Lean magnetite beneficiation method capable of reducing fineness of grinding ore
A technology of lean magnetite and beneficiation method, applied in chemical instruments and methods, magnetic separation, solid separation and other directions, can solve the problems of increased beneficiation cost, drop of concentrate grade, reduction of processing capacity of ball mill, etc., so as to reduce the production cost of beneficiation , the equipment layout is simple, the effect of reducing equipment investment
- Summary
- Abstract
- Description
- Claims
- Application Information
AI Technical Summary
Problems solved by technology
Method used
Image
Examples
Embodiment 1
[0040] (1) The crushed magnetite-lean ore is finely ground to a particle size of -0.074μm, accounting for 37.60%, and subjected to coarse-grained primary magnetic separation. The magnetic field strength of the magnetic separator is 180KA / m, and the coarse-grained primary magnetic separation concentrate is obtained , the grade is 25.04%, the yield is 68.42%, and the coarse-grained first-level magnetic separation tailings are thrown away;
[0041] (2) Classify the coarse-grained primary magnetic separation concentrate with a high-frequency fine sieve, with a sieve size of 0.12mm, and separate the on-sieve product and the under-sieve product;
[0042] (3) The product on the high-frequency screen is subjected to secondary grinding, and then subjected to coarse-grained secondary magnetic separation after grinding. The magnetic field strength of the magnetic separator is 120KA / m, and the coarse-grained secondary magnetic separation concentrate is obtained with a grade of 33.25%, the...
Embodiment 2
[0048](1) The crushed magnetite-lean ore is finely ground to a particle size of -0.074μm, accounting for 35.60%, and then subjected to coarse-grained primary magnetic separation. The magnetic field strength of the magnetic separator is 200KA / m, and the coarse-grained primary magnetic separation concentrate is obtained , the grade is 38.24%, the yield is 79.32%, and the tailings of the coarse-grained first-level magnetic separation are thrown away;
[0049] (2) Classify the coarse-grained primary magnetic separation concentrate with a high-frequency fine sieve with a sieve hole size of 0.15mm, and separate the on-sieve product and the under-sieve product;
[0050] (3) The product on the high-frequency screen is subjected to secondary grinding, and then subjected to coarse-grained secondary magnetic separation after grinding. The magnetic field strength of the magnetic separator is 160KA / m, and the coarse-grained secondary magnetic separation concentrate is obtained with a grade ...
PUM
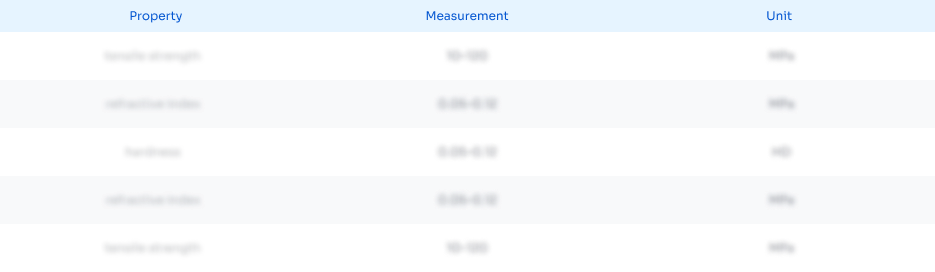
Abstract
Description
Claims
Application Information

- R&D
- Intellectual Property
- Life Sciences
- Materials
- Tech Scout
- Unparalleled Data Quality
- Higher Quality Content
- 60% Fewer Hallucinations
Browse by: Latest US Patents, China's latest patents, Technical Efficacy Thesaurus, Application Domain, Technology Topic, Popular Technical Reports.
© 2025 PatSnap. All rights reserved.Legal|Privacy policy|Modern Slavery Act Transparency Statement|Sitemap|About US| Contact US: help@patsnap.com