High-strength high-plasticity Cu-Zr-Zn amorphous composite and preparation method
An amorphous composite material, cu-zr-zn technology, applied in the field of amorphous composite materials and preparation, can solve the problem that the thermal stability of the B2CuZr phase will not be significantly improved and deteriorated, and achieve good plasticity and overcome low plasticity. Effect
- Summary
- Abstract
- Description
- Claims
- Application Information
AI Technical Summary
Problems solved by technology
Method used
Image
Examples
Embodiment 1
[0028] Step 1: Preparation of Cu 47.25 Zr 47.25 Zn 4.5 For a sample of 5g, weigh 1.9744g of pure Cu and 2.8342g of pure Zr, and put them in a polished water-cooled crucible with a good ratio;
[0029] Step 2: Evacuate the electric arc furnace to a vacuum of 5×10 -5 Pa, and then backfill Ar gas with a purity of 99.999% to one atmospheric pressure;
[0030] Step 3: Turn on the electric arc furnace and heat up to the melting point of the alloy prepared in step 1. After the alloy ingot is cooled, turn the alloy ingot over and melt it again. Repeat 3 times to mix the alloy evenly to obtain Cu 50 Zr 50 master alloy;
[0031] Step 4: Remove the surface scale of the master alloy and crush it, weigh 0.1914g of pure Zn, and mix it;
[0032] Step 5: Put it into the quartz test tube in the high-vacuum high-frequency induction melting-blow casting furnace;
[0033] Step 6: Evacuate the high-vacuum high-frequency induction melting-blow casting furnace to a vacuum of 5×10 -5 Pa, and ...
Embodiment 2
[0037] Step 1: Preparation of Cu 47.25 Zr 47.25 Zn 4.5 For a sample of 5g, weigh 1.9744g of pure Cu and 2.8342g of pure Zr, and put them in a polished water-cooled crucible with a good ratio;
[0038] Step 2: Evacuate the electric arc furnace to a vacuum of 5×10 -5 Pa, and then backfill Ar gas with a purity of 99.999% to one atmospheric pressure;
[0039] Step 3: Turn on the electric arc furnace and heat up to the melting point of the alloy prepared in step 1. After the alloy ingot is cooled, turn the alloy ingot over and melt it again. Repeat 4 times to mix the alloy evenly to obtain Cu 50 Zr 50 master alloy;
[0040] Step 4: Remove the surface scale of the master alloy and crush it, weigh 0.1914g of pure Zn, and mix it;
[0041] Step 5: Put it into the quartz test tube in the high-vacuum high-frequency induction melting-blow casting furnace;
[0042] Step 6: Evacuate the high-vacuum high-frequency induction melting-blow casting furnace to a vacuum of 5×10 -5Pa, and t...
PUM
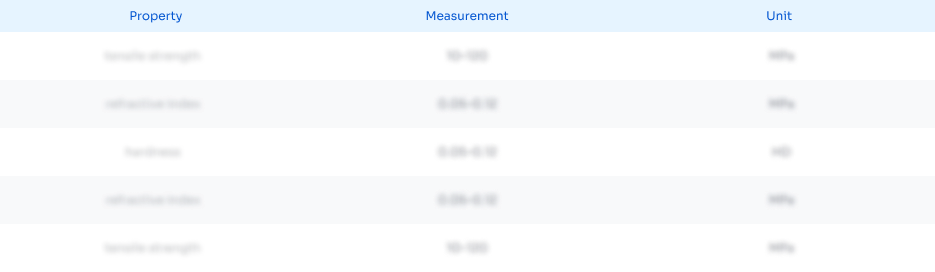
Abstract
Description
Claims
Application Information

- Generate Ideas
- Intellectual Property
- Life Sciences
- Materials
- Tech Scout
- Unparalleled Data Quality
- Higher Quality Content
- 60% Fewer Hallucinations
Browse by: Latest US Patents, China's latest patents, Technical Efficacy Thesaurus, Application Domain, Technology Topic, Popular Technical Reports.
© 2025 PatSnap. All rights reserved.Legal|Privacy policy|Modern Slavery Act Transparency Statement|Sitemap|About US| Contact US: help@patsnap.com