Corrosion resistant modified calcium carbonate with excellent overall performances and preparation method thereof
A comprehensive performance, calcium carbonate technology, applied in chemical instruments and methods, dyed low molecular organic compound treatment, dyed high molecular organic compound treatment and other directions, can solve the problem of poor direct application effect, uneven dispersion of high polymer, easy formation Aggregate and other problems, to achieve the effect of improving hardness, enhancing corrosion resistance, and good suspension stability
- Summary
- Abstract
- Description
- Claims
- Application Information
AI Technical Summary
Problems solved by technology
Method used
Examples
Embodiment Construction
[0012] specific implementation plan
[0013] The present invention will be described in detail below through specific examples.
[0014] A modified calcium carbonate with good comprehensive performance and good corrosion resistance and its preparation method is prepared from the following raw materials in parts by weight (kg): calcium carbonate 150, sodium oleate 46, sodium dodecylbenzenesulfonate 0.5, carbonic acid Sodium hydrogen 2 styrene 6, potassium persulfate 0.04, fumed silica 4, organic bentonite 3, trioctyl trimellitate 1, glass powder 4, polytetrafluoroethylene powder 4, appropriate amount of deionized water;
[0015] A kind of modified calcium carbonate with good comprehensive performance and good corrosion resistance and preparation method thereof of the present invention are made by the following concrete steps:
[0016] (1) Dissolve sodium oleate and deionized water to make a 1% aqueous solution of sodium oleate, stir electrically for 10 minutes and raise the te...
PUM
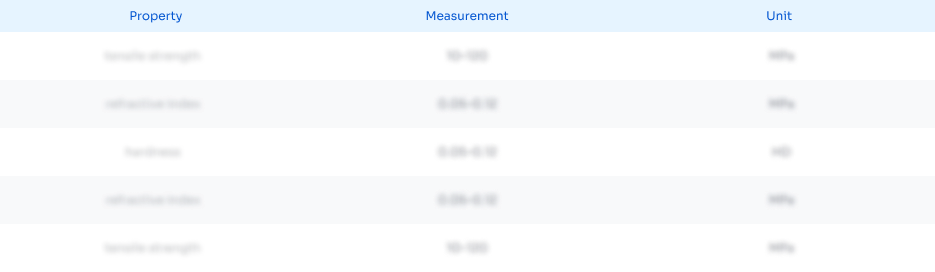
Abstract
Description
Claims
Application Information

- R&D
- Intellectual Property
- Life Sciences
- Materials
- Tech Scout
- Unparalleled Data Quality
- Higher Quality Content
- 60% Fewer Hallucinations
Browse by: Latest US Patents, China's latest patents, Technical Efficacy Thesaurus, Application Domain, Technology Topic, Popular Technical Reports.
© 2025 PatSnap. All rights reserved.Legal|Privacy policy|Modern Slavery Act Transparency Statement|Sitemap|About US| Contact US: help@patsnap.com