Vanadium-titanium enamel glaze and preparation method thereof
An enamel glaze, vanadium-titanium technology, applied in the field of enamel materials, can solve the problems of insufficient glossiness of fired enamel glaze, insufficient acid and alkali resistance, high cost, etc., to improve hydrogen corrosion resistance and scale explosion resistance , The effect of improving the hydrogen storage capacity of steel
- Summary
- Abstract
- Description
- Claims
- Application Information
AI Technical Summary
Problems solved by technology
Method used
Image
Examples
preparation example Construction
[0030] The preparation method of vanadium-titanium enamel glaze comprises the following steps:
[0031] a. Pulverize vanadium-titanium-magnetite titanium tailings or vanadium-titanium superficial ore to a particle size of 60-80 mesh, calcinate at a temperature of 550-600°C for 40-60 minutes, quickly pour into cold water for quenching, and dry to obtain Pretreated vanadium-titanium magnetite tailings or vanadium-titanium superficial ore;
[0032]b. 22-28 parts of pretreated vanadium-titanium magnetite titanium tailings or vanadium-titanium superficial ore, 20-22 parts of feldspar powder, 5-8 parts of quartz sand, 24-26 parts of borax, and 1.5 parts of sodium nitrate ~2 parts, lithium carbonate 3.5~5.5 parts, fluorite powder 5~7 parts, sodium fluorosilicate 0.1~0.3 parts, cryolite 3~5 parts, limestone 2~4 parts, cobalt nitrate 3~4 parts, nickel nitrate 1 ~2 parts, 2~3 parts of sodium vanadate and 1~2 parts of antimony oxide are mixed evenly, and the mixing uniformity is ≥98%; ...
Embodiment 1
[0041] Calcined at 550°C for 40 minutes according to weight ratio, poured into cold water, quenched, dried and pretreated, 28 parts of vanadium-titanium magnetite titanium tailings, 22 parts of feldspar powder, 8 parts of quartz sand, 26 parts of borax, sodium nitrate 1.5 parts, 3.5 parts of lithium carbonate, 5 parts of fluorite powder, 0.3 parts of sodium fluorosilicate, 5 parts of cryolite, 3 parts of limestone, 3.5 parts of cobalt nitrate, 1 part of nickel nitrate, 2 parts of sodium vanadate, 1 part of antimony oxide mixed Uniformity, mixing uniformity ≥ 98%. Transfer the mixed material into an electric furnace or a kiln and heat it to 850°C for 1 hour, then heat it to 1200°C and hold it for 1.5 hours to obtain a uniform molten enamel. The fused enamel is drawn without knots, poured into cold water, quenched and crushed, taken out and dried. Take 100 parts of enamel, 0.5 part of borax, 0.2 part of sodium nitrite, 7 parts of clay, 0.5 part of bentonite, and 1 part of magne...
Embodiment 2
[0044] Calcined at 550°C for 40 minutes according to the weight ratio, poured into cold water, quenched and dried pretreated vanadium-titanium magnetite titanium tailings 28 parts, feldspar powder 22 parts, quartz sand 5 parts, borax 26 parts, sodium nitrate 1.5 parts, 5.5 parts of lithium carbonate, 0.3 parts of sodium fluorosilicate, 5 parts of fluorite powder, 4.5 parts of cryolite, 3 parts of limestone, 3.5 parts of cobalt nitrate, 1 part of nickel nitrate, 2 parts of antimony oxide. ≥98%. Transfer the mixed material into an electric furnace or kiln and heat it to 800-850°C for 1 hour, then heat it to 1200°C and hold it for 1.5 hours to obtain a uniform molten enamel. The fused enamel is drawn without knots, poured into cold water, quenched and crushed, taken out and dried. Take 100 parts of enamel, 1 part of borax, 0.2 part of sodium nitrite, 5 parts of clay, 0.5 part of bentonite, and 1 part of magnesium sulfate and pulverize to a particle size of -200 mesh ≥ 98% to pre...
PUM
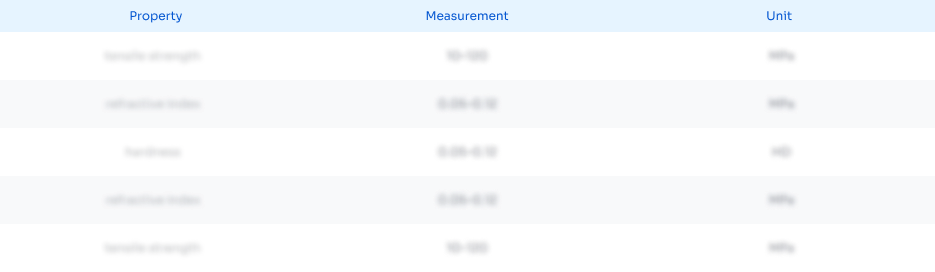
Abstract
Description
Claims
Application Information

- R&D
- Intellectual Property
- Life Sciences
- Materials
- Tech Scout
- Unparalleled Data Quality
- Higher Quality Content
- 60% Fewer Hallucinations
Browse by: Latest US Patents, China's latest patents, Technical Efficacy Thesaurus, Application Domain, Technology Topic, Popular Technical Reports.
© 2025 PatSnap. All rights reserved.Legal|Privacy policy|Modern Slavery Act Transparency Statement|Sitemap|About US| Contact US: help@patsnap.com