Two-component polyurethane resin for metal packaging tanks, and preparation method thereof
A two-component polyurethane and metal packaging can technology, applied in the direction of polyurea/polyurethane adhesives, adhesive types, adhesives, etc., can solve the problems of complex preparation process, unstable product quality, high production cost, etc., and achieve raw materials Easy to obtain, simple and reliable preparation method, and stable product quality
- Summary
- Abstract
- Description
- Claims
- Application Information
AI Technical Summary
Problems solved by technology
Method used
Examples
Embodiment 1
[0025] Add 127.32 g of isophthalic acid, 112.0 Kg of adipic acid, 45.7 Kg of ethylene glycol, and 115.0 Kg of neopentyl glycol into the reaction kettle, add 0.2 Kg of tetrabutyl titanate, and gradually raise the temperature to 240 ° C, during which the fractionation tower is controlled The top temperature is 100-110°C, when the amount of distilled water is 55.19Kg, the top temperature drops to 60°C, and the acid value is 25.73mgKOH / g for sampling analysis. From 0.02 to 0.08MPa, increase by 0.02MPa every hour, and then start high vacuum 0.099 to 0.1MPa. After 5 hours, the measured hydroxyl value is 8.71mgKOH / g, and the acid value is 0.76mgKOH / g.
[0026] Remove the vacuum from the reactor, lower the temperature to 150°C, add 370Kg of ethyl acetate to it for dilution, when it drops to 75°C, add 50.0Kg of E21 to continue to dissolve and dilute, and add 1.48Kg of γ-shrink Glyceryl ether oxypropyl trimethoxysilane, stirred evenly and discharged, used as the main agent, used in conj...
Embodiment 2
[0028] Add 302.95Kg dimethyl terephthalate, 96.88Kg ethylene glycol, 97.53Kg neopentyl glycol, 73.63Kg 1,6-hexanediol into the reaction kettle, add 0.2Kg tetrabutyl titanate, and blow in nitrogen , Gradually raise the temperature to 200°C, during which the top temperature of the fractionation tower is controlled at 60-70°C, when the amount of distilled methanol is 99.84Kg, the top temperature drops to 40°C, and then 92.35Kg of phthalic anhydride and 136.75Kg of adipic acid are added to the reactor During the process, the temperature was gradually raised to 230°C. During this period, the top temperature of the fractionation tower was controlled at 100-110°C. When the amount of distilled water was 44.93Kg, the top temperature dropped to 60°C. The acid value of the sampling analysis was 23.90 mgKOH / g, and the feeding of nitrogen was stopped. Keep it at 230°C, start vacuuming gradually, the vacuum degree is from 0.02 to 0.08MPa, increase by 0.02MPa every 1 hour, and then start to p...
Embodiment 3
[0031]Add 168.37Kg dimethyl terephthalate, 49.53Kg ethylene glycol, 82.95Kg neopentyl glycol, and 42.27Kg diethylene glycol into the reaction kettle, add 0.2Kg tetrabutyl titanate, and blow in nitrogen , Gradually raise the temperature to 200°C, during which the top temperature of the fractionation tower is controlled at 60-70°C. When the amount of distilled methanol is 55.49Kg, the top temperature drops to 40°C, and then 86.4Kg of isophthalic acid and 70.16Kg of sebacic acid are added to the reactor During the process, the temperature was gradually raised to 230°C. During this period, the top temperature of the fractionation tower was controlled at 100-110°C. When the amount of distilled water was 31.21Kg, the top temperature dropped to 60°C. The acid value of the sampling analysis was 21.14mgKOH / g, and the feeding of nitrogen was stopped. Keep it at 230°C, start vacuuming step by step, the vacuum degree is from 0.02 to 0.08MPa, increase by 0.02MPa every 1 hour, and then start...
PUM
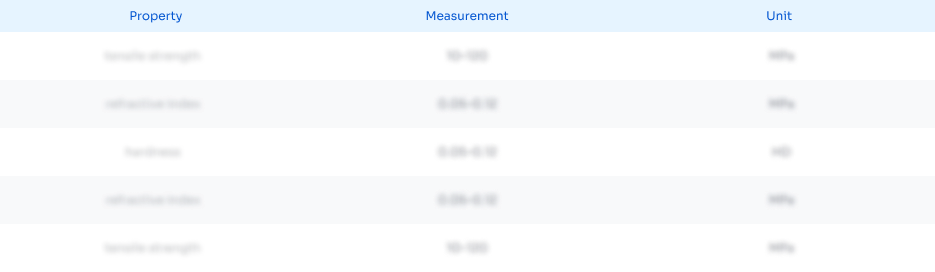
Abstract
Description
Claims
Application Information

- R&D Engineer
- R&D Manager
- IP Professional
- Industry Leading Data Capabilities
- Powerful AI technology
- Patent DNA Extraction
Browse by: Latest US Patents, China's latest patents, Technical Efficacy Thesaurus, Application Domain, Technology Topic, Popular Technical Reports.
© 2024 PatSnap. All rights reserved.Legal|Privacy policy|Modern Slavery Act Transparency Statement|Sitemap|About US| Contact US: help@patsnap.com