Prepositioned SCO intensified flue gas denitration and demercuration system of coal-fired power plant
A technology for coal-fired power plants and flue gas, which is applied in gas treatment, chemical instruments and methods, separation methods, etc., can solve the problems of unsatisfactory Hg0 oxidation efficiency, uneconomical, and reduced oxidation efficiency, and achieves that the technical process is easy to implement. , The effect of reducing the amount of use and improving the oxygen storage performance
- Summary
- Abstract
- Description
- Claims
- Application Information
AI Technical Summary
Problems solved by technology
Method used
Image
Examples
Embodiment 1
[0037] A pre-SCO enhanced denitrification and mercury removal technology test experiment was carried out in a coal-fired power plant with a pulverized coal furnace. The SCR unit is a commercial V-W-Ti catalyst, and the original denitrification efficiency is 85%. The measured mercury concentration at the inlet of the SCO unit is 25.6ug / m 3 , NO content is 0.1%, C (NO) / C (NOX) =0.95, the oxygen content was 4.6%. The SCO catalyst used is 5% by mass of cobalt oxide, 3% by mass of tungsten oxide and 10% by mass of cerium oxide as the catalyst carrier, and the arrangement temperature is 300°C. The pre-installation test was carried out, the SCO catalyst was arranged in double layers, and the actual space velocity was 3500h -1 , the flue gas direct passage rate δ is 0%, and the Hg of the SCO unit is measured by the test 0 The oxidation rate is 96%, and the NO oxidation rate is 47%, meeting the established requirements. After the SCR unit and dust removal unit, the Hg removal eff...
Embodiment 2
[0039] A pre-SCO enhanced denitrification and mercury removal technology test experiment was carried out in a coal-fired power plant with a pulverized coal furnace. The SCR unit is a commercial V-W-Ti catalyst, and the original denitrification efficiency is 83%. The measured mercury concentration at the inlet of the SCO unit is 19.6ug / m 3 , NO content is 0.15%, C (NO) / C (NOX) =0.98, the oxygen content is 5%. The SCO catalyst used is 5% by mass of manganese oxide, 5% by mass of tungsten oxide and 20% by mass of cerium oxide as the catalyst carrier, and the arrangement temperature is 350°C. The pre-installation test is carried out, the SCO catalyst adopts a double-layer arrangement, the direct flue gas passing rate δ is 0%, and the actual space velocity is 3900h -1 , measured in SCO unit Hg 0 The oxidation rate was 97%, and the NO oxidation rate was 36%. Change the SCO catalyst unit to a three-layer arrangement, the SCO unit Hg 0 The oxidation rate is 98%, and the NO oxid...
Embodiment 3
[0041] A pre-SCO enhanced denitrification and mercury removal technology test experiment was carried out in a coal-fired power plant with a pulverized coal furnace. The SCR unit is a commercial V-W-Ti catalyst, and the original denitrification efficiency is 87%. The measured mercury concentration at the inlet of the SCO unit is 22.6ug / m 3 , NO content is 0.15%, C (NO) / C (NOX) =0.92, the oxygen content is 5.5%. The SCO catalyst used is that manganese oxide accounts for 2.5% by mass of the catalyst, cobalt oxide accounts for 2.5% by mass of the catalyst, tungsten oxide accounts for 4% by mass of the catalyst, and cerium oxide accounts for 15% by mass of the catalyst carrier. The arrangement temperature is 325°C. The pre-installation test is carried out, the SCO catalyst adopts a double-layer arrangement, the direct flue gas passing rate δ is 0%, and the actual space velocity is 3100h -1 . Measured SCO unit Hg 0 The oxidation rate was 96%, and the NO oxidation rate was 58%...
PUM
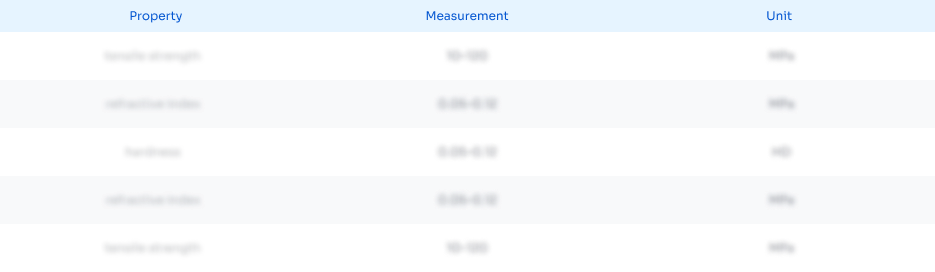
Abstract
Description
Claims
Application Information

- Generate Ideas
- Intellectual Property
- Life Sciences
- Materials
- Tech Scout
- Unparalleled Data Quality
- Higher Quality Content
- 60% Fewer Hallucinations
Browse by: Latest US Patents, China's latest patents, Technical Efficacy Thesaurus, Application Domain, Technology Topic, Popular Technical Reports.
© 2025 PatSnap. All rights reserved.Legal|Privacy policy|Modern Slavery Act Transparency Statement|Sitemap|About US| Contact US: help@patsnap.com