Rust-resistant hot rolled ribbed bar and production process thereof
A hot-rolled ribbed steel bar and production process technology, applied in the field of anti-corrosion hot-rolled ribbed steel bar and its production process, can solve the problem of high cost of steel bar alloy, unreasonable control of rolling temperature, serious corrosion rate and degree of steel bar corrosion, etc. Problems, achieve the effect of reducing alloy cost, ensuring anti-corrosion performance, and reducing cooling intensity
- Summary
- Abstract
- Description
- Claims
- Application Information
AI Technical Summary
Problems solved by technology
Method used
Examples
Embodiment 1
[0018] An anti-corrosion hot-rolled ribbed steel bar, characterized in that: the chemical composition of the ribbed steel bar includes C, Si, Mn, V, Cr, P, S, wherein the weight percentage of the chemical composition is: C: 0.23% , Si: 0.50%, Mn: 1.00%, V: 0.015%, Cr: 0.20%, P≤0.042%, S≤0.040%, and the rest are iron and unavoidable impurities.
[0019] The production process of the anti-corrosion hot-rolled ribbed steel bar in Example 1 includes the following steps: (1) Preparation of blast furnace molten iron, in weight percentage, blast furnace molten iron includes the following chemical components: P≤0.120%, S≤0.070%, Si ≤1.20%; (2) Top-blown converter smelting, in terms of weight percentage, the chemical composition of the molten iron entering the converter is controlled at P≤0.120%, S≤0.060%, Si: 0.50%, and the molten steel after converter smelting and deoxidation alloying goes out The steel temperature is 1630°C, and the chemical composition of the molten steel after tap...
Embodiment 2
[0021] An anti-corrosion hot-rolled ribbed steel bar, characterized in that: the chemical composition of the ribbed steel bar includes C, Si, Mn, V, Cr, P, S, wherein the weight percentage of the chemical composition is: C: 0.20% , Si: 0.40%, Mn: 0.90%, V: 0.010%, Cr: 0.15%, P≤0.042%, S≤0.040%, and the rest are iron and unavoidable impurities.
[0022] The production process of the anti-corrosion hot-rolled ribbed steel bar in Example 2 includes the following steps: (1) Preparation of blast furnace molten iron, in weight percentage, blast furnace molten iron includes the following chemical components: P≤0.120%, S≤0.070%, Si ≤1.20%; (2) Top-blown converter smelting, in terms of weight percentage, the chemical composition of the molten iron entering the converter is controlled at P≤0.120%, S≤0.060%, Si: 0.20%, and the molten steel after converter smelting and deoxidation alloying goes out The steel temperature is 1600°C, and the chemical composition of the molten steel after tap...
Embodiment 3
[0024] An anti-corrosion hot-rolled ribbed steel bar is characterized in that: the chemical composition of the ribbed steel bar includes C, Si, Mn, V, Cr, P, S, wherein the weight percentage of the chemical composition is: C: 0.25% , Si: 0.60%, Mn: 1.10%, V: 0.020%, Cr: 0.25%, P≤0.042%, S≤0.040%, and the rest are iron and unavoidable impurities.
[0025] The production process of the anti-corrosion hot-rolled ribbed steel bar in Example 3 includes the following steps: (1) Preparation of blast furnace molten iron, in weight percentage, blast furnace molten iron includes the following chemical components: P≤0.120%, S≤0.070%, Si ≤1.20%; (2) Top-blown converter smelting, in terms of weight percentage, the chemical composition of the molten iron entering the converter is controlled at P≤0.120%, S≤0.060%, Si: 0.80%, and the molten steel after converter smelting and deoxidation alloying goes out The steel temperature is 1660°C, and the chemical composition of the molten steel after t...
PUM
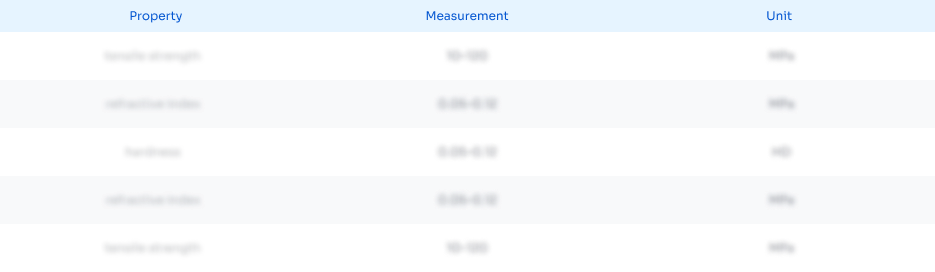
Abstract
Description
Claims
Application Information

- R&D
- Intellectual Property
- Life Sciences
- Materials
- Tech Scout
- Unparalleled Data Quality
- Higher Quality Content
- 60% Fewer Hallucinations
Browse by: Latest US Patents, China's latest patents, Technical Efficacy Thesaurus, Application Domain, Technology Topic, Popular Technical Reports.
© 2025 PatSnap. All rights reserved.Legal|Privacy policy|Modern Slavery Act Transparency Statement|Sitemap|About US| Contact US: help@patsnap.com