Method for separating and recycling heavy metal in mercury, selenium and arsenic containing dirt acid sludge
A technology of polluted acid slag and heavy metals, applied in the direction of magnesium sulfate, selenium/tellurium, etc., can solve the problems of doubled volume, large porosity of solidified body, waste of resources, etc., achieve resource recovery, avoid gypsum hazardous waste, The effect of avoiding secondary pollution
- Summary
- Abstract
- Description
- Claims
- Application Information
AI Technical Summary
Problems solved by technology
Method used
Image
Examples
Embodiment 1
[0030] Taking the dirty acid residue produced in the actual washing section of a zinc smelter as the treatment object, after preliminary dehydration, the concentration of each main component is: water content 15%, mercury content 210mg / g, selenium content 134mg / g, arsenic ion 304mg / g. The specific processing steps are as follows:
[0031] 1. Weigh 500g of dehydrated acid residue into a beaker, add 250g of magnesium oxide powder, stir to mix it thoroughly, and then let it stand for 30 minutes;
[0032] 2. Move the mixed dirty acid slag into a quartz tube, stuff an appropriate amount of quartz wool at both ends to prevent leakage of the dirty acid slag, and then put the quartz tube into a tubular electric heating furnace for roasting. The temperature is set to 600 ℃ and the temperature is stable. When the temperature is set, start timing and pass air into the quartz tube, roast for 1 hour, the air volume is 15L / min, continue to pass in air for 2 hours, and continuously pass the hot...
Embodiment 2
[0038] Taking the sewage acid residue produced in the actual washing section of a lead smelter as the treatment object, after preliminary dehydration, the concentration of each main component is: water content 20%, mercury content 178mg / g, selenium content 114mg / g, arsenic ion 332mg / g. The specific processing steps are as follows:
[0039] 1. Weigh 300g of the dehydrated acid residue into a beaker, add 150g of magnesium oxide powder, stir to mix it thoroughly, and then let it stand for 30 minutes;
[0040] 2. Move the mixed dirty acid slag into a quartz tube, stuff an appropriate amount of quartz wool at both ends to prevent leakage of the dirty acid slag, and then put the quartz tube into a tubular electric heating furnace for roasting. The temperature is set to 600 ℃ and the temperature is stable. When the temperature is set, start timing and pass air into the quartz tube, roast for 40 minutes, the air volume is 15L / min, continue to pass in air for 90 minutes, and the hot flue ...
Embodiment 3
[0046] Taking the sewage acid residue produced in the actual washing section of a lead smelter as the treatment object, after preliminary dehydration, the concentration of each main component is: moisture content 5%, mercury content 2mg / g, selenium content 200mg / g, arsenic ion 400mg / g. The specific processing steps are as follows:
[0047] 1. Weigh 300g of dehydrated acid residue into a beaker, add 30g of magnesium oxide powder, stir to mix it thoroughly, and then let it stand for 30 minutes;
[0048] 2. Move the mixed dirty acid slag into a quartz tube, stuff an appropriate amount of quartz wool at both ends to prevent the dirty acid slag from leaking, and then put the quartz tube into a blast furnace for roasting. The temperature is set at 400℃ and the temperature is stable. When the temperature is set, start timing and pass air into the quartz tube, roast for 5 hours, the air volume is 15L / min, continue to pass air for 90 minutes, and the hot flue gas discharged from the quart...
PUM
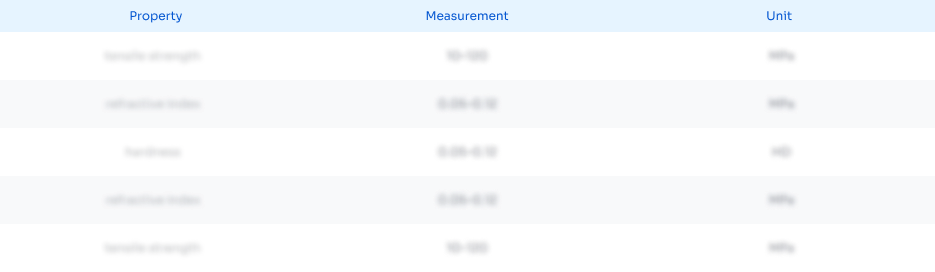
Abstract
Description
Claims
Application Information

- R&D Engineer
- R&D Manager
- IP Professional
- Industry Leading Data Capabilities
- Powerful AI technology
- Patent DNA Extraction
Browse by: Latest US Patents, China's latest patents, Technical Efficacy Thesaurus, Application Domain, Technology Topic, Popular Technical Reports.
© 2024 PatSnap. All rights reserved.Legal|Privacy policy|Modern Slavery Act Transparency Statement|Sitemap|About US| Contact US: help@patsnap.com