Inner groove screw and plunger coaxial injection molding machine
An injection molding machine and internal screw groove technology, which is applied in the field of material molding equipment, can solve the problems of drag, homogenization, and mixing that are not particularly strong, increase the complexity and difficulty of the overall system, increase the volume of the machine and the number of parts, etc. problems, to achieve the effect of increased shearing action, small axial temperature difference, and low production cost
- Summary
- Abstract
- Description
- Claims
- Application Information
AI Technical Summary
Problems solved by technology
Method used
Image
Examples
Embodiment 1
[0034] Such as Figure 1 to Figure 4 As shown, it is a coaxial injection molding machine with inner screw groove and plunger, including barrel 1, plunger 2, plasticizing screw 3, hopper 4, seat 5, radial thrust bearing group 6, transmission Mechanism 7, motor 8, injection seat frame 9, injection cylinder 10, gear 11, mobile cylinder 12 and electric heating coil 13;
[0035]The barrel 1 is divided into a plasticizing zone 101 and an injection zone 102. The diameter of the plasticizing zone 101 is larger than that of the injection zone 102. The injection zone 102 of the barrel 1 is a stepped hole type. The left section of the injection zone 102 (near the plasticizing zone) Area 101) has a large aperture, and the right section of the injection area 102 (near the injection head) has a small aperture, and a material inlet is provided at the left end of the barrel 1; the hopper 4 is installed on the barrel 1, and the outlet of the hopper 4 It communicates with the material feed por...
Embodiment 2
[0041] It is a coaxial injection molding machine with an internal screw groove and a plunger. Its working principle is basically the same as that of Embodiment 1, and its structural diagram is also the same as that of Embodiment 1. figure 1 Similar, the difference is that the injection section 102 of the barrel 1 is a through-hole type, and the structural diagram of the barrel 1 is as follows Figure 5 There is a gap between the outer circle of the plunger 2 and the inner hole of the injection section 102 of the barrel 1 to allow the melt to pass through, and the plunger 2 has been plasticized at any axial position of the injection section 102 of the barrel 1 The molten material can enter the front injection nozzle through the gap under the applied pressure.
Embodiment 3
[0043] Such as Figure 6 to Figure 10 As shown, it is a coaxial injection molding machine with an inner screw groove and a plunger, its structure and working principle are basically the same as those in Embodiment 1, the difference is the diameters of the plasticizing zone 101 and the injection zone 102 Similarly, a one-way valve 15 is installed on the right end of the plunger 2 to prevent backflow of the injection, and the one-way valve 15 is located in the injection area 102 and can move axially.
[0044] When working, the plasticizing screw 3 rotates, and the material in the hopper 4 enters the inner screw groove 302 of the plasticizing screw 3 through the material inlet of the barrel 1 and the radial channel 301 of the plasticizing screw 3, and the material is plasticized The inner screw groove 302 of the screw 3 pushes and moves forward, and then the molten material directly fills the right end of the injection area 102 of the barrel 1 through the one-way valve 15, and th...
PUM
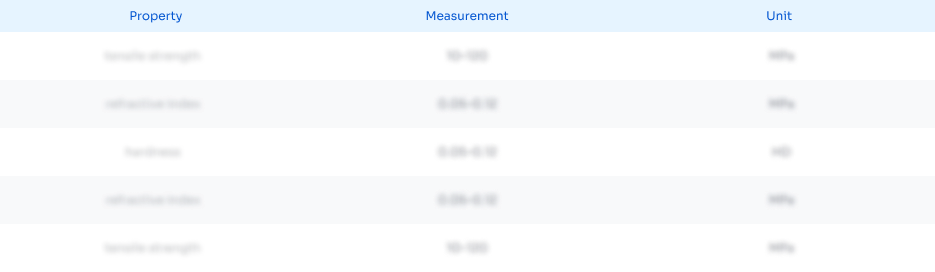
Abstract
Description
Claims
Application Information

- R&D
- Intellectual Property
- Life Sciences
- Materials
- Tech Scout
- Unparalleled Data Quality
- Higher Quality Content
- 60% Fewer Hallucinations
Browse by: Latest US Patents, China's latest patents, Technical Efficacy Thesaurus, Application Domain, Technology Topic, Popular Technical Reports.
© 2025 PatSnap. All rights reserved.Legal|Privacy policy|Modern Slavery Act Transparency Statement|Sitemap|About US| Contact US: help@patsnap.com