A production process and special device for non-woven filter material without base cloth
A special device and production process technology, applied in the direction of filtration and separation, membrane filter, non-woven fabrics, etc., can solve the problem of easy deformation of pre-needle felt without base fabric, and achieve simple production process, short production time and high production efficiency. time-controlled effects
- Summary
- Abstract
- Description
- Claims
- Application Information
AI Technical Summary
Problems solved by technology
Method used
Image
Examples
Embodiment 1
[0037] Example 1: A special device for opening fibers of pre-needled felt
[0038] combine figure 1 , figure 2 As shown, the present invention is a special device for opening fibers of pre-needled felt, comprising a cylinder body 1, the bottom of the cylinder body 1 is connected with a vacuum pump 5, a side door 2 and a feed port 8 are arranged on the cylinder body 1, and the cloth The cage 3 is installed in the cylinder body 1, the cloth cage 3 includes a chassis 32, and the small motor 7 is linked with the chassis 32. A number of small holes 311 are provided, and the cloth clamp 312 is installed on the center pipe 31 of the cloth cage. One end of the centrifugal pump 4 is connected with the central pipe 31 of the cloth cage, and the other end of the centrifugal pump 4 is connected with the driving motor 6 .
[0039] As a preferred embodiment, the cylinder body 1 is provided with a side door 2 on the side wall of the cylinder body 1 to facilitate the operation of feeding a...
Embodiment 2
[0046] Embodiment 2: a kind of production technology of base cloth nonwoven filter material
[0047] A kind of production technology of base cloth nonwoven filter material, it is characterized in that, comprises the following steps:
[0048] (1) Laying: Lay the net after evenly mixing the composite fiber and ordinary PPS fiber in proportion.
[0049] The composition ratio of the composite fiber and the mixing ratio of the composite fiber and common PPS fiber laying were changed, as shown in Example 2-1 to Example 2-6 of Table 1.
[0050] Table 1: Selection and ratio of different composite fibers
[0051]
[0052] Note: The composite fiber in Example 2-1~Example 2-3 is the sea-island type PPS / PET composite fiber; Example 2-4~
[0053] The composite fiber in embodiment 2-6 is split type PPS / PET composite fiber;
[0054] (2) Pre-acupuncture: Pre-needle the fibers laid out in step (1) into pre-needle felt without base fabric, and the needle density is: 100 needles / ㎝ 2 ;
...
Embodiment 3-1~ Embodiment 3-4
[0074] Technology is the same as embodiment 2, and difference is: change the process parameter of step (3) fiber opening, and statistics, analyze its performance impact on non-woven filter material without base cloth, specifically as follows:
[0075] (1) Laying net:
[0076] Evenly mix 70 / 30 island-in-the-sea composite fiber PPS / PET and ordinary PPS fiber in the ratio of 80 / 20, then lay the net, and lay it into a certain thickness according to actual needs;
[0077] (2) Pre-acupuncture: acupuncture density: 150 needles / ㎝ 2 .
[0078] (3) Fiber opening:
[0079] Open the side door 2 of the special device for fiber opening of the pre-needled felt, clamp the head of the non-base cloth pre-needled felt on the cloth cage central tube 31, and use the small motor 7 to make the cloth cage central tube 31 rotate at a certain speed, and evenly The non-base cloth pre-needle felt is wound onto the cloth cage central tube 31;
[0080] After closing the side door 2, add some caustic so...
PUM
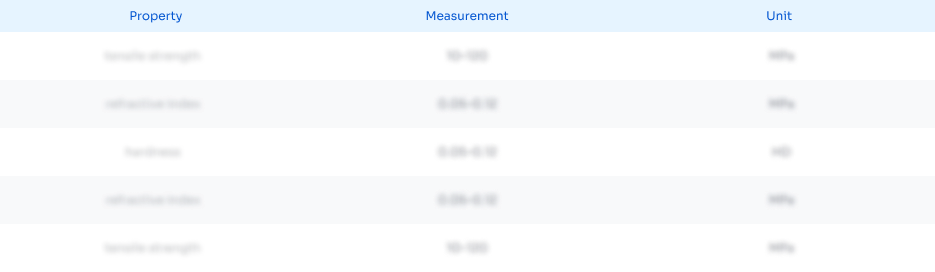
Abstract
Description
Claims
Application Information

- R&D
- Intellectual Property
- Life Sciences
- Materials
- Tech Scout
- Unparalleled Data Quality
- Higher Quality Content
- 60% Fewer Hallucinations
Browse by: Latest US Patents, China's latest patents, Technical Efficacy Thesaurus, Application Domain, Technology Topic, Popular Technical Reports.
© 2025 PatSnap. All rights reserved.Legal|Privacy policy|Modern Slavery Act Transparency Statement|Sitemap|About US| Contact US: help@patsnap.com