Large forged alloy steel backup roll sleeve and manufacturing method thereof
A technology of alloy steel and back-up rolls, which is applied in the field of roll sleeves and its manufacture, can solve the problems of limited use and inability to meet the requirements of large-scale back-up rolls, and achieve comprehensive performance improvement, good heat treatment process performance, and prevention of temper brittleness Effect
- Summary
- Abstract
- Description
- Claims
- Application Information
AI Technical Summary
Problems solved by technology
Method used
Image
Examples
Embodiment 1
[0032] A large-scale forged alloy steel back-up roll sleeve, the design target of the chemical composition and mass percentage content of the roll sleeve is: C 0.45-0.55%, Si 0.50-0.70%, Mn 0.60-0.80%, Cr 4.80- 5.80%, Mo 0.80~1.20%, V0.20~0.30%, Ni≤0.4%, P≤0.02%, S≤0.02%, and the rest are Fe and unavoidable impurities.
[0033] The manufacturing method of described roller sleeve comprises the following process steps:
[0034] A. Refining steel ingots
[0035] The required raw materials are initially smelted in an electric arc furnace. After the smelting is completed, the molten steel is placed in an LF refining furnace to start refining the molten steel. The LF refining temperature is 1600-1800 °C and the refining time is 6 hours. After the molten steel is refined, it is poured into steel ingots in the form of die casting.
[0036] The chemical composition of the steel ingot was analyzed, and the chemical composition and mass percentage of the steel ingot were: C 0.51%, Si 0...
Embodiment 2
[0045] The process steps in embodiment 2 are the same as the process steps in embodiment 1, and the difference with embodiment 1 is: the design target of the chemical composition and mass percentage content of the large forged alloy steel backup roll sleeve in the present embodiment is :
[0046] C 0.40~0.50%, Si 0.50~0.70%, Mn 0.60~0.80%, Cr 4.80~5.80%, Mo0.80~1.20%, V 0.20~0.30%, Ni≤0.4%, P≤0.02%, S≤0.02 %, the rest is Fe and unavoidable impurities.
[0047] After analyzing the chemical composition of the steel ingot, the chemical composition and its mass percentage in the steel ingot are: C0.45%, Si 0.65%, Mn 0.7%, Cr 4.8%, Mo 1.2%, V 0.25%, Ni 0.2% , P 0.014%, S 0.009%, and the rest are Fe and unavoidable impurities.
[0048] The quenching temperature in step D is 1030°C, and the quenching time is 0.6h; the primary tempering temperature is 550°C, and the primary tempering holding time is 10h; the secondary tempering temperature is 530°C, and the secondary tempering holdi...
Embodiment 3
[0050] The process step in embodiment 3 is the same as the process step in embodiment 1, and the difference with embodiment 1 is: the design target of the chemical composition and mass percentage content of the large forged alloy steel backup roll sleeve in the present embodiment is :
[0051] C 0.40~0.50%, Si 0.50~0.70%, Mn 0.60~0.80%, Cr 4.8~5.80%, Mo 0.20~0.6%, V 0.08~0.12%, Ni≤0.4%, P≤0.02%, S≤0.02% , and the rest are Fe and unavoidable impurities.
[0052] After analyzing the chemical composition of the steel ingot, the chemical composition and mass percentage of the steel ingot are: C 0.48%, Si 0.57%, Mn 0.62%, Cr 4.8%, Mo 0.3%, V 0.09%, Ni 0.4% , P 0.01%, S 0.009%, and the rest are Fe and unavoidable impurities.
[0053] The quenching temperature in step D is 980°C, and the quenching time is 0.4h; the primary tempering temperature is 480°C, and the primary tempering holding time is 12h; the secondary tempering temperature is 500°C, and the secondary tempering holding ...
PUM
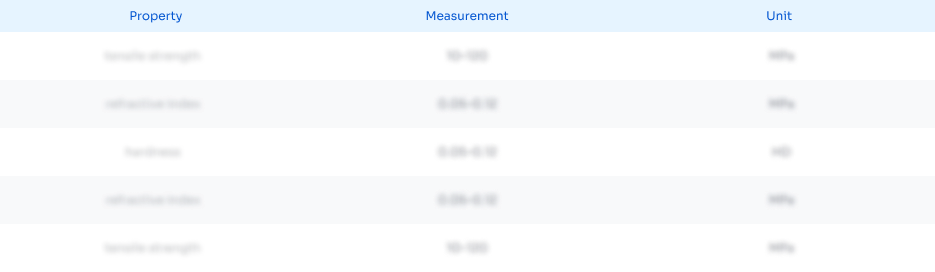
Abstract
Description
Claims
Application Information

- Generate Ideas
- Intellectual Property
- Life Sciences
- Materials
- Tech Scout
- Unparalleled Data Quality
- Higher Quality Content
- 60% Fewer Hallucinations
Browse by: Latest US Patents, China's latest patents, Technical Efficacy Thesaurus, Application Domain, Technology Topic, Popular Technical Reports.
© 2025 PatSnap. All rights reserved.Legal|Privacy policy|Modern Slavery Act Transparency Statement|Sitemap|About US| Contact US: help@patsnap.com