Shock-absorption synthetic rubber and preparation method thereof
A technology of synthetic rubber and composite particles, which is applied in the field of rubber materials and its preparation, and shock-absorbing synthetic rubber. It can solve the problems of failure to meet the requirements of sulfur-free environmental protection, corrosion of circuit and electronic components, and failure of normal operation of electrical appliances. The effect of simple process, low production cost and high elasticity
- Summary
- Abstract
- Description
- Claims
- Application Information
AI Technical Summary
Problems solved by technology
Method used
Examples
Embodiment 1
[0018] The invention is a shock-absorbing synthetic rubber, which is made of the following raw materials in parts by weight:
[0019] 10.5 parts of methyl methacrylate, 2.3 parts of silver-coated glass microbead core-shell composite particles, 2.6 parts of rosin polyoxyethylene sulfonate, 1.5 parts of polyethylene glycol octylphenyl ether, 3-ethoxy ethyl propionate 5.3 parts of ester, 4.3 parts of pine tar, 2.5 parts of magnesium oxide, 1.3 parts of coupling agent. The coupling agent is distearyloxy isopropyl aluminate.
[0020] The preparation method of above-mentioned damping synthetic rubber, comprises the following steps:
[0021] (1) Mix methyl methacrylate, silver-coated glass microbead core-shell composite particles and rosin polyoxyethylene sulfonate according to the above formula, and stir for 15 minutes at a stirring speed of 500 rpm;
[0022] (2) Then polyethylene glycol octylphenyl ether and ethyl 3-ethoxypropionate were added, stirred for 20 minutes, and the sti...
Embodiment 2
[0026] The invention is a shock-absorbing synthetic rubber, which is made of the following raw materials in parts by weight:
[0027] 11.6 parts of methyl methacrylate, 3.7 parts of silver-coated glass microbead core-shell composite particles, 3.8 parts of rosin polyoxyethylene sulfonate, 1.6 parts of polyethylene glycol octylphenyl ether, 3-ethoxy ethyl propionate 6.8 parts of ester, 4.8 parts of pine tar, 2.9 parts of magnesium oxide, and 1.6 parts of coupling agent. The coupling agent is distearyloxy isopropyl aluminate.
[0028] The preparation method of above-mentioned damping synthetic rubber, comprises the following steps:
[0029] (1) Mix methyl methacrylate, silver-coated glass microbead core-shell composite particles and rosin polyoxyethylene sulfonate according to the above formula, and stir for 18 minutes at a stirring speed of 550 rpm;
[0030] (2) Then polyethylene glycol octylphenyl ether and ethyl 3-ethoxypropionate were added, stirred for 25 minutes, and the...
Embodiment 3
[0034] The invention is a shock-absorbing synthetic rubber, which is made of the following raw materials in parts by weight:
[0035] 12.6 parts of methyl methacrylate, 5.7 parts of silver-coated glass microbead core-shell composite particles, 4.8 parts of rosin polyoxyethylene sulfonate, 1.8 parts of polyethylene glycol octylphenyl ether, 3-ethoxy ethyl propionate 7.8 parts of ester, 5.2 parts of pine tar, 3.7 parts of magnesium oxide, 1.8 parts of coupling agent. The coupling agent is distearyloxy isopropyl aluminate.
[0036] The preparation method of above-mentioned damping synthetic rubber, comprises the following steps:
[0037] (1) Mix methyl methacrylate, silver-coated glass microbead core-shell composite particles and rosin polyoxyethylene sulfonate according to the above formula, and stir for 20 minutes at a stirring speed of 600 rpm;
[0038] (2) Then polyethylene glycol octylphenyl ether and ethyl 3-ethoxypropionate were added, stirred for 30 minutes, and the sti...
PUM
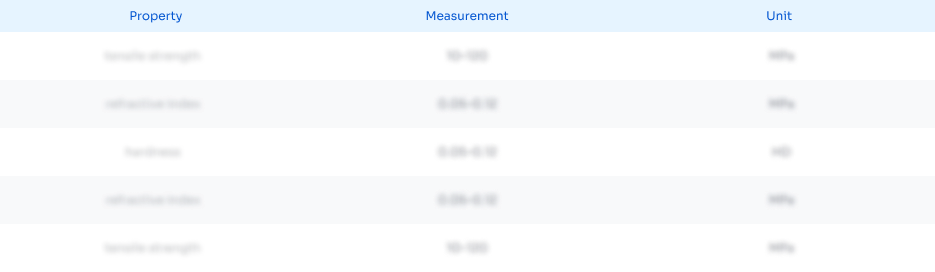
Abstract
Description
Claims
Application Information

- R&D
- Intellectual Property
- Life Sciences
- Materials
- Tech Scout
- Unparalleled Data Quality
- Higher Quality Content
- 60% Fewer Hallucinations
Browse by: Latest US Patents, China's latest patents, Technical Efficacy Thesaurus, Application Domain, Technology Topic, Popular Technical Reports.
© 2025 PatSnap. All rights reserved.Legal|Privacy policy|Modern Slavery Act Transparency Statement|Sitemap|About US| Contact US: help@patsnap.com