Complete-machine static rigidity detection control system for numerical control machine tool
A technology of detection control system and numerical control machine tool, which is applied in the field of numerical control machine tool, can solve the problems of no test system or instrument device, scattered test system, and inability to apply in large quantities, so as to improve detection efficiency and precision, realize automation and diversify functions Effect
- Summary
- Abstract
- Description
- Claims
- Application Information
AI Technical Summary
Problems solved by technology
Method used
Image
Examples
Embodiment Construction
[0015] In order to further understand the invention content, characteristics and effects of the present invention, the following examples are given, and detailed descriptions are as follows in conjunction with the accompanying drawings:
[0016] See figure 1 , figure 2 and image 3 , the present invention is used in the static stiffness detection and control system of CNC machine tools, mainly composed of a data acquisition system, a motion control system and a three-degree-of-freedom loading execution unit; the three-degree-of-freedom loading execution unit is mainly composed of the data acquisition system and the control The system consists of pressure sensor, eddy current displacement sensor 2, 3 and 4, NI data acquisition system card, NI motion control card and PC. The three-degree-of-freedom loading execution unit is mainly composed of servo valves, hydraulic cylinders 9, 10 and 11, disc springs, probes and a test rod installed on the main shaft 1.
[0017] There is a...
PUM
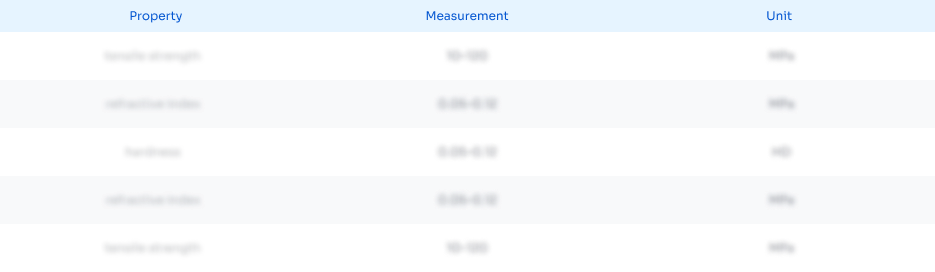
Abstract
Description
Claims
Application Information

- R&D
- Intellectual Property
- Life Sciences
- Materials
- Tech Scout
- Unparalleled Data Quality
- Higher Quality Content
- 60% Fewer Hallucinations
Browse by: Latest US Patents, China's latest patents, Technical Efficacy Thesaurus, Application Domain, Technology Topic, Popular Technical Reports.
© 2025 PatSnap. All rights reserved.Legal|Privacy policy|Modern Slavery Act Transparency Statement|Sitemap|About US| Contact US: help@patsnap.com