Preparation method of high-weathering-resistance and high-wear-resistance polyurethane surface layer resin for vehicle interior decoration leathers
A surface layer resin and interior leather technology, which is applied in the field of polyurethane resin preparation, can solve the problems of high wear resistance and heat resistance, reduced wear resistance, and poor weather resistance of leather used in automotive interiors. The preparation process is easy to control, improves cracking, and increases the effect of low temperature flexibility
- Summary
- Abstract
- Description
- Claims
- Application Information
AI Technical Summary
Problems solved by technology
Method used
Examples
Embodiment 1
[0018] A preparation method of high weather resistance and high wear resistance polyurethane surface layer resin for automotive interior leather, comprising the following processing steps: adding 300 g of polycarbonate diol, 3.7 g of ethylene glycol, and primary carbon with a molecular weight of about 2000 in a reaction kettle 15g of hydroxyl silicone oil, 10.8g of 1,4-butanediol, 1010 (BASF) anti-heat oxidant: 0.5g, heat up to 50°C, stir until the polycarbonate diol is dissolved, then stir for 20 minutes, then add 4,4 -Dicyclohexylmethane diisocyanate 159g , Stir evenly, slowly raise the temperature to 110°C, and keep it for 120min, then add catalyst M20 (air chemistry): 0.1g, react at 105°C for 120min to prepare a prepolymer, test the NCO value, when the NCO value is lower than the theoretical value , add 200g of toluene and 480g of dimethylformamide to dissolve the prepolymer and lower the temperature to below 50°C, dilute 4,4-diamino-dicyclohexylmethane with toluene 3 time...
Embodiment 2
[0020] A method for preparing a high-weather-resistant and high-wear-resistant polyurethane surface layer resin for automotive interior leather, comprising the following steps: adding 300 g of polycarbonate diol and silicone polyol 9565 to a reaction kettle (manufacturer: Bicker, Germany) : 15g, 1,4-butanediol: 10.8g, 0.5g of anti-heat oxidant, heat up to 50°C, stir for 20min, after the polycarbonate diol is dissolved, add 130.8g of 4,4-dicyclohexylmethane diisocyanate , Stir evenly, then slowly raise the temperature to 110°C and keep it for 120min, then add catalyst M20 (American Air Chemicals): 0.1g, react at 105°C for 120min to prepare a prepolymer, test the NCO value, when the NCO value is lower than the theory value, add 200g of toluene and 480kg of dimethylformamide to dissolve the prepolymer and lower the temperature to below 50°C, dilute 4,4-diamino-dicyclohexylmethane with toluene 3 times, and use a constant pressure dropping device to react Add diluted 4,4-diamino-di...
Embodiment 3
[0022] A preparation method of high weather resistance and high wear resistance polyurethane surface layer resin for automotive interior leather, comprising the following processing steps: adding polycarbonate diol 300g, silicone polyol 8492 (German competition): 15g, 1 , 10.8g of 4-butanediol, 0.5g of anti-heat oxidant, heat up to 50°C, stir for 20min, add 84g of hexylene diethylene cyanate after the polycarbonate diol is dissolved, stir evenly, then slowly heat up to 130°C , and keep it for 120min, then add catalyst M20: 0.1g, react at 105°C for 120min to prepare a prepolymer, test the NCO value, when the NCO value is lower than the theoretical value, add 250g of toluene and 350kg of dimethylformamide to dissolve the prepolymer polymerize and lower the temperature below 50°C, dilute isophorone diamine 3 times with toluene, and use a constant pressure dropping device to drop the diluted isophorone diamine into the reaction kettle, when the viscosity meets the process requireme...
PUM
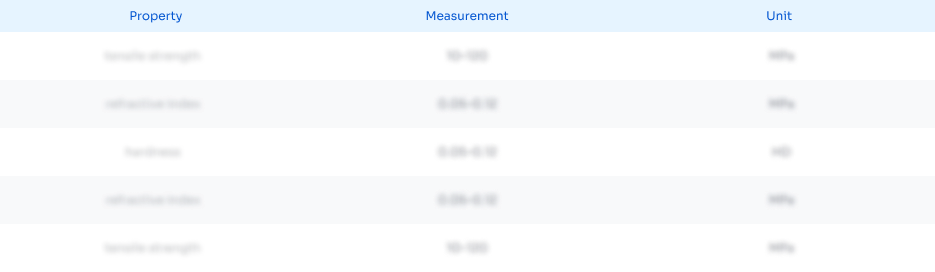
Abstract
Description
Claims
Application Information

- Generate Ideas
- Intellectual Property
- Life Sciences
- Materials
- Tech Scout
- Unparalleled Data Quality
- Higher Quality Content
- 60% Fewer Hallucinations
Browse by: Latest US Patents, China's latest patents, Technical Efficacy Thesaurus, Application Domain, Technology Topic, Popular Technical Reports.
© 2025 PatSnap. All rights reserved.Legal|Privacy policy|Modern Slavery Act Transparency Statement|Sitemap|About US| Contact US: help@patsnap.com