Method for synthesis of binary metal composite oxide by microwave sintering
A technology of composite oxides and binary metals, applied in the fields of rare earth metal compounds, chemical instruments and methods, preparation of alkaline earth metal aluminates/alumina/hydroxide, etc.
- Summary
- Abstract
- Description
- Claims
- Application Information
AI Technical Summary
Problems solved by technology
Method used
Examples
Embodiment 1
[0031] Take 5.10 g of yttrium oxide (Y 2 o 3 ), 6.00 g iron oxide (Fe 2 o 3 ), 1.20 g of activated carbon and 0.40 g of sucrose, were briefly ground into a powder mixture, and then added to a stainless steel tank of a ball mill together with 20 mL of distilled water for wet ball milling, and taken out after 3 h. After taking it out, put it in the oven at 110 o C and dried for 1 h, and pressed at 90 MPa to form a cylinder to be sintered. Put it into the MgO heat preservation tray, move it into the sintering microwave oven, at 1100 o C sintered for 50 min to obtain a sintered cylinder.
[0032] The sintered cylinder was sintered in a box-type resistance furnace at 400 o C heat treatment in air for 2 h to obtain the target product Y 3 Fe 5 o 12 .
Embodiment 2
[0034] Take 5.10 g of yttrium oxide (Y 2 o 3 ), 3.75 g alumina (Al 2 o 3 ), 1.90 g of activated carbon and 0.40 g of polyvinyl alcohol were simply ground into a powder mixture, and then added to the stainless steel tank of the ball mill together with 20 mL of alcohol for wet ball milling, and taken out after 4 h. After taking it out, put it in the oven at 90 o C and dried for 1 h, and pressed at 100 MPa to form a cylinder to be fired. Put it into the MgO heat preservation tray, move it into the sintering microwave oven, at 1200 o C sintered for 70 min to obtain a sintered cylinder.
[0035] The sintered cylinder was sintered in a box-type resistance furnace at 400 o C heat treatment in air for 2 h to obtain the target product Y 3 Al 5 o 12 .
Embodiment 3
[0037] Take 4.52 g yttrium oxide (Y 2 o 3 ), 1.20 g silicon dioxide (SiO 2 ), 1.10 g of activated carbon and 0.20 g of polyvinyl alcohol were simply ground into a powder mixture, and then added to the stainless steel tank of the ball mill together with 10 mL of alcohol for wet ball milling, and taken out after 4 h. After taking it out, put it in the oven at 90 o C and dried for 1 h, and pressed at 100 MPa to form a cylinder to be fired. Put it into the MgO heat preservation tray, move it into the sintering microwave oven, at 1100 o C sintered for 50 min to obtain a sintered cylinder.
[0038] The sintered cylinder was sintered in a box-type resistance furnace at 400 o C heat treatment in air for 2 h to obtain the target product Y 2 SiO 5 .
PUM
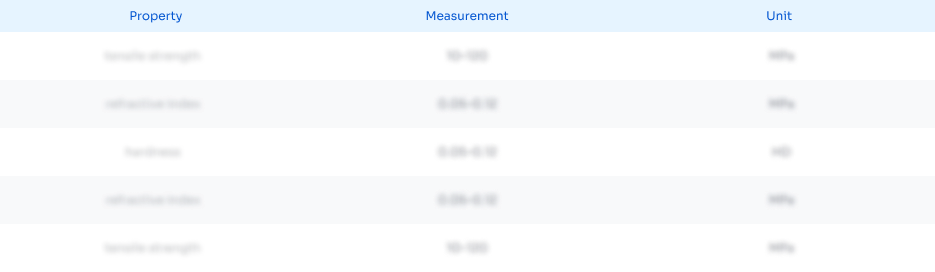
Abstract
Description
Claims
Application Information

- R&D
- Intellectual Property
- Life Sciences
- Materials
- Tech Scout
- Unparalleled Data Quality
- Higher Quality Content
- 60% Fewer Hallucinations
Browse by: Latest US Patents, China's latest patents, Technical Efficacy Thesaurus, Application Domain, Technology Topic, Popular Technical Reports.
© 2025 PatSnap. All rights reserved.Legal|Privacy policy|Modern Slavery Act Transparency Statement|Sitemap|About US| Contact US: help@patsnap.com