Spherical catalytic microelectrolytic environment-friendly material and preparation method therefor
An environmentally friendly material, micro-electrolysis technology, applied in chemical instruments and methods, water/sewage treatment, water/sludge/sewage treatment, etc.
- Summary
- Abstract
- Description
- Claims
- Application Information
AI Technical Summary
Problems solved by technology
Method used
Image
Examples
Embodiment 1
[0024] Embodiment 1 130-147 parts of fine iron powder, 25-29 parts of coal, 1-5 parts of catalyst, 1-3 parts of sintering agent
[0025] Example 1 Grind dry iron concentrate (grade 60), coal (grade 5000 cal or more), specially made cerium dioxide, and sodium tetraborate to 200 mesh respectively, and sieve them for later use; weigh the prepared raw materials by weight Mix 130 parts of fine iron powder, 29 parts of coal, 5 parts of catalyst, and 3 parts of sintering agent; granulate the uniformly mixed fine material into small balls with a diameter of 12 to 16 mm, dry and dehydrate, pack into cans, and heat up in a reducing atmosphere Sinter at 1000-1050 degrees Celsius for 4 hours, then cool out of the tank and serve. The product composition is: zero-valent active iron (78wt.%), carbon (14wt.%), catalyst (5wt.%).
Embodiment 2
[0026] Example 2 Grind dry iron concentrate (grade 60), coal (grade 5000 cal or more), specially made cerium dioxide, and sodium tetraborate to 200 mesh respectively, and sieve them for later use; weigh the prepared raw materials by weight Mix 140 parts of fine iron powder, 27 parts of coal, 3 parts of catalyst, and 2 parts of sintering agent; granulate the uniformly mixed fine material into small balls with a diameter of 12 to 16 mm, dry and dehydrate, pack into cans, and heat up in a reducing atmosphere Sinter at 1000-1050 degrees Celsius for 4 hours, then cool out of the tank and serve. The product composition is: zero-valent active iron (84wt.%), carbon (12wt.%), catalyst (3wt.%).
Embodiment 3
[0027] Example 3 Grind dry iron concentrate (grade 60), coal (grade 5000 cal or more), specially made cerium dioxide, and sodium tetraborate to 200 mesh respectively, and sieve them for later use; weigh the prepared raw materials by weight Mix 147 parts of fine iron powder, 25 parts of coal, 1 part of catalyst, and 1 part of sintering agent; granulate the uniformly mixed fine material into small balls with a diameter of 12 to 16 mm, dry and dehydrate, pack into cans, and heat up in a reducing atmosphere Sinter at 1000-1050 degrees Celsius for 4 hours, then cool out of the tank and serve. The product composition is: zero-valent active iron (88wt.%), carbon (10wt.%), catalyst (1wt.%).
PUM
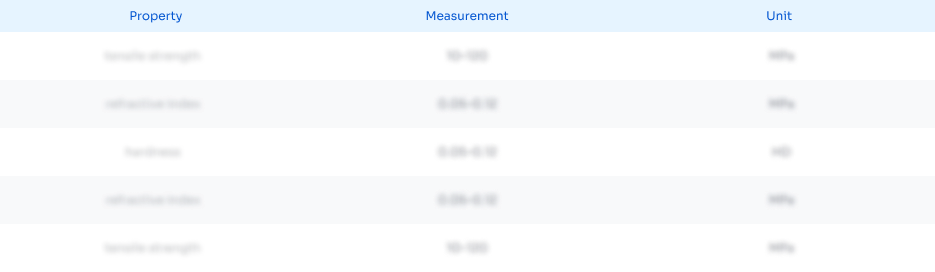
Abstract
Description
Claims
Application Information

- R&D
- Intellectual Property
- Life Sciences
- Materials
- Tech Scout
- Unparalleled Data Quality
- Higher Quality Content
- 60% Fewer Hallucinations
Browse by: Latest US Patents, China's latest patents, Technical Efficacy Thesaurus, Application Domain, Technology Topic, Popular Technical Reports.
© 2025 PatSnap. All rights reserved.Legal|Privacy policy|Modern Slavery Act Transparency Statement|Sitemap|About US| Contact US: help@patsnap.com