Method for preparing nano-particle dispersed ultrafine grain metal matrix nano composite
A nano-composite material and nano-particle technology, which is applied in the field of preparation of ultra-fine-grained metal-based nano-composite materials, can solve the limitation of large plastic deformation process, multiple rolling and extrusion process, extremely insufficient metal flow, and multi-pass processing. Small quantity and other problems, to achieve the effect of improving casting defects, improving casting defects, and improving yield
- Summary
- Abstract
- Description
- Claims
- Application Information
AI Technical Summary
Problems solved by technology
Method used
Image
Examples
Embodiment 1、1
[0031] Preparation of embodiment 1, 1.0wt% n-SiCp / pure Mg composite material
[0032] Pure Mg (99.93%) is used as the matrix, and 50nm β-SiC particles are used as the reinforcement. After the magnesium melt is completely melted at 700°C, keep it warm for 1 hour, turn on the mechanical stirring device, add nano-SiC particles preheated at 500°C into the melt (molten magnesium metal liquid), and at the same time, treat the melt with high-energy ultrasonic for 15 minutes. Then, the melt was raised to 725°C for casting. The preheating temperature of the metal mold is 350°C, and the melting process uses CO 2 +SF 6 Mixed gas as shielding gas. A reciprocating extrusion billet with geometric dimensions of Φ30mm×42mm was cut out from the ingot, and solution treated at 413°C for 24h. After the heat treatment is completed, a reciprocating extrusion die is used to carry out 8 passes of reciprocating extrusion at 350°C for large plastic deformation. figure 2 a shows n-SiCp nanoparti...
Embodiment 2、0
[0033] Example 2, Preparation of 0.5wt% n-SiCp / AZ91D magnesium-based composite material
[0034] AZ91D cast magnesium alloy is used as the matrix, and 40nm β-SiC particles are used as the reinforcement. After the magnesium alloy melt is completely melted at 630°C, keep it warm for 1 hour, turn on the mechanical stirring device, add nano-SiC particles preheated at 500°C into the magnesium alloy melt (melting AZ91D magnesium alloy liquid), and at the same time, high-energy ultrasonic treatment Melt 15min. Then, the melt is raised to 650-660°C for casting. The preheating temperature of the metal mold is 300°C, and the melting process uses CO 2 +SF 6 Mixed gas as shielding gas. A repeatedly upsetting billet with a geometric size of 100mm×100mm×20mm was cut from the ingot, and was subjected to solution heat treatment at 413°C for 24h. After the heat treatment is completed, use the repeated upsetting mold to perform 2 times of repeated upsetting and large plastic deformation ...
Embodiment 3、15
[0035] Example 3, Preparation of 1.5wt% n-SiCp / AZ91D magnesium-based composite material
[0036] AZ91D cast magnesium alloy is used as the matrix, and 40nm β-SiC particles are used as the reinforcement. After the magnesium alloy melt is completely melted at 630°C, keep it warm for 1 hour, turn on the mechanical stirring device, add nano-SiC particles preheated at 500°C into the magnesium alloy melt (melting AZ91D magnesium alloy liquid), and at the same time, high-energy ultrasonic treatment Melt 15min. Then, the temperature of the melt is raised to 650-660° C. for casting. The preheating temperature of the metal mold is 300°C, and the melting process uses CO 2 +SF 6 Mixed gas as shielding gas. A repeatedly upsetting billet with a geometric size of 100mm×100mm×20mm was cut from the ingot, and was subjected to solution heat treatment at 413°C for 24h. After the heat treatment is completed, use the cyclic closed die forging die to carry out 4 passes of cyclic closed die f...
PUM
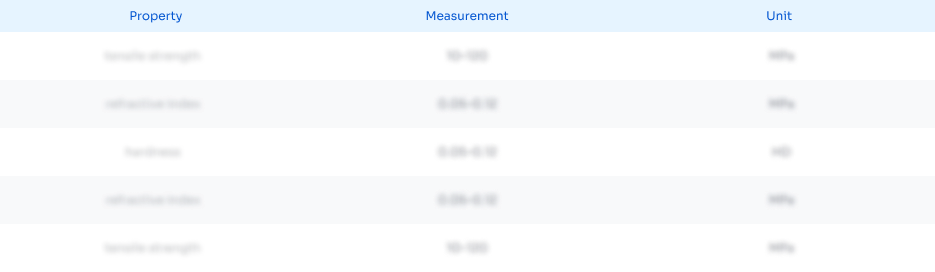
Abstract
Description
Claims
Application Information

- R&D Engineer
- R&D Manager
- IP Professional
- Industry Leading Data Capabilities
- Powerful AI technology
- Patent DNA Extraction
Browse by: Latest US Patents, China's latest patents, Technical Efficacy Thesaurus, Application Domain, Technology Topic, Popular Technical Reports.
© 2024 PatSnap. All rights reserved.Legal|Privacy policy|Modern Slavery Act Transparency Statement|Sitemap|About US| Contact US: help@patsnap.com