Nickel-based corrosion-resistant alloy and preparation method
A corrosion-resistant alloy and nickel-based technology, applied in the field of nickel-based corrosion-resistant alloys, can solve problems such as manpower and material resources consumption, achieve the effects of reducing production process costs, shortening desensitization heat treatment time, and improving depletion conditions
- Summary
- Abstract
- Description
- Claims
- Application Information
AI Technical Summary
Problems solved by technology
Method used
Image
Examples
Embodiment 1
[0033] Vacuum induction plus electroslag remelting smelting process was used to smelt one furnace of the alloy of the present invention (1# alloy) and one furnace of traditional 690 alloy (0# alloy, for comparison), and the chemical composition weight % was as follows.
[0034] 1#: C0.016, Cr30.34, Fe9.70, V0.51, Nb0, Ti0.26, Al0.34, Si0.24, Mn0.20, the rest are Ni and unavoidable impurities.
[0035] 0#: C0.023, Cr30.34, Fe9.67, V0, Nb0, Ti0.26, Al0.31, Si0.26, Mn0.24, the rest are Ni and unavoidable impurities.
[0036] After the 0# alloy is forged and rolled into plates, it is subjected to solution heat treatment (1090°C×1min / mm) and desensitization heat treatment (715°C×15h).
[0037] After the 1# alloy is forged and rolled into a plate, it is subjected to a solution heat treatment (1090°C×1min / mm), then an intermediate heat treatment of 900°C×2h, and then a desensitization heat treatment (715°C×2h).
[0038] The two alloy samples were tested for intergranular corrosion r...
Embodiment 2
[0045] Vacuum induction plus electroslag remelting smelting process was used to smelt one furnace of the alloy of the present invention (2# alloy), and still compared with the traditional 690 alloy of 0#. The weight % of chemical composition of 2# alloy is as follows.
[0046] 2#: C0.020, Cr29.82, Fe9.87, V0.86, Nb0.024, Ti0.01, Al0.25, Si0.23, Mn0.24, the rest are Ni and unavoidable impurities.
[0047] After the 2# alloy is forged and rolled into a plate, it is subjected to solution heat treatment (1090°C×1min / mm), then to 900°C×2h for intermediate heat treatment, and then to desensitization heat treatment (715°C×2h).
[0048] The same test method as in Example 1 was used to test the resistance to intergranular corrosion and pitting corrosion of the two alloys, and the results are also shown in Table 1. It can be seen that the alloy 2# alloy of the present invention (the V content is increased to 0.86%, containing a small amount of Nb,
[0049] The comprehensive corrosion ...
Embodiment 3
[0051] Vacuum induction plus electroslag remelting smelting process was used to smelt one furnace of the alloy (3# alloy) of the present invention, and still compared with the traditional 690 alloy of 0#. The weight % of chemical composition of 3# alloy is as follows.
[0052] 3#: C0.020, Cr29.95, Fe9.70, V0.05, Nb1.06, Ti0.005, Al0.25, Si0.23, Mn0.19, the rest are Ni and unavoidable impurities.
[0053] After the 3# alloy is forged and rolled into a plate, it is subjected to solution heat treatment (1090°C×1min / mm), then to 900°C×2h for intermediate heat treatment, and then to desensitization heat treatment (715°C×2h).
[0054] The same test method as in Example 1 was used to test the resistance to intergranular corrosion and pitting corrosion of the two alloys, and the results are also shown in Table 1. It can be seen that the overall corrosion resistance of the alloy 3# alloy (Nb content increased to 0.86%, containing a small amount of V, (V+Nb) / C=56) of the present invent...
PUM
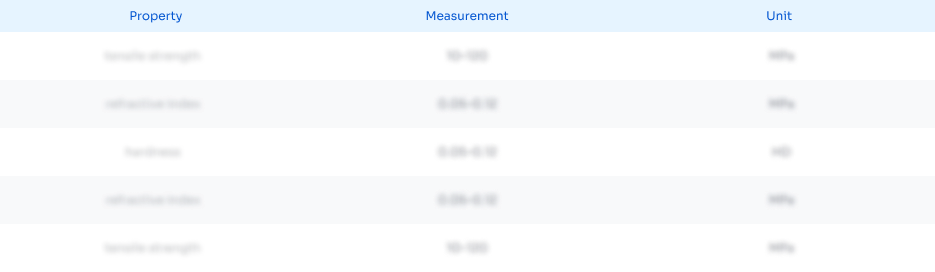
Abstract
Description
Claims
Application Information

- R&D
- Intellectual Property
- Life Sciences
- Materials
- Tech Scout
- Unparalleled Data Quality
- Higher Quality Content
- 60% Fewer Hallucinations
Browse by: Latest US Patents, China's latest patents, Technical Efficacy Thesaurus, Application Domain, Technology Topic, Popular Technical Reports.
© 2025 PatSnap. All rights reserved.Legal|Privacy policy|Modern Slavery Act Transparency Statement|Sitemap|About US| Contact US: help@patsnap.com