Fabrication method for high-aspect rate copper-thickness printed circuit board (pcb) solder mask
A technology with a high aspect ratio and a manufacturing method, which is applied in the directions of printed circuit manufacturing, printed circuit secondary processing, and sequence of processing steps, to achieve good market prospects and application value, and to improve the yield rate
- Summary
- Abstract
- Description
- Claims
- Application Information
AI Technical Summary
Problems solved by technology
Method used
Examples
Embodiment 1
[0019] This embodiment discloses a method for manufacturing a high-aspect-ratio copper-thick pcb solder resist. The method is as follows: the method is sequentially divided into three steps: a plug hole treatment step, a circuit oil spraying step, and a silk screen surface step.
[0020] (1) Carry out pre-treatment grinding plate for the first time to the whole board of circuit board, then carry out plug hole treatment step, then carry out pre-baking, development, inspection, back exposure, post-baking processing to plug hole order separately; Described back exposure step The energy value of the middle back exposure is 800 mJ / time; the pre-baking temperature in the plug hole processing step is 75° C., and the time is 45 minutes; the exposure ruler in the exposure step is 9-13 grids. The post-baking treatment is divided into eight sections, and the specific temperature and time of each section are: 55°C×60min, 65°C×60min, 75°C×60min, 85°C×60min, 95°C×60min, 110°C×60min, 130°C ℃...
Embodiment 2
[0024] This embodiment discloses a method for manufacturing a high-aspect-ratio copper-thick pcb solder resist. The method is as follows: the method is sequentially divided into three steps: a plug hole treatment step, a circuit oil spraying step, and a silk screen surface step.
[0025] (1) Carry out pre-treatment grinding plate for the first time to the whole board of circuit board, then carry out plug hole treatment step, then carry out pre-baking, development, inspection, back exposure, post-baking processing to plug hole order separately; Described back exposure step The energy value of the middle back exposure is 800 mJ / time, and the number of times is twice; the pre-baking temperature in the plugging treatment step is 75°C, and the time is 45 minutes; the exposure ruler in the exposure step is 9-13 grids. The post-baking treatment is divided into eight sections, and the specific temperature and time of each section are: 55°C×60min, 65°C×60min, 75°C×60min, 85°C×60min, 95°...
PUM
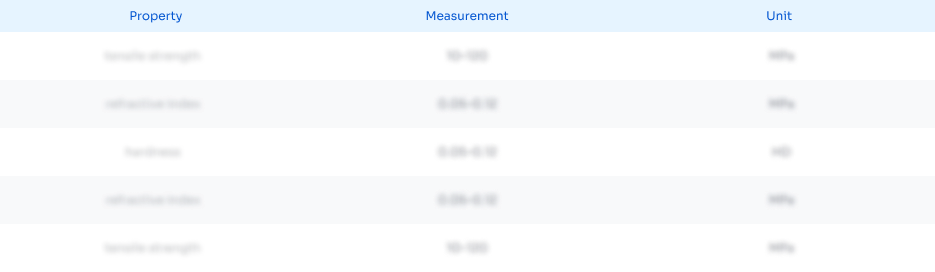
Abstract
Description
Claims
Application Information

- R&D
- Intellectual Property
- Life Sciences
- Materials
- Tech Scout
- Unparalleled Data Quality
- Higher Quality Content
- 60% Fewer Hallucinations
Browse by: Latest US Patents, China's latest patents, Technical Efficacy Thesaurus, Application Domain, Technology Topic, Popular Technical Reports.
© 2025 PatSnap. All rights reserved.Legal|Privacy policy|Modern Slavery Act Transparency Statement|Sitemap|About US| Contact US: help@patsnap.com