A hdi board manufacturing process to improve blind hole pad removal
A manufacturing process and blind hole technology, which is applied in the direction of printed circuit manufacturing, electrical connection formation of printed components, electrical components, etc., to achieve the effects of improving microcracks in blind holes, improving abrasive belt grinding efficiency, and reducing costs
- Summary
- Abstract
- Description
- Claims
- Application Information
AI Technical Summary
Problems solved by technology
Method used
Examples
Embodiment
[0016] This embodiment discloses a manufacturing process of an HDI board for improving the blind hole de-padging. The specific process steps are as follows:
[0017] S1: Open the core board according to the size of the puzzle;
[0018] S2: Finish the inner circuit exposure with 6 grid exposure ruler, and etch the circuit pattern after development;
[0019] S3: Check and correct defects such as open and short circuits in the inner layer;
[0020] S4: Pressing: browning, the speed of browning is according to the bottom copper thickness, and then the appropriate lamination conditions are selected according to the sheet material Tg for pressing, and the outer layer of copper foil follows the customer's requirements for the thickness of the finished surface to choose copper foil ;
[0021] S5: According to the thickness of the plate, use the drilling data for inner laser drilling processing;
[0022] S6: Conduct inner layer copper immersion, and the backlight test is 9.5 level;
[0023] S7: E...
PUM
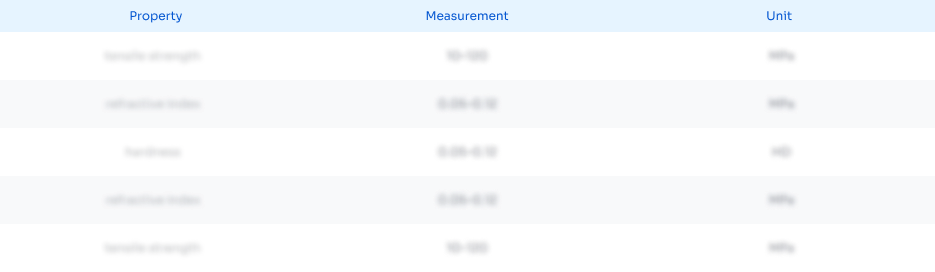
Abstract
Description
Claims
Application Information

- R&D Engineer
- R&D Manager
- IP Professional
- Industry Leading Data Capabilities
- Powerful AI technology
- Patent DNA Extraction
Browse by: Latest US Patents, China's latest patents, Technical Efficacy Thesaurus, Application Domain, Technology Topic, Popular Technical Reports.
© 2024 PatSnap. All rights reserved.Legal|Privacy policy|Modern Slavery Act Transparency Statement|Sitemap|About US| Contact US: help@patsnap.com