High isotactic polypropylene alloy material and preparation method thereof
An alloy material and polyolefin technology, which is used in the preparation of regular polyolefin alloy materials and the field of polybutene polypropylene alloy materials, can solve the problems of inability to achieve results, reduced catalytic activity, and uneven distribution of copolymers.
- Summary
- Abstract
- Description
- Claims
- Application Information
AI Technical Summary
Problems solved by technology
Method used
Image
Examples
Embodiment 1
[0070] 1L full-sealed magnetic stirring stainless steel pressure polymerization kettle, pumped and replaced with high-purity nitrogen for several times, then metered and added triethylaluminum (Al), 100mL of hexane, and external electron donor diphenyl dimethoxide into the reaction kettle Silane (Si) and MgCl 2 Loaded TiCl 4 Catalyst (Ti content 2.5wt.%) 0.25g, add propylene 0.06Kg, wherein Al / Ti=50 (molar ratio), Al / Si=10 (molar ratio). Stir and polymerize at 0°C for 5 minutes, then raise the temperature and depressurize to evacuate propylene and hexane, flush it into a new reactor with inert gas, replace the inert gas with propylene to a pressure of 0.1MPa, and then add 0.01MPa of hydrogen at 30°C React for 6 minutes, then evacuate propylene and hydrogen, add 0.2Kg butene-1, react at 60°C for 1 hour, evacuate butene-1, further feed propylene to a pressure of 0.2MPa, maintain 6 minutes, then evacuate propylene, add 0.2 Kg of butene-1 and 0.01MPa hydrogen were reacted for 1 ...
Embodiment 2
[0072] 1L fully-closed magnetic stirring gas-phase stainless steel pressure polymerization kettle, pumped and replaced with high-purity nitrogen for several times, then metered triethylaluminum (Al), external electron donor cyclohexyltrimethoxysilane (Si) and MgI 2 Loaded TiCl 4 Catalyst (Ti content 2.5wt.%) 0.25g, add propylene 0.05Kg, hydrogen 0.02Mpa, wherein Al / Ti=80 (molar ratio), Al / Si=20 (molar ratio). Stir and polymerize at 0°C for 5 minutes, then heat up and evacuate propylene and hydrogen under reduced pressure, add 0.2Kg of butene-1, react at 55°C for 0.5h, empty butene-1, and feed 0.2MPa of propylene and 0.02 MPa of hydrogen was reacted at 60°C for 10 minutes, then the propylene and hydrogen were evacuated, 0.2Kg of butene-1 was added, and the reaction was carried out at 55°C for 0.5h, and the cycle was repeated three times. After the drying was terminated, 380g of powdered polymer was directly obtained. The properties of the alloy are shown in Table 1.
Embodiment 3
[0074] 10L fully-closed loop reactor, pumped out and replaced with high-purity nitrogen several times, then metered 150ml of heptane, triethylaluminum (AlEt3), and external electron donor diphenyldimethoxysilane into the reactor (Si) and SiO 2 Load VlCl 3 Catalyst (V content 3.3wt.%) 1.0g, add propylene 0.05Kg, wherein Al / V=50 (molar ratio), Al / Si=20 (molar ratio), 0 ℃ of stirring polymerization 1min, then heat up and depressurize discharge Empty propylene and hexane, feed 0.3MPa propylene and 0.03MPa hydrogen into the reactor, react at 60°C for 10 minutes, then empty the propylene and hydrogen, add 0.5Kg of butene-1, react at 35°C for 0.6h, and empty Butene-1, further feed propylene and hydrogen to a pressure of 0.2MPa, maintain for 10min, then empty the propylene, add 0.5Kg of butene-1, react for 0.5h, and cycle like this 4 times, and obtain powder directly after drying Polymer 2.77Kg. The properties of polybutene alloy are shown in Table 1.
PUM
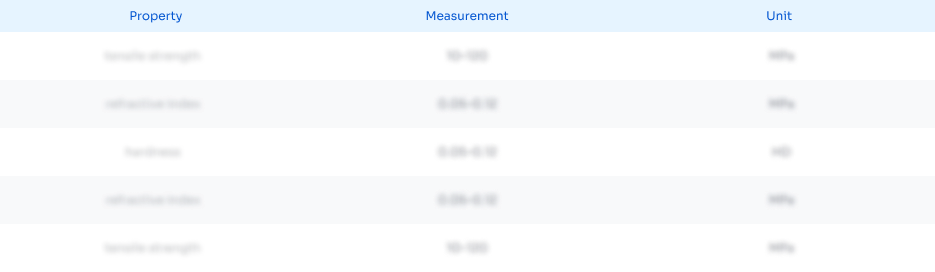
Abstract
Description
Claims
Application Information

- R&D
- Intellectual Property
- Life Sciences
- Materials
- Tech Scout
- Unparalleled Data Quality
- Higher Quality Content
- 60% Fewer Hallucinations
Browse by: Latest US Patents, China's latest patents, Technical Efficacy Thesaurus, Application Domain, Technology Topic, Popular Technical Reports.
© 2025 PatSnap. All rights reserved.Legal|Privacy policy|Modern Slavery Act Transparency Statement|Sitemap|About US| Contact US: help@patsnap.com