A highly dispersed monolithic catalyst for hydrogen peroxide synthesis and its preparation method and application
A technology of monolithic catalysts and catalysts, applied in molecular sieve catalysts, chemical instruments and methods, physical/chemical process catalysts, etc.
- Summary
- Abstract
- Description
- Claims
- Application Information
AI Technical Summary
Problems solved by technology
Method used
Image
Examples
Embodiment 1
[0055] 1) Coating preparation:
[0056] 10g γ-Al 2 o 3 , 10g Y-type molecular sieve, 4.2g KNO 3 , 60g of nitric acid solution with a concentration of 2wt.% is mixed in a 100ml ball mill tank, and the rotating speed of the ball mill is adjusted to 500r / min. After ball milling for 6 hours, the pH of the slurry is adjusted to be between 3-4 to obtain the catalyst molecular sieve-oxide Coating carrier slurry.
[0057] Select a monolithic catalyst carrier with a pore size of 400 holes / square inch, dip the coating carrier slurry for 3 minutes, then use compressed air to remove excess liquid slurry in the channel of the monolithic catalyst carrier, and repeat the above coating after drying. The coating step was carried out 3 times, and the weight of the coated catalyst promoter was weighed to be 16% of the overall catalyst carrier, and it was placed in a muffle furnace for calcination at 500° C. for 2 h.
[0058] 2) Active ingredient upload:
[0059] Get above-mentioned catalyst...
Embodiment 2
[0063] 1) Coating preparation:
[0064] 10g TiO 2 , 2g ZSM-5 molecular sieve, 60gH 2 O was mixed in a 100ml spherical ink tank, and the rotating speed of the ball mill was adjusted to 500r / min. After ball milling for 6 hours, the pH of the slurry was adjusted to be between 3-4 to obtain catalyst molecular sieve-oxide coating carrier slurry.
[0065] Select a monolithic catalyst carrier with a pore size of 400 holes / square inch, dip the coating carrier slurry for 3 minutes, then use compressed air to remove excess liquid slurry in the channel of the monolithic catalyst carrier, and repeat the above coating after drying. The coating step was carried out 3 times, and the weight of the coated catalyst promoter was weighed to be 23% of the overall catalyst carrier, and it was placed in a muffle furnace for calcination at 500° C. for 2 hours.
[0066] Take the above carrier impregnated with 0.1mol / L Mg(NO 3 ) 2 The solution was dried and then baked in a muffle furnace at 500°C f...
Embodiment 3
[0071] 1) Coating preparation:
[0072] SiO was crushed using a jet mill 2 , the β-type molecular sieve material is crushed to a particle size of 2-7μm, and then 5g of SiO 2 , 18gβ-type molecular sieve, add 3.7g K 2 SO 4 , 60gH 2 O, after stirring into a suspension, the catalyst molecular sieve-oxide-coated carrier slurry is obtained.
[0073] Select a monolithic catalyst carrier with a pore size of 400 holes / square inch, dip the coating carrier slurry for 3 minutes, then use compressed air to remove excess liquid slurry in the channel of the monolithic catalyst carrier, and repeat the above coating after drying. The coating step was carried out 3 times, and the weight of the coated catalyst promoter was weighed to be 32% of the overall catalyst carrier, and it was placed in a muffle furnace for calcination at 500° C. for 2 h.
[0074]The loading method and reduction process of the noble metal active component of the catalyst are the same as in Example 2 to obtain catalys...
PUM
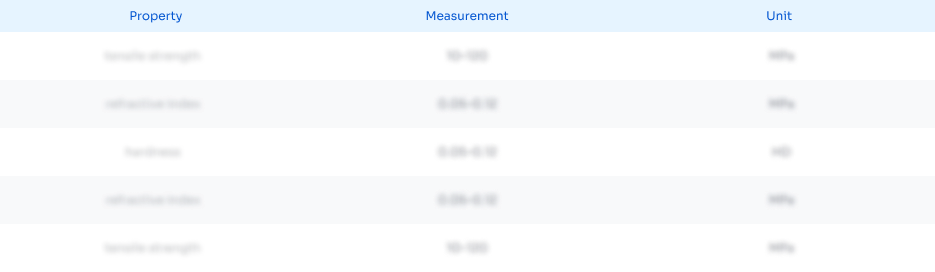
Abstract
Description
Claims
Application Information

- R&D Engineer
- R&D Manager
- IP Professional
- Industry Leading Data Capabilities
- Powerful AI technology
- Patent DNA Extraction
Browse by: Latest US Patents, China's latest patents, Technical Efficacy Thesaurus, Application Domain, Technology Topic, Popular Technical Reports.
© 2024 PatSnap. All rights reserved.Legal|Privacy policy|Modern Slavery Act Transparency Statement|Sitemap|About US| Contact US: help@patsnap.com