Preparation method for special precipitated calcium carbonate for PVC (polyvinyl chloride) stone chip resistant coating
A technology for precipitating calcium carbonate and coatings, applied in the direction of calcium carbonate / strontium / barium, coatings, etc., can solve problems such as unfavorable moisture control, difficulty in meeting the needs of filling high-grade PVC anti-stone chip coatings, and products are easy to absorb moisture, etc. Inhibition of solvation, simple and feasible method, low hygroscopic effect
- Summary
- Abstract
- Description
- Claims
- Application Information
AI Technical Summary
Problems solved by technology
Method used
Image
Examples
Embodiment 1
[0038] Dilute the milk of lime that has been refined and aged for 48 hours, adjust the specific gravity to 1.060, control the temperature at 20.0°C, and then transport it to the bubbling carbonization tower, and pass it into the purified and cooled kiln gas for carbonation reaction. The kiln gas flow rate is 9m 3 / h, the volume content of carbon dioxide is 33%, when the pH of the reaction solution drops below 7.0, the carbonation reaction is completed, and the specific surface area of cooked pulp is 24.8m 2 / g;
[0039] Prepare a compound surface treatment agent of 3.50% (calculated on a dry basis of calcium carbonate): among them, the fatty acid is selected from stearic acid: arachidic acid = 1:1, and its consumption is 60% of the total surface treatment agent, and the consumption of castor oil is the surface treatment 10% of the total amount of agent, the amount of epoxy soybean oil is 30% of the total amount of surface treatment agent, the temperature of hot water is 90 ...
Embodiment 2
[0043] Dilute the milk of lime that has been refined and aged for 48 hours, adjust the specific gravity to 1.070, control the temperature at 25°C, and then transport it to the bubbling carbonization tower with stirring; pass it into the purified and cooled kiln gas for carbonation reaction, The kiln gas flow rate is 10m 3 / h, the volume content of carbon dioxide is 33%, when the pH of the reaction solution drops below 7.0, the carbonation reaction is completed, and the specific surface area of cooked pulp is 21.3m 2 / g;
[0044]Prepare the compound surface treatment agent of 3.0% (calcium carbonate dry basis): wherein fatty acid selects stearic acid for use: behenic acid=1:3, and its consumption is 80% of surface treatment agent total amount, castor oil consumption is surface 12% of the total amount of treatment agent, the amount of epoxidized soybean oil is 8% of the total amount of surface treatment agent, the temperature of hot water is 90 ℃, and the consumption of sodiu...
Embodiment 3
[0048] Dilute the milk of lime that has been refined and aged for 48 hours, adjust the specific gravity to 1.055, control the temperature at 20°C, and then transport it to the bubbling carbonization tower with stirring; pass it into the purified and cooled kiln gas for carbonation reaction, The kiln gas flow rate is 10m 3 / h, the volume content of carbon dioxide is 35%, when the pH of the reaction solution drops below 7.0, the carbonation reaction is completed, and the specific surface area of cooked pulp is 31.7m 2 / g;
[0049] Prepare the composite surface treatment agent of 4.5% (in calcium carbonate dry basis): wherein fatty acid is selected stearic acid for use, and its consumption is 70% of surface treatment agent total amount, castor oil consumption is 20% of surface treatment agent total amount, The consumption of epoxy soybean oil is 10% of the total amount of surface treatment agent, the temperature of hot water is 95°C, and the consumption of sodium hydroxide is ...
PUM
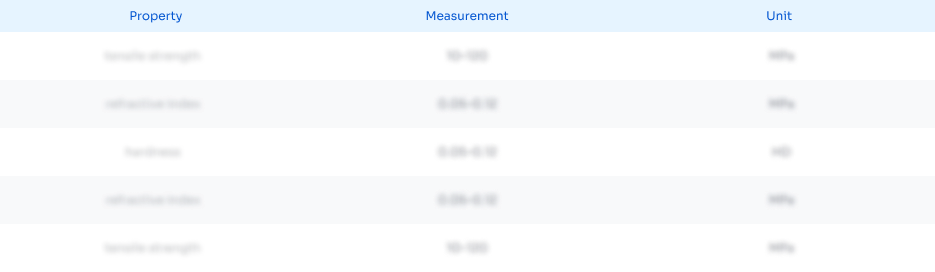
Abstract
Description
Claims
Application Information

- R&D
- Intellectual Property
- Life Sciences
- Materials
- Tech Scout
- Unparalleled Data Quality
- Higher Quality Content
- 60% Fewer Hallucinations
Browse by: Latest US Patents, China's latest patents, Technical Efficacy Thesaurus, Application Domain, Technology Topic, Popular Technical Reports.
© 2025 PatSnap. All rights reserved.Legal|Privacy policy|Modern Slavery Act Transparency Statement|Sitemap|About US| Contact US: help@patsnap.com