Production technique for improving heat exchange efficiency of heat pipe type preheater of hot air furnace
A technology of heat exchange efficiency and production process, applied in blast furnaces, blast furnace details, blast furnace parts, etc., can solve the problems of hot blast furnace exhaust gas waste heat not being effectively recovered, fuel consumption and iron costs rising, fuel costs and iron costs increase, etc. , to achieve the effect of prolonging high-efficiency applications, reducing iron costs, and increasing temperature
- Summary
- Abstract
- Description
- Claims
- Application Information
AI Technical Summary
Problems solved by technology
Method used
Examples
Embodiment Construction
[0016] The present invention will be further described below in conjunction with embodiments.
[0017] A production process for improving the heat exchange efficiency of the heat pipe preheater of a hot blast stove, the process steps are:
[0018] Step 1: Find out the reason for the decrease in heat exchange effect; the decrease in heat exchange effect has the following reasons: ① A large amount of non-condensable gas is produced in the heat pipe. After the gas is continuously accumulated, it occupies a large amount of volume in the pipe and inhibits the steam chemical industry. The circulation rate of the working fluid is reduced; ②During the circulation process of the working fluid, the exhaust valve of the heat pipe head is not closed tightly, and there is air leakage, which leads to the reduction of working quality; ③The heat pipe wall is long due to material defects. There are leaks after time runs, resulting in a reduction in work quality;
[0019] Step 2: Confirm the decrease...
PUM
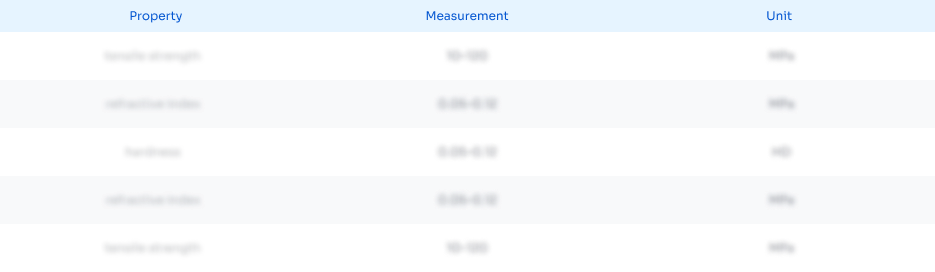
Abstract
Description
Claims
Application Information

- R&D Engineer
- R&D Manager
- IP Professional
- Industry Leading Data Capabilities
- Powerful AI technology
- Patent DNA Extraction
Browse by: Latest US Patents, China's latest patents, Technical Efficacy Thesaurus, Application Domain, Technology Topic, Popular Technical Reports.
© 2024 PatSnap. All rights reserved.Legal|Privacy policy|Modern Slavery Act Transparency Statement|Sitemap|About US| Contact US: help@patsnap.com