A kind of preparation method of hearth roller of normalizing furnace
A hearth roll and normalizing furnace technology, which is applied in the field of refractory materials, can solve the problems of shortening the service life of fiber hearth rolls, affecting the output of steel plates, and shedding of fiber sheets, and achieves low material cost, high self-adaptive pressing performance, and finished products rate-enhancing effect
- Summary
- Abstract
- Description
- Claims
- Application Information
AI Technical Summary
Problems solved by technology
Method used
Examples
Embodiment 1
[0017] A preparation method for a hearth roll of a normalizing furnace, comprising the following steps:
[0018] ① Preparation of slurry: put 15wt% asbestos fiber, 3wt% sepiolite, 2wt% alumina powder, 40wt% water-based thermosetting acrylic resin, and 40wt% water into a homogenizer, and stir at high speed for 15 minutes to make a uniform slurry;
[0019] ②Preparation of roller rings: pump the uniform slurry into the forming mold with a non-clogging pump, the pressing pressure of the upper die head is 10 tons, and at the same time vacuum suction and filter, demold, and dry in a drying kiln at 60°C for 24 hours, and at 120°C for 24 hours. Make a 5mm thick roll ring;
[0020] ③ Furnace roller pressing: put the roller ring on the furnace roller mandrel, press and install every 20 pieces with a CNC press-fitting machine with a mechanical output of 50 tons, until the furnace roller is installed;
[0021] ④ Furnace roller surface treatment: use CNC machine tools to turn the surface ...
Embodiment 2
[0023] A preparation method for a hearth roll of a normalizing furnace, comprising the following steps:
[0024] ① Preparation of slurry: put 14wt% asbestos fiber, 4wt% sepiolite, 2wt% alumina powder, 40wt% water-based thermosetting acrylic resin, and 40wt% water into a homogenizer, and stir at high speed for 18 minutes to make a uniform slurry;
[0025] ②Preparation of roller rings: pump the uniform slurry into the forming mold with a non-clogging pump. The pressing pressure of the upper die head is 10 tons. Make a 6mm thick roll ring;
[0026] ③ Furnace roller pressing: put the roller ring on the furnace roller mandrel, press and install every 20 pieces with a CNC press-fitting machine with a mechanical output of 50 tons, until the furnace roller is installed;
[0027] ④ Furnace roller surface treatment: use CNC machine tools to turn the surface of the installed furnace roller to make a furnace roller with a flat surface.
Embodiment 3
[0029] A preparation method for a hearth roll of a normalizing furnace, comprising the following steps:
[0030] ① Preparation of slurry: put 16wt% asbestos fiber, 3wt% sepiolite, 2wt% coke powder, 39wt% water-based thermosetting acrylic resin, 40wt% water into a homogenizer, and stir at high speed for 16 minutes to make a uniform slurry;
[0031] ②Preparation of roller rings: pump the uniform slurry into the forming mold with a non-clogging pump. The pressing pressure of the upper die head is 10 tons. Make a 5mm thick roll ring;
[0032] ③ Furnace roller pressing: put the roller ring on the furnace roller mandrel, press and install every 20 pieces with a CNC press-fitting machine with a mechanical output of 50 tons, until the furnace roller is installed;
[0033] ④ Furnace roller surface treatment: use CNC machine tools to turn the surface of the installed furnace roller to make a furnace roller with a flat surface.
PUM
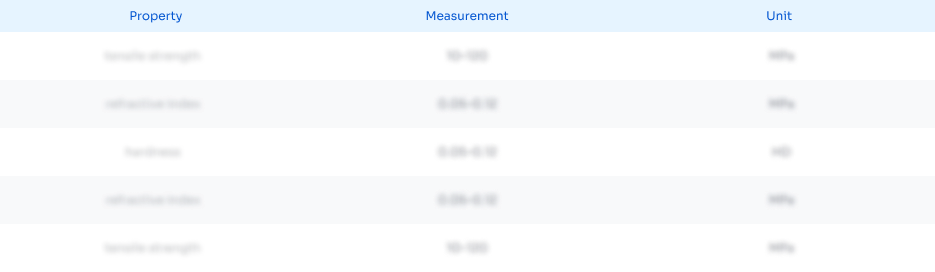
Abstract
Description
Claims
Application Information

- R&D Engineer
- R&D Manager
- IP Professional
- Industry Leading Data Capabilities
- Powerful AI technology
- Patent DNA Extraction
Browse by: Latest US Patents, China's latest patents, Technical Efficacy Thesaurus, Application Domain, Technology Topic, Popular Technical Reports.
© 2024 PatSnap. All rights reserved.Legal|Privacy policy|Modern Slavery Act Transparency Statement|Sitemap|About US| Contact US: help@patsnap.com