Honeycomb vanadium series denitration preformed catalyst, and preparation method and use thereof
A catalyst, honeycomb-shaped technology, applied in the field of environmental catalysis and environmental protection, can solve the problems of water resistance, sulfur resistance, poor corrosion resistance, and high vanadium loading of the unexamined catalyst, and achieve excellent resistance to SO2 and water vapor poisoning performance, The effect of excellent denitration efficiency and excellent mechanical properties
- Summary
- Abstract
- Description
- Claims
- Application Information
AI Technical Summary
Problems solved by technology
Method used
Image
Examples
Embodiment 1
[0053] Configuration 5wt% oxalic acid solution, then add ammonium metavanadate, active component V 2 o 5 The content accounts for 0.1% of the mass percentage of the catalyst powder, stir and dissolve at a temperature of 55°C until the solution turns dark blue, then add ammonium metatungstate, WO 3 The content accounts for 10% of the mass percentage of the catalyst powder and is stirred until dissolved. Then add this solution into the titanium dioxide powder and stir evenly to obtain a slurry. Dry at 110° C. for 12 hours, grind, calcinate at 500° C. for 5 hours, and grind to obtain catalyst powder.
[0054] Weigh the catalyst powder, then add solid forming aids glass fiber, activated carbon, and methyl cellulose for stirring and dry mixing, wherein the content of glass fiber is 10%, the content of activated carbon is 10%, and the content of methyl cellulose is 1%. After uniformity, add liquid forming additives silica sol and glycerin for wet mixing, wherein the content of si...
Embodiment 2
[0057] Configuration 5wt% oxalic acid solution, then add ammonium metavanadate, active component V 2 o 5 The content accounts for 3% of the mass percentage of the catalyst powder, stir and dissolve at a temperature of 55°C until the solution turns dark blue, then add ammonium metatungstate, WO 3 The content accounts for 1% of the mass percentage of the catalyst powder, and it is stirred until dissolved. Then add this solution into the titanium dioxide powder and stir evenly to obtain a slurry. Dry at 110° C. for 12 hours, grind, calcinate at 500° C. for 5 hours, and grind to obtain catalyst powder.
[0058] Weigh the catalyst powder, then add solid forming aids glass fiber, safflower powder, and polyvinyl alcohol for stirring and dry mixing, wherein the content of glass fiber is 10%, the content of squat powder is 5%, and the content of polyvinyl alcohol is 1%. After mixing evenly, add liquid forming additives silica sol and glycerin for wet mixing, wherein the content of s...
Embodiment 3
[0061] Configuration 5wt% oxalic acid solution, then add ammonium metavanadate, active component V 2 o 5 The content accounts for 1.5% of the mass percentage of the catalyst powder. Stir and dissolve at a temperature of 55°C until the solution turns dark blue, then add ammonium metatungstate, WO 3 The content accounts for 10% of the mass percentage of the catalyst powder and is stirred until dissolved. Then add this solution into the titanium dioxide powder and stir evenly to obtain a slurry. Dry at 110° C. for 12 hours, grind, calcinate at 500° C. for 5 hours, and grind to obtain catalyst powder.
[0062] Weigh the catalyst powder, then add solid forming aids glass fiber, water glass, activated carbon, hydroxypropyl methylcellulose, and turnip powder for stirring and dry mixing, wherein the content of glass fiber is 10%, and the content of activated carbon is 5%. The content of safflower powder is 5%, the content of hydroxypropyl methylcellulose is 5%, and after mixing eve...
PUM
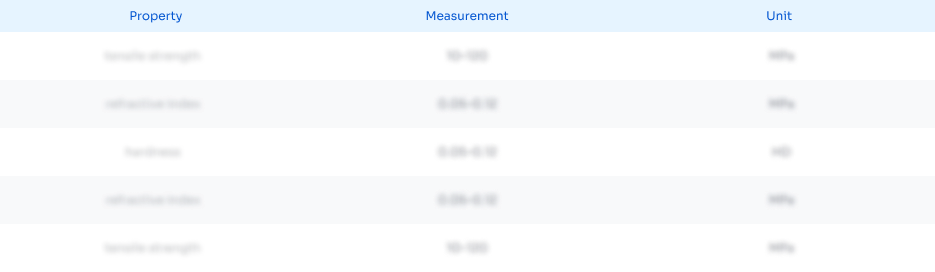
Abstract
Description
Claims
Application Information

- Generate Ideas
- Intellectual Property
- Life Sciences
- Materials
- Tech Scout
- Unparalleled Data Quality
- Higher Quality Content
- 60% Fewer Hallucinations
Browse by: Latest US Patents, China's latest patents, Technical Efficacy Thesaurus, Application Domain, Technology Topic, Popular Technical Reports.
© 2025 PatSnap. All rights reserved.Legal|Privacy policy|Modern Slavery Act Transparency Statement|Sitemap|About US| Contact US: help@patsnap.com