Powder paint for aluminum section and preparation method thereof
A technology for powder coatings and aluminum profiles, applied in powder coatings, polyester coatings, coatings, etc., can solve the problems of easy generation of orange peel, easy powder removal, weak adhesion, etc., and achieve easy powder removal and good adhesion Strong, simple preparation method
- Summary
- Abstract
- Description
- Claims
- Application Information
AI Technical Summary
Problems solved by technology
Method used
Examples
Embodiment 1
[0016] A powder coating for aluminum profiles, comprising the following raw materials in parts by weight: 66 parts by weight of carboxyl-terminated polyester resin, 10 parts by weight of titanium dioxide, 5 parts by weight of superfine sericite, 12 parts by weight of precipitated barium sulfate, 10 parts by weight of ethanol, 4 parts by weight of triglycidyl isocyanurate, 10 parts by weight of silane coupling agent, 2 parts by weight of expanded perlite, 10 parts by weight of potassium carbonate, and 15 parts by weight of ammonium dihydrogen phosphate.
[0017] The preparation method thereof comprises the following processing steps: (1) 66 parts by weight of carboxyl-terminated polyester resin, 10 parts by weight of titanium dioxide, 12 parts by weight of precipitated barium sulfate, 10 parts by weight of ethanol, 4 parts by weight of triglycidyl isocyanurate, Put 2 parts by weight of expanded perlite into a mixer and mix and stir for 10 minutes, then heat to 16°C; (2) Then add...
Embodiment 2
[0019] A powder coating for aluminum profiles, comprising the following raw materials in parts by weight: 66-70 parts by weight of carboxyl-terminated polyester resin, 15 parts by weight of titanium dioxide, 10 parts by weight of superfine sericite, 18 parts by weight of precipitated barium sulfate, and 18 parts by weight of ethanol parts, 5 parts by weight of triglycidyl isocyanurate, 15 parts by weight of silane coupling agent, 8 parts by weight of expanded perlite, 15 parts by weight of potassium carbonate, and 20 parts by weight of ammonium dihydrogen phosphate.
[0020] Its preparation method includes the following processing steps: (1) 70 parts by weight of carboxyl-terminated polyester resin, 15 parts by weight of titanium dioxide, 18 parts by weight of precipitated barium sulfate, 18 parts by weight of ethanol, 5 parts by weight of triglycidyl isocyanurate, Put 8 parts by weight of expanded perlite into a mixer and mix for 15 minutes, then heat to 25°C; (2) Then add 10 ...
Embodiment 3
[0022] A powder coating for aluminum profiles, comprising the following raw materials in parts by weight: 69 parts by weight of carboxyl-terminated polyester resin, 14 parts by weight of titanium dioxide, 8 parts by weight of superfine sericite, 16 parts by weight of precipitated barium sulfate, 17 parts by weight of ethanol, 4 parts by weight of triglycidyl isocyanurate, 14 parts by weight of silane coupling agent, 6 parts by weight of expanded perlite, 12 parts by weight of potassium carbonate, and 17 parts by weight of ammonium dihydrogen phosphate.
[0023] Its preparation method includes the following processing steps: (1) 69 parts by weight of carboxyl-terminated polyester resin, 14 parts by weight of titanium dioxide, 16 parts by weight of precipitated barium sulfate, 17 parts by weight of ethanol, 4 parts by weight of triglycidyl isocyanurate, swelling Put 6 parts by weight of perlite into a blender and mix for 12 minutes, heat to 16-25°C; (2) Then add 8 parts by weight...
PUM
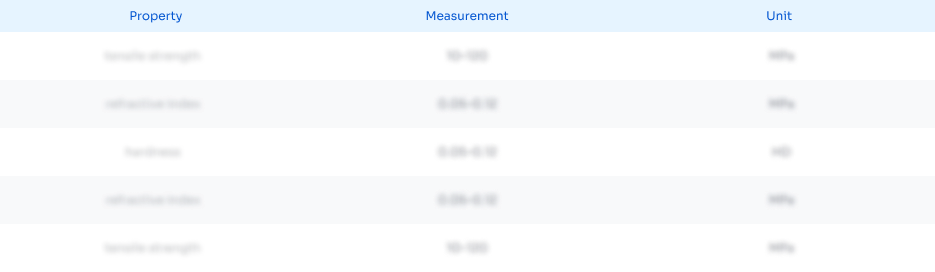
Abstract
Description
Claims
Application Information

- R&D Engineer
- R&D Manager
- IP Professional
- Industry Leading Data Capabilities
- Powerful AI technology
- Patent DNA Extraction
Browse by: Latest US Patents, China's latest patents, Technical Efficacy Thesaurus, Application Domain, Technology Topic, Popular Technical Reports.
© 2024 PatSnap. All rights reserved.Legal|Privacy policy|Modern Slavery Act Transparency Statement|Sitemap|About US| Contact US: help@patsnap.com