Solid oxide fuel cell with anti-carbon function
A solid oxide and fuel cell technology, applied in solid electrolyte fuel cells, battery electrodes, circuits, etc., to achieve the effects of reducing deposition, increasing the amount of catalyst, and improving catalytic conversion efficiency
- Summary
- Abstract
- Description
- Claims
- Application Information
AI Technical Summary
Problems solved by technology
Method used
Image
Examples
Embodiment 1
[0030] Using the classic NiO-YSZ / YSZ / LSM-YSZ as a single cell, Al 2 O 3 As the substrate of the catalyst layer, NiO / BaO / CeO synthesized in a certain proportion 2 The mixture is the catalyst:
[0031] (1) Preparation of catalyst powder: according to Ni:BaO:CeO 2 The mass fraction is 13:2:85, respectively weigh nickel nitrate, barium nitrate, cerium nitrate, dissolve in deionized water, add glycine, and the molar ratio of glycine to total metal ions (G / M n+ ) is 3:1. Put it on an electric furnace to heat and stir, and after the water is evaporated to dryness, the primary powder is obtained by spontaneous combustion, and then placed in an oven at 240°C for 8 hours. After cooling, it was calcined in a muffle furnace at 850 °C for 2 h, and the heating rate was 5 °C min -1 .
[0032] (2) Preparation of catalyst layer: Weigh 0.3 g of Al with a mass ratio of 9:1 2 O 3 Mix the powder with PVB uniformly, press the catalyst layer substrate with a tableting die at 144MPa, and then...
Embodiment 2
[0038] Using NiO-YSZ / YSZ / LSM-YSZ as a single cell and YSZ as a catalyst substrate, the synthesized NiO / BaO / CeO 2 for catalyst:
[0039] The preparation method is the same as in Example 1, except that the Al in Example 1 2 O 3 Replace with YSZ, see battery discharge life Figure 5 .
Embodiment 3
[0041] Using NiO-YSZ / YSZ / LSM-YSZ as a single cell, Al 2 O 3 As a catalyst substrate, NiO / BaO / CeO synthesized in a certain proportion 2 / Al 2 O 3 for catalyst:
[0042] (1) Preparation of catalyst powder: Ni:BaO:CeO 2 :Al 2 O 3 The mass fraction is 13:2:42.5:42.5. Weigh nickel nitrate, barium nitrate, cerium nitrate, aluminum nitrate, dissolve in deionized water, add glycine, and the molar ratio of glycine to metal ions (G / M n+ ) ratio is 3:1. Put it on an electric furnace to heat and stir, and after the water is evaporated to dryness, it will spontaneously ignite to obtain a primary powder, and put it in an oven to dry at 240°C for 8 hours. After cooling, it was calcined in a muffle furnace at 850 °C for 2 h, and the heating rate was 5 °C min -1 .
[0043] (2)-(5) are the same as in Example 1, the constant current discharge life of the battery is shown in Image 6 .
PUM
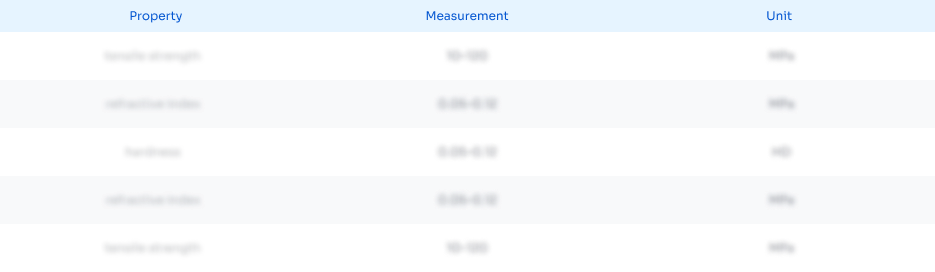
Abstract
Description
Claims
Application Information

- R&D
- Intellectual Property
- Life Sciences
- Materials
- Tech Scout
- Unparalleled Data Quality
- Higher Quality Content
- 60% Fewer Hallucinations
Browse by: Latest US Patents, China's latest patents, Technical Efficacy Thesaurus, Application Domain, Technology Topic, Popular Technical Reports.
© 2025 PatSnap. All rights reserved.Legal|Privacy policy|Modern Slavery Act Transparency Statement|Sitemap|About US| Contact US: help@patsnap.com