Leather production technique
A production process and leather technology, applied in the field of leather production technology, can solve the problems of large environmental damage to the human body, high pressure on the spraying machine, and high cost, achieve not easy creases, improve resistance to bending and bending, and excellent resistance to bending. Effect
- Summary
- Abstract
- Description
- Claims
- Application Information
AI Technical Summary
Problems solved by technology
Method used
Examples
Embodiment 1
[0031] A kind of production technology of leather is characterized in that, comprises the following steps:
[0032] 1) Material selection, leather material selection;
[0033] 2) Retanning, retanning the leather;
[0034] 3) undercoat, carry out undercoat with cationic wax, epoxy resin water-soluble coating and dry;
[0035] 4) hot, hot with a roller burner;
[0036] 5) Intermediate coating, use leather followed by epoxy resin water-soluble paint to carry out intermediate coating and dry;
[0037] 6) top coat, carry out top coat and bake dry with epoxy resin, acrylic resin, leather cracking resin and leather pigment water-soluble paint;
[0038] 7) washing with water, washing with water;
[0039] 8) Dyeing, dyeing the leather surface;
[0040] 9) fatliquoring, fatliquoring coating is carried out to the surface of leather material;
[0041] 10) Drumming is performed to obtain finished leather.
[0042] In the retanning step, after adding 80 parts by weight of water at 25...
Embodiment 2
[0052] A kind of production technology of leather is characterized in that, comprises the following steps:
[0053] 1) Material selection, leather material selection;
[0054] 2) Retanning, retanning the leather;
[0055] 3) undercoat, carry out undercoat with cationic wax, epoxy resin water-soluble coating and dry;
[0056] 4) hot, hot with a roller burner;
[0057] 5) Intermediate coating, use leather followed by epoxy resin water-soluble paint to carry out intermediate coating and dry;
[0058] 6) top coat, carry out top coat and bake dry with epoxy resin, acrylic resin, leather cracking resin and leather pigment water-soluble paint;
[0059] 7) washing with water, washing with water;
[0060] 8) Dyeing, dyeing the leather surface;
[0061] 9) fatliquoring, fatliquoring coating is carried out to the surface of leather material;
[0062] 10) Drumming is performed to obtain finished leather.
[0063] In the retanning step, after adding 100 parts by weight of water at 28°...
Embodiment 3
[0073] A kind of production technology of leather is characterized in that, comprises the following steps:
[0074] 1) Material selection, leather material selection;
[0075] 2) Retanning, retanning the leather;
[0076] 3) undercoat, carry out undercoat with cationic wax, epoxy resin water-soluble coating and dry;
[0077] 4) hot, hot with a roller burner;
[0078] 5) Intermediate coating, use leather followed by epoxy resin water-soluble paint to carry out intermediate coating and dry;
[0079] 6) top coat, carry out top coat and bake dry with epoxy resin, acrylic resin, leather cracking resin and leather pigment water-soluble paint;
[0080] 7) washing with water, washing with water;
[0081] 8) Dyeing, dyeing the leather surface;
[0082] 9) fatliquoring, fatliquoring coating is carried out to the surface of leather material;
[0083] 10) Drumming is performed to obtain finished leather.
[0084] In the retanning step, after adding 90 parts by weight of water at 26...
PUM
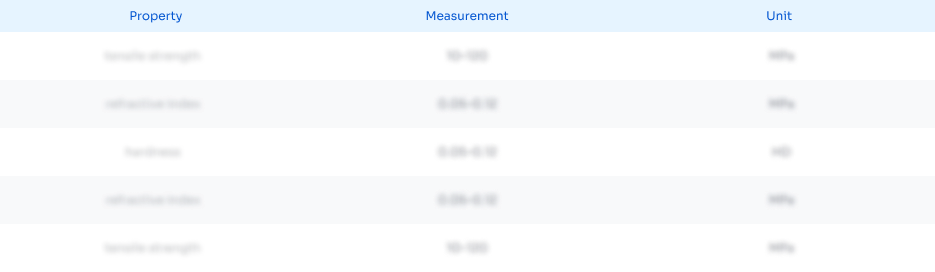
Abstract
Description
Claims
Application Information

- R&D
- Intellectual Property
- Life Sciences
- Materials
- Tech Scout
- Unparalleled Data Quality
- Higher Quality Content
- 60% Fewer Hallucinations
Browse by: Latest US Patents, China's latest patents, Technical Efficacy Thesaurus, Application Domain, Technology Topic, Popular Technical Reports.
© 2025 PatSnap. All rights reserved.Legal|Privacy policy|Modern Slavery Act Transparency Statement|Sitemap|About US| Contact US: help@patsnap.com