Production method of multi-element transition metal hydroxide nuclear shell composite carbon filter electrode material
A composite carbon fiber and hydroxide technology, which is applied in the manufacture of hybrid capacitor electrodes and hybrid/electric double layer capacitors, etc., can solve the problems of electrochemical efficiency limitation, capacitance degradation, poor quality, large volume change, etc., and achieve easy implementation and energy saving. Excellent electrochemical performance and good electrical conductivity
- Summary
- Abstract
- Description
- Claims
- Application Information
AI Technical Summary
Problems solved by technology
Method used
Image
Examples
Embodiment 1
[0020] 1) Preparation of polymer nanofibers: Dissolve PAN in DMF and prepare a 10wt% polymer solution. After it is completely dissolved, inject it into the spinning needle tube to set the spinning voltage at 20KV, and spin at a receiving distance of 15cm to obtain The nanofibers were dried in a vacuum oven for 24 hours;
[0021] 2) Preparation of surface-functionalized carbon nanofibers: the obtained polymer fibers were placed in a vacuum tube furnace, pre-oxidized in an air atmosphere at 280°C for 2 hours, and then heated to 1000°C in a nitrogen atmosphere for high-temperature carbonization for 1 hour, and the obtained carbon nanofibers The fiber was treated with a mixed solution of sulfuric acid and nitric acid (molar ratio 1:1) for 30 minutes;
[0022] 3) In-situ catalytic growth of multi-element metal hydroxides: Cut the carbon nanofibers obtained in the above steps to 2cm*2cm and soak them in 20ml of absolute ethanol solution, add 2g of zinc nitrate / The cobalt nitrate m...
Embodiment 2
[0024] 1) Preparation of polymer nanofibers: Dissolve PAN in DMF and prepare a 15wt% polymer solution. After it is completely dissolved, inject it into the spinning needle tube to set the spinning voltage at 15KV, and spin at a receiving distance of 15cm to obtain The nanofibers were dried in a vacuum oven for 24 hours;
[0025] 2) Preparation of surface-functionalized carbon nanofibers: the obtained polymer fibers were placed in a vacuum tube furnace, pre-oxidized in an air atmosphere at 280°C for 2 hours, and then heated to 1000°C in a nitrogen atmosphere for high-temperature carbonization for 1 hour, and the obtained carbon nanofibers The fiber was treated with a mixed solution of sulfuric acid and nitric acid (molar ratio 1:1) for 30 minutes;
[0026] 3) In-situ catalytic growth of multi-element metal hydroxides: Cut the carbon nanofibers obtained in the above steps into 2cm*2cm and soak them in 20ml of absolute ethanol solution, add 2g of zinc nitrate / The cobalt nitrate...
Embodiment 3
[0028] 1) Preparation of polymer nanofibers: Dissolve PAN in DMF and prepare a 15wt% polymer solution. After it is completely dissolved, inject it into the spinning needle tube to set the spinning voltage at 20KV, and spin at a receiving distance of 20cm. The obtained The nanofibers were dried in a vacuum oven for 24 hours;
[0029] 2) Preparation of surface-functionalized carbon nanofibers: the obtained polymer fibers were placed in a vacuum tube furnace, pre-oxidized in an air atmosphere at 280°C for 2 hours, and then heated to 1000°C in a nitrogen atmosphere for high-temperature carbonization for 1 hour, and the obtained carbon nanofibers The fiber was treated with a mixed solution of sulfuric acid and nitric acid (molar ratio 1:1) for 30 minutes;
[0030] 3) In-situ catalytic growth of multi-element metal hydroxides: Cut the carbon nanofibers obtained in the above steps to 2cm*2cm and soak them in 20ml of absolute ethanol solution, add 2g of zinc nitrate / The cobalt nitra...
PUM
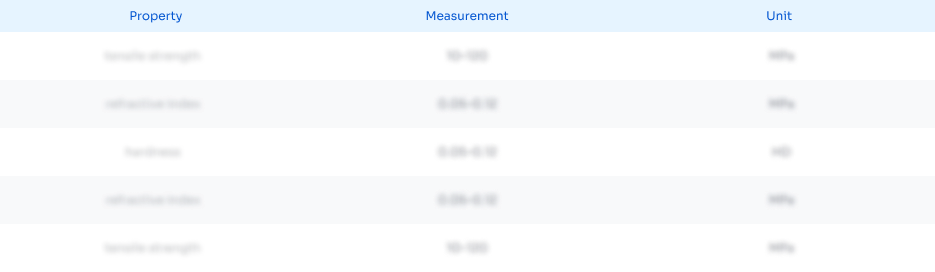
Abstract
Description
Claims
Application Information

- Generate Ideas
- Intellectual Property
- Life Sciences
- Materials
- Tech Scout
- Unparalleled Data Quality
- Higher Quality Content
- 60% Fewer Hallucinations
Browse by: Latest US Patents, China's latest patents, Technical Efficacy Thesaurus, Application Domain, Technology Topic, Popular Technical Reports.
© 2025 PatSnap. All rights reserved.Legal|Privacy policy|Modern Slavery Act Transparency Statement|Sitemap|About US| Contact US: help@patsnap.com