A kind of electric contact material and preparation method thereof
A technology of electric contact material and copper alloy, which is applied in the direction of contacts, circuits, electric switches, etc., can solve the problems of reducing the conductivity of materials, reduce agglomeration, shorten melting time, improve corrosion resistance and welding resistance Effect
- Summary
- Abstract
- Description
- Claims
- Application Information
AI Technical Summary
Problems solved by technology
Method used
Image
Examples
Embodiment 1
[0020] (1) Nickel-coated graphene powder was prepared by depositing metallic nickel on the surface of graphene (1-10 layers) by DC magnetron sputtering. The nickel target with a purity of 99.99% is first polished with fine sandpaper to remove the surface oxide film before installation, then cleaned with acetone and dried. Pre-sputtering is carried out for 5 minutes before DC magnetron sputtering deposition to remove metal oxides and other impurities on the target surface to ensure the purity of the nickel film deposited on the subsequent graphene surface. The sputtering parameters are as follows: the vacuum degree reaches 0.1*10 -3 At Pa, high-purity argon gas was introduced, the vacuum chamber pressure was 0.5 Pa, the sputtering power was 100 W, and the deposition time was 30 min.
[0021] (2) The alloy powder containing 0.15% bismuth, 0.1% zinc and 99.75% copper is made into 200 mesh copper alloy powder by gas atomization method.
[0022] (3) Nickel-plated graphene and cop...
Embodiment 2
[0026] (1) Use DC magnetron sputtering method to deposit metallic nickel on the surface of graphene (1-5 layers) to prepare nickel-coated graphene powder. The nickel target with a purity of 99.99% is ground and removed with fine sandpaper before installation. The oxide film was cleaned with acetone, dried, and pre-sputtered for 5 minutes before DC magnetron sputtering deposition to remove metal oxides and other impurities on the target surface to ensure the purity of the nickel film deposited on the subsequent graphene surface. The sputtering parameters are as follows: when the vacuum reaches 1.0×10-3Pa, high-purity argon gas is introduced, the vacuum chamber pressure is 1.2Pa, the sputtering power is 150W, and the deposition time is 10min.
[0027] (2) The alloy powder containing 0.5% bismuth, 3.0% zinc and 96.5% copper is made into 300 mesh copper alloy powder by gas atomization method.
[0028] (3) Nickel-plated graphene and copper-0.5% bismuth-3.0% zinc alloy powder are lo...
Embodiment 3
[0032] (1) Nickel-coated graphene was prepared by depositing metallic nickel on the surface of graphene (1-10 layers) by DC magnetron sputtering. The target with a purity of 99.99% is ground with fine sandpaper to remove the surface oxide film before installation, then cleaned with acetone and dried. Pre-sputtering is carried out for 5 minutes before DC magnetron sputtering deposition to remove metal oxides and other impurities on the target surface to ensure the purity of the nickel film deposited on the subsequent graphene surface. The sputtering parameters are as follows: the vacuum degree reaches 0.5*10 -3 At Pa, high-purity argon gas was introduced, the vacuum chamber pressure was 1.0 Pa, the sputtering power was 140 W, and the deposition time was 15 min.
[0033] (2) The alloy powder containing 0.2% bismuth, 3.0% aluminum and 96.8% copper is made into 200 mesh copper alloy powder by gas atomization method.
[0034] (3) Put nickel-plated graphene: copper-0.2% bismuth-3....
PUM
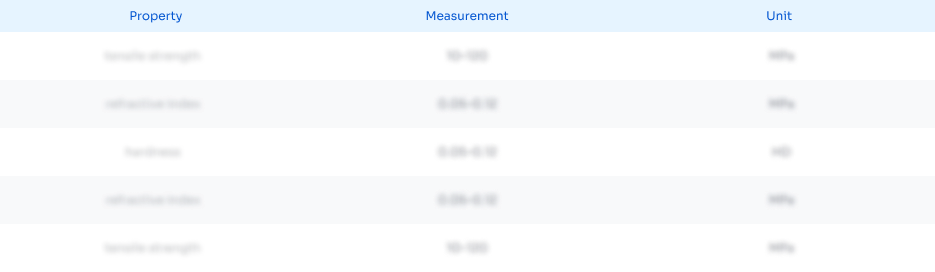
Abstract
Description
Claims
Application Information

- R&D
- Intellectual Property
- Life Sciences
- Materials
- Tech Scout
- Unparalleled Data Quality
- Higher Quality Content
- 60% Fewer Hallucinations
Browse by: Latest US Patents, China's latest patents, Technical Efficacy Thesaurus, Application Domain, Technology Topic, Popular Technical Reports.
© 2025 PatSnap. All rights reserved.Legal|Privacy policy|Modern Slavery Act Transparency Statement|Sitemap|About US| Contact US: help@patsnap.com