Method of leaching copper, cobalt and nickel from smelting alloy
An alloy, copper-cobalt technology, applied in the fields of hydrometallurgy and chemical production, can solve the problems of increasing the burden of iron removal, affecting the recovery rate of cobalt, and high price of sodium chlorate, achieving low requirements for anti-corrosion and high gas utilization rate , the effect of high reaction efficiency
- Summary
- Abstract
- Description
- Claims
- Application Information
AI Technical Summary
Problems solved by technology
Method used
Image
Examples
Embodiment 1
[0052] A method for leaching copper-cobalt-nickel from molten alloy of the present invention comprises the following steps:
[0053] The waste lithium-ion battery reduction smelting alloy containing three metals of copper, cobalt, nickel and iron impurities is melted, and the melting temperature is 1400°C, and then atomized into alloy powder by high-pressure water; the alloy powder is passed through a 100-mesh sieve, and the The particle size distribution is as shown in the following table 1, and the composition of the alloy powder is as shown in the following table 2:
[0054] Table 1: Particle size distribution of alloy powder in Example 1
[0055] Particle size / mm
Distribution rate / %
Cumulative distribution rate / %
-0.043 (-325 mesh)
73.22
73.22
-0.074~+0.043 (200~325 mesh)
16.46
89.68
-0.098~+0.074(150~200 mesh)
6.28
95.96
-0.150~+0.098(100~150 mesh)
4.04
100
[0056] Table 2: The particle ...
Embodiment 2
[0062] A method for leaching copper-cobalt-nickel from molten alloy of the present invention comprises the following steps:
[0063] The waste lithium-ion battery reduction smelting alloy containing three metals of copper, cobalt, nickel and iron impurities is melted, and the melting temperature is 1400°C, and then atomized into alloy powder by high-pressure water; the alloy powder is passed through a 100-mesh sieve, and the The particle size distribution is as shown in the above table 1 and table 2;
[0064] Take 250 g of the atomized 150-200 mesh alloy powder and add it to a stirring and aerating reaction device. In this stirring and aerating reaction device, 98% concentrated sulfuric acid is used as the leaching medium. The theoretical amount of the sum of the elements is 1.7 times, so that air or oxygen is evenly blown into the stirring shaft system of the stirring and aerating reaction device, and the shearing action of the stirring shaft system makes the blown gas evenly...
Embodiment 3
[0068] A method for leaching copper-cobalt-nickel from molten alloy of the present invention comprises the following steps:
[0069] The waste lithium-ion battery reduction smelting alloy containing three metals of copper, cobalt, nickel and iron impurities is melted, and the melting temperature is 1400°C, and then atomized into alloy powder by high-pressure water; the alloy powder is passed through a 100-mesh sieve, and the The particle size distribution is as shown in the above table 1 and table 2;
[0070] Take 250g of the atomized 200-325 mesh alloy powder and add it into a stirring and aerating reaction device. In this stirring and aerating reaction device, 98% concentrated sulfuric acid is used as the leaching medium, and the amount of acid is 2.0 times the theoretical amount of the sum of the elements, so that air or oxygen is evenly blown into the stirring shaft system of the stirring and aerating reaction device, and the shearing action of the stirring shaft system ma...
PUM
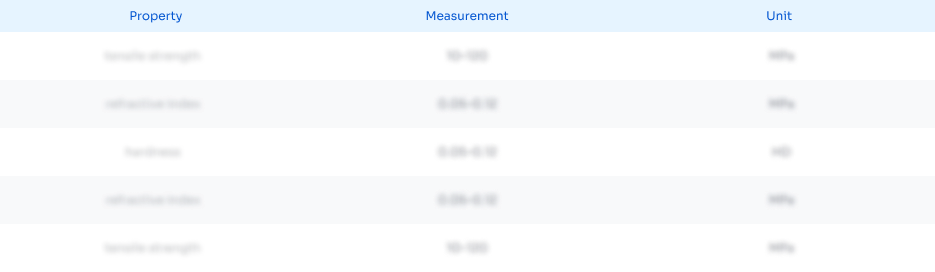
Abstract
Description
Claims
Application Information

- Generate Ideas
- Intellectual Property
- Life Sciences
- Materials
- Tech Scout
- Unparalleled Data Quality
- Higher Quality Content
- 60% Fewer Hallucinations
Browse by: Latest US Patents, China's latest patents, Technical Efficacy Thesaurus, Application Domain, Technology Topic, Popular Technical Reports.
© 2025 PatSnap. All rights reserved.Legal|Privacy policy|Modern Slavery Act Transparency Statement|Sitemap|About US| Contact US: help@patsnap.com