Preheating Scrap Steel Continuous Feeding System Based on Electric Arc Furnace Waste Heat Recovery Channel and Its Application Method
A waste heat recovery and feeding system technology, which is applied in electric furnaces, furnaces, waste heat treatment, etc., can solve the problems of uncommon application, insufficient contact between gas and scrap steel, and low preheating temperature of scrap steel
- Summary
- Abstract
- Description
- Claims
- Application Information
AI Technical Summary
Problems solved by technology
Method used
Image
Examples
Embodiment Construction
[0071] The present invention will be further described below in conjunction with the accompanying drawings and embodiments.
[0072] The implementation of the electric arc furnace waste heat recovery channel is as follows:
[0073] Such as figure 1 The electric arc furnace waste heat recovery channel includes a draft tube 10 connected and fixed on the fourth hole of the electric arc furnace, and also includes an upright heat exchange storage box 30, and the side air inlet at the bottom of the heat exchange storage box 30 32 is externally connected with a transition pipe 20 that is connected to the opening of the top of the draft tube and is connected with an inclined downward. A feeding cart 70 is installed at the bottom of the chamber 31 of the heat exchange storage tank 30. The feeding cart 70 is driven horizontally by a feeding oil cylinder 71. Continuously push the preheated steel scrap into the transition pipe 20 intermittently for a certain period of time, and the prehe...
PUM
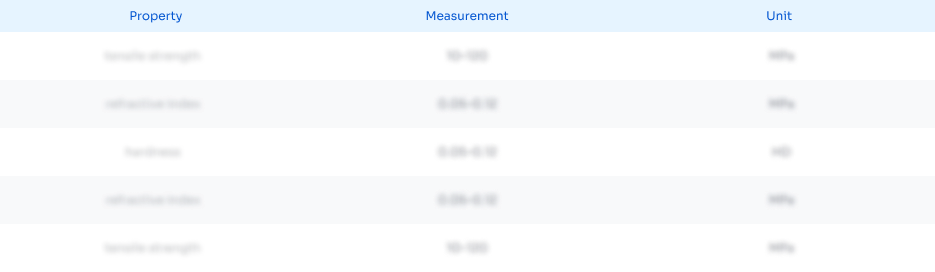
Abstract
Description
Claims
Application Information

- R&D
- Intellectual Property
- Life Sciences
- Materials
- Tech Scout
- Unparalleled Data Quality
- Higher Quality Content
- 60% Fewer Hallucinations
Browse by: Latest US Patents, China's latest patents, Technical Efficacy Thesaurus, Application Domain, Technology Topic, Popular Technical Reports.
© 2025 PatSnap. All rights reserved.Legal|Privacy policy|Modern Slavery Act Transparency Statement|Sitemap|About US| Contact US: help@patsnap.com