Composite molybdenum-based catalyst and preparation method and application thereof
A technology of composite molybdenum and catalyst, which is applied in the fields of energy and chemical industry, can solve the problems of complex catalyst composition, cumbersome preparation steps, poor repeatability, etc., and achieve the effect of stable phase structure, overcoming cumbersome preparation process and easy control of conditions
- Summary
- Abstract
- Description
- Claims
- Application Information
AI Technical Summary
Problems solved by technology
Method used
Image
Examples
Embodiment 1
[0035] Step 1: Reduction-Carbonization
[0036] Weigh a certain amount of ammonium molybdate (NH 4 ) 6 Mo 7 o 24 4H 2 O, roasted at 450°C for 4h, then weighed 10g of the above-mentioned roasted sample, put it into a quartz tube, placed it in a tube furnace, and controlled it by temperature programming, with CH 4 / H 2 As the carbonization medium, the reduction-carbonization process is carried out, and the specific process is as follows:
[0037] First, at N 2 Under atmospheric conditions (20mL / min), rise from room temperature to 450°C at 5°C / min; then, switch to CH 4 / H 2 Atmosphere (50mL / min), continue to heat up to 700°C at 1°C / min and keep for 4h; then, cool to room temperature; finally, switch to N 2 / O 2 Atmosphere (8mL / min), passivation for 5h, to obtain sample A. in N 2 / O 2 In, O 2 The content is 1v%.
[0038] Step 2: Wet Dipping
[0039] Weigh a certain amount of sample A, according to the molar ratio Mo:K=10:1, equal volume impregnation K 2 CO 3 , dr...
Embodiment 2
[0051] Step 1: Reduction-Carbonization
[0052] Weigh a certain amount of ammonium molybdate (NH 4 ) 6 Mo 7 o 24 4H 2 O, roasted at 500°C for 4 hours, then weighed 10 g of the above-mentioned roasted sample and put it into a quartz tube, placed it in a tube furnace, and controlled it by temperature programming, with CH 4 / H 2 As the carbonization medium, the reduction-carbonization process is carried out, and the specific process is as follows:
[0053] First, at N 2 Under atmospheric conditions (20mL / min), rise from room temperature to 450°C at 5°C / min; then, switch to CH 4 / H 2 Atmosphere (60mL / min), continue to heat up to 700°C at 1°C / min and keep for 5h; then, cool to room temperature; finally, switch to N 2 / O 2 Atmosphere (15mL / min), passivation for 10h, to obtain sample B. in N 2 / O 2 atmosphere, O 2 The content is 0.5v%.
[0054] Step 2: Wet Dipping
[0055] Weigh a certain amount of sample B, according to the molar ratio Mo:K=5:1, impregnate KNO 3 , d...
Embodiment 3
[0066] Step 1: Reduction-Carbonization
[0067] Weigh a certain amount of ammonium molybdate (NH 4 ) 6 Mo 7 o 24 4H 2 O, roasted at 600°C for 2 hours, then weighed 10 g of the sample obtained from the above roasting, put it into a quartz tube, placed it in a tube furnace, and controlled it by temperature programming, with CH 4 / H 2 As the carbonization medium, the reduction-carbonization process is carried out, and the specific process is as follows:
[0068] First, at N 2 Under atmospheric conditions (20mL / min), rise from room temperature to 450°C at 5°C / min; then, switch to CH 4 / H 2 Atmosphere (50mL / min), continue to heat up to 675°C at 1°C / min and keep for 5h; then, cool to room temperature; finally, switch to N 2 / O 2 Atmosphere (15mL / min), passivation for 5h, to obtain sample A. in N 2 / O 2 In, O 2 The content is 1v%.
[0069] Step 2: Wet Dipping
[0070] Weigh a certain amount of sample A, according to the molar ratio Mo:K=20:1, equal volume impregnation...
PUM
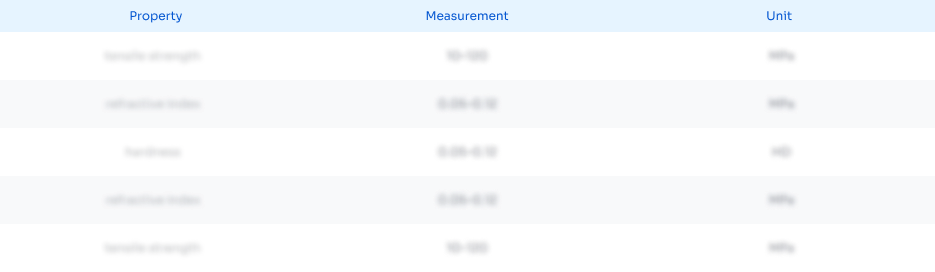
Abstract
Description
Claims
Application Information

- Generate Ideas
- Intellectual Property
- Life Sciences
- Materials
- Tech Scout
- Unparalleled Data Quality
- Higher Quality Content
- 60% Fewer Hallucinations
Browse by: Latest US Patents, China's latest patents, Technical Efficacy Thesaurus, Application Domain, Technology Topic, Popular Technical Reports.
© 2025 PatSnap. All rights reserved.Legal|Privacy policy|Modern Slavery Act Transparency Statement|Sitemap|About US| Contact US: help@patsnap.com