Method for preparing low-deformation polyurethane damping bumper block
A polyurethane and low-deformation technology, applied in the field of polymer material preparation, can solve the problem of high deformation rate, achieve the effect of reducing deformation rate, meeting requirements, and increasing chemical crosslinking
- Summary
- Abstract
- Description
- Claims
- Application Information
AI Technical Summary
Problems solved by technology
Method used
Image
Examples
Embodiment 1
[0032] Excessive diphenylmethane diisocyanate (MDI) reacts with carbodiimide to prepare -NCO group content 25% diphenylmethane diisocyanate with a certain degree of crosslinking; ℃ for 120 minutes to form a prepolymer with a -NCO group content of 10%; the molecular weight is 2000 polyether polyol is heated to 100 degrees, and the mass fraction of polyether polyol with a molecular weight of 2000 is 5% and the molecular weight is 4000. Propylene oxide polyol, adding accounted for molecular weight is 2000 polyether polyol mass fractions and is 3% water foaming agent, tin dioctoate and DC193 to obtain chain extender; Wherein the mass ratio of water foaming agent, dioctoate and DC193 3:1:5; use a low-pressure foaming machine to mix the prepolymer and chain extender at a mass ratio of 100:80; quickly inject the prepared mixture into a 70°C vulcanizer, quickly close the mold, and vulcanize for 15 minutes , demoulding; place the poured sample in an oven at 100°C and vulcanize for 24 h...
Embodiment 2
[0035] Excessive diphenylmethane diisocyanate (MDI) reacts with carbodiimide to prepare -NCO group content 20% diphenylmethane diisocyanate with a certain degree of crosslinking; ℃ for 120 minutes to form a prepolymer with a -NCO group content of 8%; the molecular weight is 2200 polyether polyol is heated up to 100 degrees, and the mass fraction of 2200 polyether polyol is added and the molecular weight is 5000. Propylene oxide polyol, adding accounted for molecular weight is 2200 and the mass fraction of polyether polyol is 2.5% water blowing agent, triethylenediamine and 3042 to obtain chain extender; Wherein water blowing agent, triethylenediamine The mass ratio of 3042 and 3042 is 3:1:5; use a low-pressure foaming machine to mix the prepolymer and chain extender in a mass ratio of 100:90; the prepared mixed material is quickly injected into the 70°C vulcanizing machine, and quickly Close the mold, vulcanize for 15 minutes, and demould; place the poured sample in an oven at...
Embodiment 3
[0038] Excessive diphenylmethane diisocyanate (MDI) reacts with carbodiimide to prepare -NCO group content 26% diphenylmethane diisocyanate with a certain degree of crosslinking; ℃ for 60 minutes to form a prepolymer with a -NCO group content of 6%; the molecular weight is 1800 polyether polyol is heated up to 100 degrees, and the mass fraction of 1800 polyether polyol is added, and the molecular weight is 10000 trifunctional polyol Tetrahydrofuran polyol, adding accounted for molecular weight is 1800 the mass fraction of polyether polyol and is 3.5% water blowing agent, triethylenediamine and 3042 to obtain chain extender; Wherein water blowing agent, triethylenediamine and 3042 The mass ratio is 3:1:5; use a low-pressure foaming machine to mix the prepolymer and the chain extender at a mass ratio of 100:80; the prepared mixed material is quickly injected into the 40°C vulcanizer, and the mold is quickly closed , vulcanized for 30 minutes, and demolded; place the poured sampl...
PUM
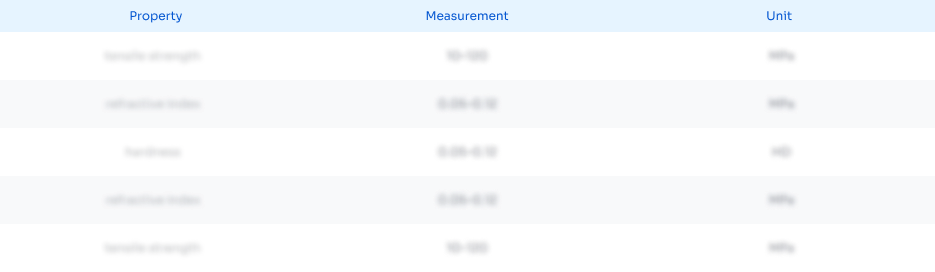
Abstract
Description
Claims
Application Information

- R&D
- Intellectual Property
- Life Sciences
- Materials
- Tech Scout
- Unparalleled Data Quality
- Higher Quality Content
- 60% Fewer Hallucinations
Browse by: Latest US Patents, China's latest patents, Technical Efficacy Thesaurus, Application Domain, Technology Topic, Popular Technical Reports.
© 2025 PatSnap. All rights reserved.Legal|Privacy policy|Modern Slavery Act Transparency Statement|Sitemap|About US| Contact US: help@patsnap.com