Multi-station continuous hot stamping production line and method
A technology of hot stamping and production line, which is applied in the field of hot stamping, and can solve problems such as surface wear of scale stamping dies, long time-consuming transfer of hot blanks, and reduced heating efficiency, etc., so as to prolong the life of punching dies and improve energy utilization and heating efficiency , High heating efficiency
- Summary
- Abstract
- Description
- Claims
- Application Information
AI Technical Summary
Problems solved by technology
Method used
Image
Examples
Embodiment Construction
[0039] In order to make the object, technical solution and advantages of the present invention clearer, the present invention will be further described in detail below in conjunction with the accompanying drawings and embodiments. It should be understood that the specific embodiments described here are only used to explain the present invention, not to limit the present invention.
[0040] Such as Figure 1-Figure 5 As shown, a multi-station continuous hot stamping production line includes a loading table 2, a feeding robot 3, a press unit, a feeding robot 5, a quenching device, an unloading robot 7 and a conveyor belt 8 arranged in sequence; wherein,
[0041] The feeding platform 2 is used to place the prefabricated blank 1 after blanking;
[0042] The feeding robot 3 is used to transfer the prefabricated blank 1 to the press unit;
[0043] The press unit includes a heating device, a mold device and at least one press for installing the mold device. The heating device is us...
PUM
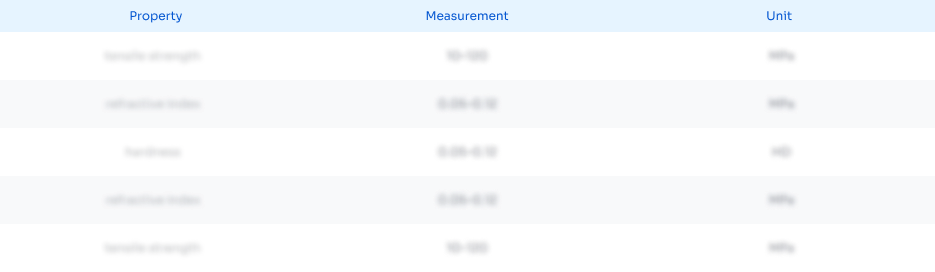
Abstract
Description
Claims
Application Information

- R&D
- Intellectual Property
- Life Sciences
- Materials
- Tech Scout
- Unparalleled Data Quality
- Higher Quality Content
- 60% Fewer Hallucinations
Browse by: Latest US Patents, China's latest patents, Technical Efficacy Thesaurus, Application Domain, Technology Topic, Popular Technical Reports.
© 2025 PatSnap. All rights reserved.Legal|Privacy policy|Modern Slavery Act Transparency Statement|Sitemap|About US| Contact US: help@patsnap.com