate; 25 parts of bentonite; 12 parts of sodium sulfate; 25 parts of shale powder.
[0044] The denitrification system and denitrification process are the same as in Example 1, and will not be described in detail.
Embodiment 3
[0046] The polymer dry denitrification agent for coal-fired boilers consists of the following raw materials in parts by weight:
[0047] 40 parts of urea; 30 parts of silica powder; 20 parts of sodium carbonate; 30 parts of bentonite; 15 parts of sodium sulfate; 30 parts of shale powder.
[0048] The denitrification system and denitrification process are the same as in Example 1, and will not be described in detail.
[0049] When adopting the denitrification agent prepared in embodiment 1, embodiment 2, embodiment 3 to operate in conjunction with the denitrification system, with other denitrification energy-saving technologies and products [such as selective non-catalytic reduction (SNCR), selective catalytic reduction (SCR), Electron beam combined desulfurization and denitration method, activated carbon combined desulfurization and denitrification method, ozone oxidation absorption method, etc.] have the following advantages: 1. High denitrification efficiency, up to 95%; 2. ...
PUM
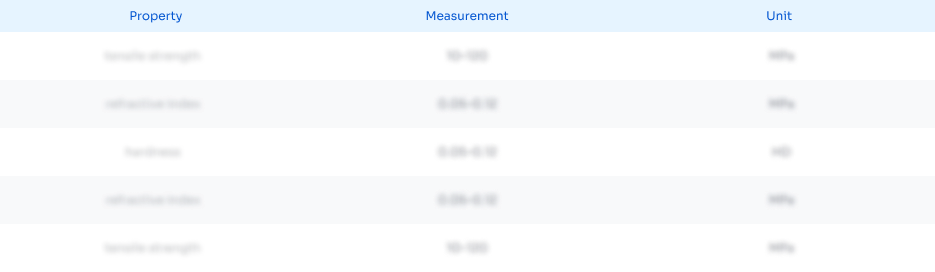
Abstract
Description
Claims
Application Information

- R&D
- Intellectual Property
- Life Sciences
- Materials
- Tech Scout
- Unparalleled Data Quality
- Higher Quality Content
- 60% Fewer Hallucinations
Browse by: Latest US Patents, China's latest patents, Technical Efficacy Thesaurus, Application Domain, Technology Topic, Popular Technical Reports.
© 2025 PatSnap. All rights reserved.Legal|Privacy policy|Modern Slavery Act Transparency Statement|Sitemap|About US| Contact US: help@patsnap.com