Preparation method of carbon-containing residual oil hydrodemetallization catalyst
A hydrodemetallization and catalyst technology, applied in the direction of metal/metal oxide/metal hydroxide catalysts, chemical instruments and methods, physical/chemical process catalysts, etc., can solve the problems of unsatisfactory mechanical strength of catalysts, and prevent The effect of reunion
- Summary
- Abstract
- Description
- Claims
- Application Information
AI Technical Summary
Problems solved by technology
Method used
Image
Examples
Embodiment 1
[0035] Weigh the pore volume as 0.9ml / g and the specific surface area as 220m 2 100 grams of gamma-phase cylindrical strip-shaped alumina carrier / g is put into the spray rolling pot, and in the rotating state, spray and impregnate 25 ml of xylitol aqueous solution with a mass concentration of 40% to the carrier in the rolling pot in the form of atomization ; Then continue to spray and impregnate the alumina carrier with 40ml of xylitol aqueous solution with a mass concentration of 20%; finally continue to spray and impregnate the alumina carrier with 40ml of xylitol aqueous solution with a mass concentration of 10%. After impregnation, the alumina carrier was transferred into an autoclave, and the autoclave was placed in an oven at 180° C. for 9 hours under autogenous pressure for carbonization treatment, and then cooled naturally to room temperature. The alumina carrier after hydrothermal treatment was dried at 120° C. for 3 hours. Dry the carrier with 150ml containing MoO ...
Embodiment 2
[0037] Same as Example 1, except that the alumina carrier is a clover strip, 30ml of sorbitol aqueous solution with a mass concentration of 30% is used for the first spray and impregnation, and 50ml of sorbitol with a mass concentration of 10% is used for the second spray and impregnation. For the aqueous alcohol solution, use 20ml of sorbitol aqueous solution with a mass concentration of 5% for the third spraying and dipping. The temperature during carbonization treatment is 200°C, and the carbonization time is 8 hours. MoO in impregnating solution 3 8g / 100ml (molybdenum source comes from ammonium molybdate), NiO1.2g / 100ml (nickel source comes from nickel chloride). The temperature of the hydrothermal treatment was 160° C., and the treatment time was 8 hours. Ammonia gas sealing treatment condition is that at first the ammonia gas pressure is 5MPa and seals for 1 hour, then vents part of the ammonia gas, controls the pressure of ammonia gas to be 0.5MPa, and seals for 10 hou...
Embodiment 3
[0039] With embodiment 1, just adopt four times of spray impregnation, use 20ml mass concentration to be the aqueous solution of mannitol of 50% during the first spray impregnation, use 40ml mass concentration to be 30% sorbitol during the second spray impregnation 20ml of sorbitol aqueous solution with a mass concentration of 20% was used for the third spray and dipping, and 20ml of a sorbitol aqueous solution with a mass concentration of 10% was used for the fourth spray and dip. During the carbonization treatment, the temperature was 240° C., and the carbonization time was 12 hours. MoO in impregnating solution 3 12g / 100ml (molybdenum source comes from ammonium molybdate), NiO1.8g / 100ml (nickel source comes from nickel chloride). The temperature of the hydrothermal treatment is 180° C., and the treatment time is 6 hours. The condition of ammonia gas sealing treatment is to feed ammonia gas and nitrogen gas respectively, the partial pressure of ammonia gas in the tube furn...
PUM
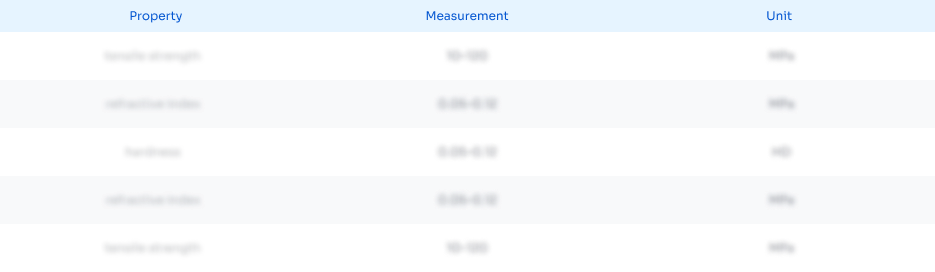
Abstract
Description
Claims
Application Information

- R&D Engineer
- R&D Manager
- IP Professional
- Industry Leading Data Capabilities
- Powerful AI technology
- Patent DNA Extraction
Browse by: Latest US Patents, China's latest patents, Technical Efficacy Thesaurus, Application Domain, Technology Topic, Popular Technical Reports.
© 2024 PatSnap. All rights reserved.Legal|Privacy policy|Modern Slavery Act Transparency Statement|Sitemap|About US| Contact US: help@patsnap.com