Method for forging formation of 16Cr3NiWMoVNbE forge piece
A technology for forgings and steel ingots, applied in the direction of metal processing equipment, etc., can solve the problems of low magnification and no improvement effect, and achieve the effect of avoiding residual stress
- Summary
- Abstract
- Description
- Claims
- Application Information
AI Technical Summary
Problems solved by technology
Method used
Examples
Embodiment approach
[0016] The chemical composition of the alloy steel is as follows:
[0017] alloy element
C
mn
Si
Cr
Ni
Mo
W
V
Nb
S
P
percentage content
0.193
0.64
0.83
2.76
1.26
0.48
1.19
0.43
0.14
0.00015
0.012
[0018] The steps of this method are as follows:
[0019] Take a 16Cr3NiWMoVNbE steel ingot of a certain specification, put it into a heating furnace and heat it to 350°C-450°C for 3 hours; then raise its temperature to 1020°C-1050°C at a speed of 90°C-100°C, and keep it for 3 hours; Raise the temperature from 70°C to 80°C to 1200°C to 1250°C, and keep the temperature for 3 hours.
[0020] Put the steel ingot vertically on the bottom plate of the press, and drive the upper cutting board of the press to upset the steel ingot. The pressing amount of the upper cutting board for each upsetting is 40mm~45mm, and after each pressing, stop for 3s~5s; When the downward pressure r...
PUM
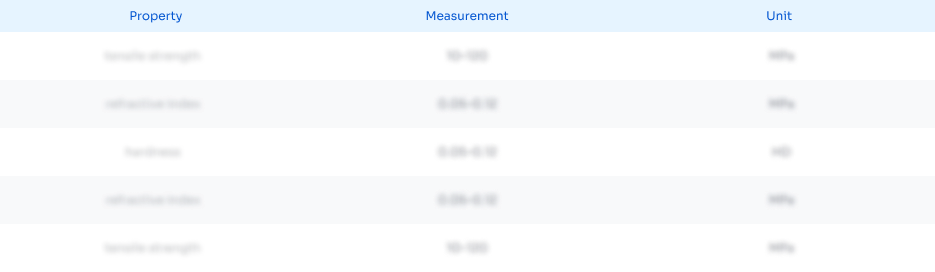
Abstract
Description
Claims
Application Information

- Generate Ideas
- Intellectual Property
- Life Sciences
- Materials
- Tech Scout
- Unparalleled Data Quality
- Higher Quality Content
- 60% Fewer Hallucinations
Browse by: Latest US Patents, China's latest patents, Technical Efficacy Thesaurus, Application Domain, Technology Topic, Popular Technical Reports.
© 2025 PatSnap. All rights reserved.Legal|Privacy policy|Modern Slavery Act Transparency Statement|Sitemap|About US| Contact US: help@patsnap.com