Rare-earth alloy permanent magnet material preparation device and technique
A technology of permanent magnet materials and rare earth alloys, applied in the direction of magnetic materials, magnetic objects, electrical components, etc., can solve the problems affecting the quality of mass production, low working temperature stability, segregation of alloy ingot materials, etc., and achieve welding performance and resistance The effect of improving corrosion performance, improving current utilization rate, and improving actual coercive force
- Summary
- Abstract
- Description
- Claims
- Application Information
AI Technical Summary
Problems solved by technology
Method used
Image
Examples
Embodiment 1
[0047] A kind of rare earth alloy permanent magnet material, according to the following table 1-1 for batching:
[0048] Table 1-1 Example 1 formula table
[0049] components
Nd+Pr
Dy
sc
B
co
Al
Fe
total
weight / kg
5.94
0.44
0.66
0.235
0.024
0.073
14.64
21.99
mass percentage / %
27
2
3
1.02
0.1
0.33
66.55
100
[0050] The preparation process of the above-mentioned rare earth alloy permanent magnet material of the present embodiment is as follows:
[0051] In the rare earth metal treatment tank 1, the rare earth raw materials are pretreated, acidolyzed, filtered, extracted and separated to obtain neodymium chloride, praseodymium chloride, dysprosium chloride and scandium chloride. The distribution ratio is required to prepare a chloride complex solution in the mixing tank 2, and settle the chloride complex solution to obtain the Nd Pr·Dy·Sc mixed coform, a...
Embodiment 2
[0056] A kind of rare earth alloy permanent magnet material, according to the following table 2-1 for batching:
[0057] Table 2-1 Example 2 formula table
[0058] components
Nd+Pr
Dy
sc
B
co
Al
Fe
total
weight / kg
5.5
0.66
0.88
0.24
0.033
0.092
14.61
22.015
mass percentage / %
25
3
4
1.04
0.15
0.42
66.39
100
[0059] The preparation process of the above-mentioned rare earth alloy permanent magnet material of the present embodiment is as follows:
[0060] In the rare earth metal treatment tank 1, the rare earth raw materials are pretreated, acidolyzed, filtered, extracted and separated to obtain neodymium chloride, praseodymium chloride, dysprosium chloride and scandium chloride. The distribution ratio is required to prepare a chloride complex solution in the mixing tank 2, and settle the chloride complex solution to obtain the Nd Pr·Dy·Sc mixed coform, a...
Embodiment 3
[0064] A kind of rare earth alloy permanent magnet material, according to the following table 3-1 for batching:
[0065] Table 3-1 Example 3 formula table
[0066] components
[0067] mass percentage / %
[0068] The preparation process of the above-mentioned rare earth alloy permanent magnet material of the present embodiment is as follows:
[0069] In the rare earth metal treatment tank 1, the rare earth raw materials are pretreated, acidolyzed, filtered, extracted and separated to obtain neodymium chloride, praseodymium chloride, dysprosium chloride and scandium chloride. The distribution ratio is required to prepare a chloride complex solution in the mixing tank 2, and settle the chloride complex solution to obtain the Nd Pr·Dy·Sc mixed coform, and then mix the Nd Pr·Dy·Sc mixed coform with other The prepared raw materials are put into the electrolytic furnace 6 for smelting so that the raw materials form molten alloy liquid, the smelting temperature is ...
PUM
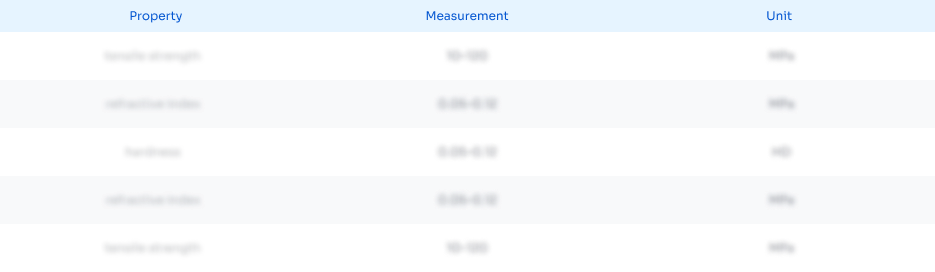
Abstract
Description
Claims
Application Information

- R&D
- Intellectual Property
- Life Sciences
- Materials
- Tech Scout
- Unparalleled Data Quality
- Higher Quality Content
- 60% Fewer Hallucinations
Browse by: Latest US Patents, China's latest patents, Technical Efficacy Thesaurus, Application Domain, Technology Topic, Popular Technical Reports.
© 2025 PatSnap. All rights reserved.Legal|Privacy policy|Modern Slavery Act Transparency Statement|Sitemap|About US| Contact US: help@patsnap.com