Method for extracting valuable metal in vanadium containing material by microwave heating preprocessing
A valuable metal, microwave heating technology, applied in the field of non-ferrous metallurgy, can solve the problems of low recovery rate of vanadium, unfavorable industrial large-scale promotion, large amount of additives, etc., achieve leaching rate and recovery rate is simple, shorten microwave reaction time, leaching The effect of high rate and recovery rate
- Summary
- Abstract
- Description
- Claims
- Application Information
AI Technical Summary
Problems solved by technology
Method used
Image
Examples
Embodiment 1
[0026] Take converter vanadium slag for grinding and screening to a particle size of ≤200 mesh, heat in a microwave heating reactor at a heating temperature of 350°C and a heating time of 10 minutes; grind the microwave-treated material to a particle size of ≤200 mesh, using 200g / L According to the liquid-solid ratio of 10:1, the leaching temperature is 90°C, the leaching time is 1h, and the stirring speed is 400rpm, the vanadium slag is leached, and then the leaching solution is obtained after liquid-solid separation, and the vanadium leaching rate is measured. The leaching rate of iron is 92.8%, the leaching rate of iron is 87.9%, the leaching rate of manganese is 97.6%, and the leaching rate of chromium is 64.2%;
[0027] Extract the leaching solution, select P204 (bis(2-ethylhexyl) phosphate) as the extractant, and sulfonated kerosene as the diluent; wherein, the number of extraction stages is selected to be 3, and the extraction conditions of each stage are: adjust water ...
Embodiment 2
[0029] Take converter vanadium slag for grinding and screening to a particle size of ≤200 mesh, and heat it in a microwave heating reactor at a heating temperature of 150°C for a heating time of 20 minutes; after microwave treatment, the material has a particle size of ≤200 mesh and uses 300g / L According to the liquid-solid ratio of 12.5:1, the leaching temperature is 85°C, the leaching time is 3h, and the stirring speed is 300rpm, the vanadium slag is leached, and then the leaching solution is obtained after liquid-solid separation, and the leaching rate of vanadium is measured. The leaching rate of iron is 97.6%, the leaching rate of manganese is 97.3%, and the leaching rate of chromium is 58.4%;
[0030] Extract the leaching solution, choose primary amine N1923 as the extractant, and sulfonated kerosene as the diluent; wherein, the number of extraction stages is selected to be 5, and the extraction conditions of each stage are: adjust the initial pH value of the aqueous phas...
Embodiment 3
[0032]Take converter vanadium slag for grinding and screening to a particle size of ≤200 mesh, heat in a microwave heating reactor at a heating temperature of 450°C and a heating time of 10 minutes; grind the microwave-treated material to a particle size of ≤200 mesh, using 250g / L According to the liquid-solid ratio of 15:1, the leaching temperature is 80°C, the leaching time is 4h, and the stirring speed is 200rpm, the vanadium slag is leached, and then the leaching solution is obtained after liquid-solid separation, and the vanadium leaching rate is measured. The leaching rate of iron was 94.2%, the leaching rate of iron was 89.3%, the leaching rate of manganese was 98.2%, and the leaching rate of chromium was 55.7%;
[0033] Extract the leaching solution, select P204 (di(2-ethylhexyl) phosphate) as the extractant, and sulfonated kerosene as the diluent; wherein, the extraction stages are selected to be grade 6, and the extraction conditions of each stage are: adjust The ini...
PUM
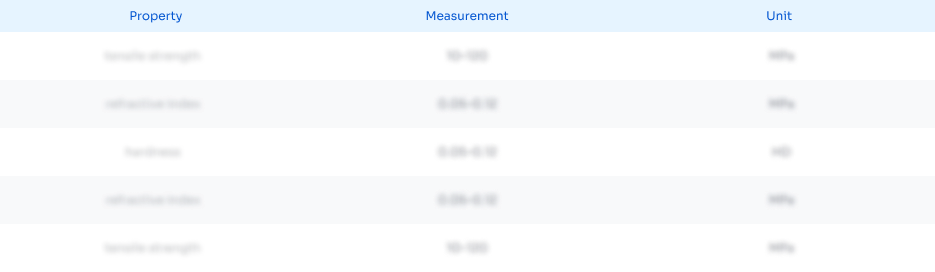
Abstract
Description
Claims
Application Information

- R&D Engineer
- R&D Manager
- IP Professional
- Industry Leading Data Capabilities
- Powerful AI technology
- Patent DNA Extraction
Browse by: Latest US Patents, China's latest patents, Technical Efficacy Thesaurus, Application Domain, Technology Topic, Popular Technical Reports.
© 2024 PatSnap. All rights reserved.Legal|Privacy policy|Modern Slavery Act Transparency Statement|Sitemap|About US| Contact US: help@patsnap.com