Heat-resistant corrosion-resistant woven bag
A corrosion-resistant, woven bag technology, applied in the field of plastic materials, can solve the problems of corrosion resistance and heat resistance that cannot meet the requirements of the society, short service life, and limited application range, etc., to improve the elongation at break and reduce the surface Can, improve the effect of strength
- Summary
- Abstract
- Description
- Claims
- Application Information
AI Technical Summary
Problems solved by technology
Method used
Examples
Embodiment 1
[0034] A heat-resistant and corrosion-resistant woven bag proposed by the present invention is made of polyvinyl chloride / thermoplastic polyurethane composite material, wherein the raw materials of the polyvinyl chloride / thermoplastic polyurethane composite material include the following components by weight: polyvinyl chloride 40 parts of ethylene, 60 parts of thermoplastic polyurethane, 20 parts of methyl vinyl silicone rubber, 25 parts of nitrile rubber, 5 parts of acrylonitrile-butadiene-styrene copolymer, 3 parts of stearic acid, 0.5 parts of sulfur, zinc oxide 1.5 parts, 8 parts of calcium stearate, 5 parts of zinc stearate, 2 parts of bis(2-hydroxyethyl)amino(trimethylol)methane, 8 parts of stannous pyrophosphate, diisooctyl dimercaptoacetate 2 parts of n-octyl tin, 20 parts of barium sulfate, 10 parts of light calcium carbonate, 10 parts of aluminum hydroxide, 5 parts of rare earth coupling agent, 10 parts of decabromodiphenylethane, 6 parts of antimony trioxide, bis-pe...
Embodiment 2
[0040] A heat-resistant and corrosion-resistant woven bag proposed by the present invention is made of polyvinyl chloride / thermoplastic polyurethane composite material, wherein the raw materials of the polyvinyl chloride / thermoplastic polyurethane composite material include the following components by weight: polyvinyl chloride 80 parts of ethylene, 20 parts of thermoplastic polyurethane, 40 parts of methyl vinyl silicone rubber, 10 parts of nitrile rubber, 15 parts of acrylonitrile-butadiene-styrene copolymer, 1 part of stearic acid, 2 parts of sulfur, zinc oxide 0.4 parts, 20 parts of calcium stearate, 2 parts of zinc stearate, 8 parts of bis(2-hydroxyethyl)amino(trimethylol)methane, 3 parts of stannous pyrophosphate, diisooctyl dimercaptoacetate 6 parts of n-octyl tin, 8 parts of barium sulfate, 25 parts of light calcium carbonate, 3 parts of aluminum hydroxide, 9 parts of rare earth coupling agent, 5 parts of decabromodiphenylethane, 15 parts of antimony trioxide, bis-penta...
Embodiment 3
[0046] A heat-resistant and corrosion-resistant woven bag proposed by the present invention is made of polyvinyl chloride / thermoplastic polyurethane composite material, wherein the raw materials of the polyvinyl chloride / thermoplastic polyurethane composite material include the following components by weight: polyvinyl chloride 64 parts of ethylene, 35 parts of thermoplastic polyurethane, 30 parts of methyl vinyl silicone rubber, 20 parts of nitrile rubber, 9 parts of acrylonitrile-butadiene-styrene copolymer, 2.2 parts of stearic acid, 1 part of sulfur, zinc oxide 1.3 parts, 12 parts of calcium stearate, 4.2 parts of zinc stearate, 5.7 parts of bis(2-hydroxyethyl)amino(trimethylol)methane, 5.3 parts of stannous pyrophosphate, diisooctyl dimercaptoacetate 4 parts of n-octyl tin, 16 parts of barium sulfate, 18 parts of light calcium carbonate, 7 parts of aluminum hydroxide, 6.8 parts of rare earth coupling agent, 8.5 parts of decabromodiphenylethane, 9 parts of antimony trioxide...
PUM
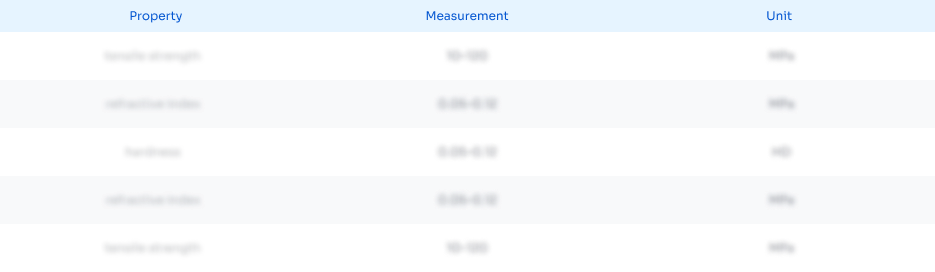
Abstract
Description
Claims
Application Information

- R&D
- Intellectual Property
- Life Sciences
- Materials
- Tech Scout
- Unparalleled Data Quality
- Higher Quality Content
- 60% Fewer Hallucinations
Browse by: Latest US Patents, China's latest patents, Technical Efficacy Thesaurus, Application Domain, Technology Topic, Popular Technical Reports.
© 2025 PatSnap. All rights reserved.Legal|Privacy policy|Modern Slavery Act Transparency Statement|Sitemap|About US| Contact US: help@patsnap.com