Preheat treatment method for large-size forged steel supporting roller
A technology of preparatory heat treatment and post-forging heat treatment, applied in heat treatment furnaces, heat treatment equipment, furnace types, etc., can solve the problems of increasing the risk of backup roll breakage, difficulty in formulating heat treatment processes, and large dissolving temperature differences, and shortening the holding time. , The effect of eliminating segregation, adjusting the organization, and high degree of spheroidization
- Summary
- Abstract
- Description
- Claims
- Application Information
AI Technical Summary
Problems solved by technology
Method used
Image
Examples
Embodiment 1
[0029] Example 1 of the present invention backup roll material 45Cr4NiMoV, its chemical composition and ingredients in weight percent (%), is: C: 0.4-0.5; Si: 0.4-1.0; Mn: 0.4-1.0; Cr: 3.5-4.5 ; Mo: 0.4-0.8; Ni: 0.4-0.8; V: 0.05-0.25; the rest are Fe and other impurities. The size of the backup roll is Φ1410mm (roller body diameter)×2815mm (roller body length)×5660mm (total length).
[0030] 1. Post-forging heat treatment process: normalizing temperature is 880-920°C, heating rate is less than 90°C / h, holding time after uniform temperature is 10-25 hours, high temperature tempering after air cooling, tempering temperature is 500 -700°C, the heating rate is less than 60°C / h, and the holding time after uniform temperature is 50-90 hours.
[0031] 2. Quenching and tempering treatment method: the preheating temperature of the backup roll is 550-700°C, the holding time is 5-20 hours, and then heated to the quenching temperature of 880±20°C, the heating rate is less than 80°C / h, an...
Embodiment 2
[0035] Example 2 of the present invention backup roll material 50Cr5NiMoV, its chemical composition and ingredients in weight percent (%), including: C: 0.4-0.6; Si: 0.4-1.0; Mn: 0.4-1.0; Cr: 4.5-5.5 ; Mo: 0.4-0.8; Ni: 0.4-0.8; V: 0.05-0.3; the rest are Fe and other impurities. The size of the backup roll is Φ1340mm (roller body diameter)×1380mm (roller body length)×4870mm (total length).
[0036] The following process is used for heat treatment of the steel of the embodiment: after forging, the billet is firstly subjected to post-forging heat treatment, the normalizing temperature is 900-940°C, the heating rate is less than 90°C / h, and the holding time after equalization is 10-25 hours. After air cooling, carry out high-temperature tempering, the tempering temperature is 550-700°C, the heating rate is less than 60°C / h, and the holding time after uniform temperature is 50-90 hours.
[0037] Then carry out quenching and tempering treatment, the preheating temperature is 580-70...
PUM
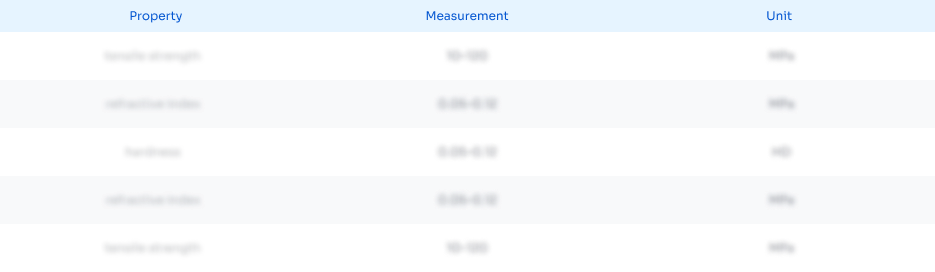
Abstract
Description
Claims
Application Information

- Generate Ideas
- Intellectual Property
- Life Sciences
- Materials
- Tech Scout
- Unparalleled Data Quality
- Higher Quality Content
- 60% Fewer Hallucinations
Browse by: Latest US Patents, China's latest patents, Technical Efficacy Thesaurus, Application Domain, Technology Topic, Popular Technical Reports.
© 2025 PatSnap. All rights reserved.Legal|Privacy policy|Modern Slavery Act Transparency Statement|Sitemap|About US| Contact US: help@patsnap.com