Method for restraining macrosegregation of large steel ingot
A technology of macro segregation and steel ingots, which is applied in the field of casting of large steel ingots, can solve the problems that the macro segregation of large steel ingots has not been effectively solved, the application is difficult, and cold shut defects, etc. Improved effect
- Summary
- Abstract
- Description
- Claims
- Application Information
AI Technical Summary
Problems solved by technology
Method used
Image
Examples
Embodiment 1
[0032] In this embodiment, the material of the ingot mold is gray cast iron HT250, the preheating temperature of the ingot mold is 100°C, a heating riser is used, the taper of the heating riser is 10%, the height-diameter ratio of the steel ingot is 1.2, and the total weight of the steel ingot is 1.2. It is 438 tons, and the pouring temperature is 1560 ℃.
[0033] Process 1: 1) Using three packs of continuous vacuum casting; 2) Using heating risers, the heating temperature is 1530 ℃ (higher than the liquidus temperature), the heating time of heating risers is 10 hours, and covering agent and heating agent are used at the same time 3) The carbon content of the first ladle of molten steel is 0.51%, the carbon content of the second ladle of molten steel is 0.45%, the carbon content of the third ladle of molten steel is 0.37%, and the continuous pouring time is 5200 seconds; Both weigh 150 tons.
[0034] Process two: steps 1), 3) and 4) are exactly the same as process one, but th...
Embodiment 2
[0039] Compared with Example 1, the heating process of the 438-ton steel ingot is the same in this implementation, but the composition of the last ladle of molten steel in the continuous vacuum casting process of multi-cladding is different.
[0040] Process five: 1) Using three-pack continuous vacuum casting; 2) Using a heating riser, the heating temperature is 1530 ℃ (higher than the liquidus temperature), the heating time of the heating riser is 30 hours, and a covering agent and a heating agent are used at the same time. 3) The carbon content of the first ladle of molten steel is 0.51%, the carbon content of the second ladle of molten steel is 0.45%, the carbon content of the third ladle of molten steel is 0.37%, and the continuous pouring time is 5200 seconds; Both weigh 150 tons.
[0041] Process six: steps 1), 2) and 4) are exactly the same as process five, but the carbon content of the third ladle of molten steel in step 3) is 0.30%.
[0042] Process seven: Steps 1), ...
PUM
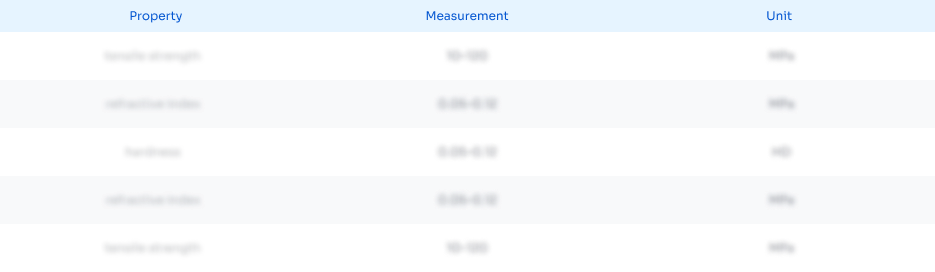
Abstract
Description
Claims
Application Information

- Generate Ideas
- Intellectual Property
- Life Sciences
- Materials
- Tech Scout
- Unparalleled Data Quality
- Higher Quality Content
- 60% Fewer Hallucinations
Browse by: Latest US Patents, China's latest patents, Technical Efficacy Thesaurus, Application Domain, Technology Topic, Popular Technical Reports.
© 2025 PatSnap. All rights reserved.Legal|Privacy policy|Modern Slavery Act Transparency Statement|Sitemap|About US| Contact US: help@patsnap.com