Method for directly preparing microcrystal glass through hot steel slag
A technology of glass ceramics and slag, which is applied in the field of building decoration materials, can solve the problems of reduced utilization efficiency, achieve the effects of alleviating a large amount of waste, simple production process, and easy operation
- Summary
- Abstract
- Description
- Claims
- Application Information
AI Technical Summary
Problems solved by technology
Method used
Image
Examples
example 1
[0029] The preparation method of directly using hot-melt steel slag glass ceramics is as follows:
[0030] a. Use a certain amount of auxiliary materials: quartz sand, aluminum stone powder, soda ash, barium carbonate, and titanium oxide are added to the steel slag. The mass ratio of these auxiliary materials to the steel slag is 35:100; the applicable chemical composition of the steel slag Range: SiO 2 (20wt%wt%), Al 2 o 3 (8wt%), CaO (55wt%), MgO (7wt%), Fe 2 o 3 (10wt%); the specific addition amount of auxiliary materials needs to refer to the composition of steel slag in actual production. It is necessary to ensure that the chemical composition of the molten glass after mixing is within the following range: SiO 2 (55wt%), Al 2 o 3 (8wt%), CaO (16wt%), MgO (1wt%), BaO (8wt%), Na 2 O (6wt%), Fe 2 o 3 (5wt%), TiO 2 (1 wt%).
[0031] b. Transport the steel slag with a certain quality in liquid state through the steel slag transport tank 1 to the front transition po...
example 2
[0036] a. Use a certain amount of auxiliary materials: quartz sand, aluminum stone powder, soda ash, barium carbonate, and titanium oxide are added to the steel slag. The mass ratio of these auxiliary materials to the steel slag is: 48:100; the applicable chemical composition of the steel slag Range: SiO 2 (23wt%), Al 2 o 3 (6wt%), CaO (52wt%), MgO (7wt%), Fe 2 o 3 (5wt%); the specific addition amount of auxiliary materials needs to refer to the composition of steel slag in actual production. It is necessary to ensure that the chemical composition of the molten glass after mixing is within the following range: SiO 2 (58wt%), Al 2 o 3 (5wt%8), CaO (20wt%), MgO (2wt%), BaO (6wt%), Na 2 O (4wt%), Fe 2 o 3 (4wt%), TiO 2 (1 wt%).
[0037] b. Transport the steel slag with a certain quality in liquid state through the steel slag transport tank 1 to the front transition pool 3 of the steel slag melting furnace and throw it into the glass kiln feeding port through the refrac...
example 3
[0042] a. Use a certain amount of auxiliary materials: quartz sand, aluminum stone powder, soda ash, barium carbonate, and titanium oxide are added to the steel slag. The mass ratio of these auxiliary materials to the steel slag is: 58:100; the applicable chemical composition of the steel slag Range: SiO 2 (25wt%), Al 2 o 3 (2wt%), CaO (48wt%), MgO (7wt%), Fe 2 o 3 (5wt%-); the specific addition amount of auxiliary materials needs to refer to the composition of steel slag in actual production. It is necessary to ensure that the chemical composition of the molten glass after mixing is within the following range: SiO 2 (60wt%), Al 2 o 3 (5wt%), CaO (21wt%), MgO (1wt%), BaO (5wt%), Na 2 O (3wt%), Fe 2 o 3 (4wt%), TiO 2 (1 wt%).
[0043] b. Transport the steel slag with a certain quality in liquid state through the steel slag transport tank 1 to the front transition pool 3 of the steel slag melting furnace and throw it into the glass kiln feeding port through the refrac...
PUM
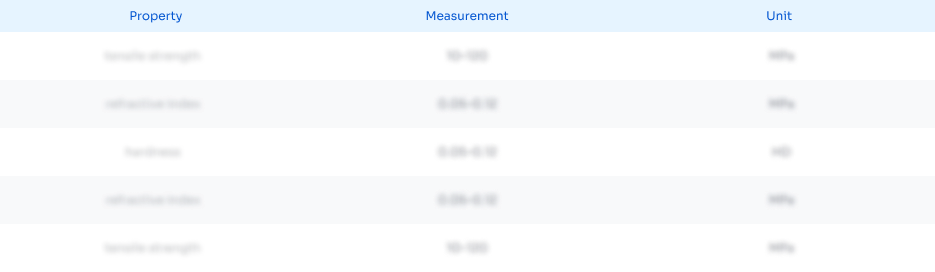
Abstract
Description
Claims
Application Information

- R&D
- Intellectual Property
- Life Sciences
- Materials
- Tech Scout
- Unparalleled Data Quality
- Higher Quality Content
- 60% Fewer Hallucinations
Browse by: Latest US Patents, China's latest patents, Technical Efficacy Thesaurus, Application Domain, Technology Topic, Popular Technical Reports.
© 2025 PatSnap. All rights reserved.Legal|Privacy policy|Modern Slavery Act Transparency Statement|Sitemap|About US| Contact US: help@patsnap.com