Reproducible paper-plastic compound bag and preparation method thereof
A composite bag, recycled paper technology, applied in the field of paper-plastic bag manufacturing, can solve the problems of poor degradation performance, poor regeneration ability, increase, etc., and achieve good biodegradability and photodegradability, excellent regeneration performance, and easy-to-obtain raw materials. Effect
- Summary
- Abstract
- Description
- Claims
- Application Information
AI Technical Summary
Problems solved by technology
Method used
Examples
preparation example Construction
[0025] The present invention also provides a preparation method of a recyclable paper-plastic composite bag, the method comprising:
[0026] (1) Polypropylene, polyethylene, starch, polylactic acid, plant fiber, polyhydroxyalkanoate, polycaprolactone, poly-β-hydroxybutyric acid, epoxy resin, wood flour, aluminum sulfate, lactose, o-phthalic acid Dibutyl diformate and sodium stearate are mixed and extruded to make a film;
[0027] (2) Cutting, drawing and weaving the film into a plastic layer, and then sticking the plastic layer on the surface of the paper layer through an adhesive to make a composite paper; or heating the film And coated on the surface of the paper layer to form a plastic layer to make composite paper;
[0028] (3) Processing the composite paper machine into a recyclable paper-plastic composite bag.
[0029] In the above preparation method, the weight-average molecular weight of polyethylene can be selected in a wide range, in order to make the regeneration ...
Embodiment 1
[0042] (1) At 25°C, polypropylene, polyethylene, wheat starch, polylactic acid, rice husk fiber, hydroxybutyric acid caproic acid copolyester, polycaprolactone, polyβ-hydroxybutyric acid, epoxy resin, Wood flour, aluminum sulfate, lactose, dibutyl phthalate and sodium stearate (the mass ratio of each raw material is 100:33:18:27:18:22:18:16:8:7:6: 3:4:2) mixed for 2 hours, and extruded at 240°C to make a film;
[0043] (2) Heating the film to 230°C and coating it on the surface of the paper layer to form a plastic layer to make a composite paper (the thickness ratio of the paper layer to the plastic layer is 1:1);
[0044] (3) Process the above-mentioned composite paper machine into a recyclable paper-plastic composite bag A1.
Embodiment 2
[0046] (1) At 25°C, polypropylene, polyethylene, potato starch, polylactic acid, bamboo fiber, hydroxybutyric acid caproic acid copolyester, polycaprolactone, polyβ-hydroxybutyric acid, epoxy resin, Wood flour, aluminum sulfate, lactose, dibutyl phthalate and sodium stearate (the mass ratio of each raw material is 100:30:18:27:18:22:18:16:8:7:6: 1:2:1) mixed for 2 hours, and extruded at 240°C to make a film;
[0047] (2) heating the film to 230° C. and coating it on the surface of the paper layer to form a plastic layer to make a composite paper (the thickness ratio of the paper layer to the plastic layer is 1.1:1);
[0048] (3) Process the above-mentioned composite paper machine into a recyclable paper-plastic composite bag A2.
PUM
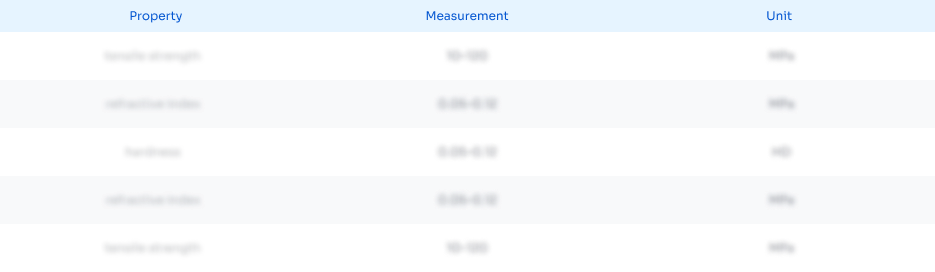
Abstract
Description
Claims
Application Information

- R&D
- Intellectual Property
- Life Sciences
- Materials
- Tech Scout
- Unparalleled Data Quality
- Higher Quality Content
- 60% Fewer Hallucinations
Browse by: Latest US Patents, China's latest patents, Technical Efficacy Thesaurus, Application Domain, Technology Topic, Popular Technical Reports.
© 2025 PatSnap. All rights reserved.Legal|Privacy policy|Modern Slavery Act Transparency Statement|Sitemap|About US| Contact US: help@patsnap.com